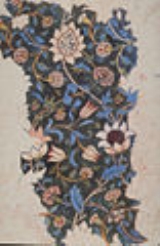
Textile printing
Encyclopedia
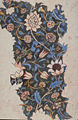
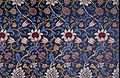
Textile
A textile or cloth is a flexible woven material consisting of a network of natural or artificial fibres often referred to as thread or yarn. Yarn is produced by spinning raw fibres of wool, flax, cotton, or other material to produce long strands...
in definite pattern
Pattern
A pattern, from the French patron, is a type of theme of recurring events or objects, sometimes referred to as elements of a set of objects.These elements repeat in a predictable manner...
s or designs. In properly printed
Printing
Printing is a process for reproducing text and image, typically with ink on paper using a printing press. It is often carried out as a large-scale industrial process, and is an essential part of publishing and transaction printing....
fabrics the colour is bonded with the fiber
Fiber
Fiber is a class of materials that are continuous filaments or are in discrete elongated pieces, similar to lengths of thread.They are very important in the biology of both plants and animals, for holding tissues together....
, so as to resist washing
Washing
Washing is one way of cleaning, namely with water and often some kind of soap or detergent. Washing is an essential part of good hygiene and health....
and friction
Friction
Friction is the force resisting the relative motion of solid surfaces, fluid layers, and/or material elements sliding against each other. There are several types of friction:...
. Textile printing is related to dyeing
Dyeing
Dyeing is the process of adding color to textile products like fibers, yarns, and fabrics. Dyeing is normally done in a special solution containing dyes and particular chemical material. After dyeing, dye molecules have uncut Chemical bond with fiber molecules. The temperature and time controlling...
but, whereas in dyeing proper the whole fabric is uniformly covered with one colour, in printing one or more colours are applied to it in certain parts only, and in sharply defined patterns.
In printing, wood
Wood
Wood is a hard, fibrous tissue found in many trees. It has been used for hundreds of thousands of years for both fuel and as a construction material. It is an organic material, a natural composite of cellulose fibers embedded in a matrix of lignin which resists compression...
en blocks, stencil
Stencil
A stencil is a thin sheet of material, such as paper, plastic, or metal, with letters or a design cut from it, used to produce the letters or design on an underlying surface by applying pigment through the cut-out holes in the material. The key advantage of a stencil is that it can be reused to...
s, engrave
Engraving
Engraving is the practice of incising a design on to a hard, usually flat surface, by cutting grooves into it. The result may be a decorated object in itself, as when silver, gold, steel, or glass are engraved, or may provide an intaglio printing plate, of copper or another metal, for printing...
d plates, rollers, or silkscreens are used to place colours on the fabric. Colourants used in printing contain dyes thickened to prevent the colour from spreading by capillary attraction beyond the limits of the pattern or design.
Traditional textile printing techniques may be broadly categorised into four styles:
- Direct printing, in which colourants containing dyes, thickeners, and the mordantMordantA mordant is a substance used to set dyes on fabrics or tissue sections by forming a coordination complex with the dye which then attaches to the fabric or tissue. It may be used for dyeing fabrics, or for intensifying stains in cell or tissue preparations. The term mordant comes from the Latin...
s or substances necessary for fixingFixativeA fixative is a stabilizing or preservative agent:*Fixative , a liquid usually sprayed over a finished piece of artwork to better preserve it and prevent smudging...
the colour on the cloth are printed in the desired pattern. - The printing of a mordant in the desired pattern prior to dyeing cloth; the color adheres only where the mordant was printed.
- Resist dyeingResist dyeingResist dyeing is a term for a number of traditional methods of dyeing textiles with patterns. Methods are used to "resist" or prevent the dye from reaching all the cloth, thereby creating a pattern and ground. The most common forms use wax, some type of paste, or a mechanical resist that...
, in which a waxWaxthumb|right|[[Cetyl palmitate]], a typical wax ester.Wax refers to a class of chemical compounds that are plastic near ambient temperatures. Characteristically, they melt above 45 °C to give a low viscosity liquid. Waxes are insoluble in water but soluble in organic, nonpolar solvents...
or other substance is printed onto fabric which is subsequently dyed. The waxed areas do not accept the dye, leaving uncoloured patterns against a coloured ground. - Discharge printing, in which a bleachBleachBleach refers to a number of chemicals that remove color, whiten, or disinfect, often via oxidation. Common chemical bleaches include household chlorine bleach , lye, oxygen bleach , and bleaching powder...
ing agent is printed onto previously dyed fabrics to remove some or all of the colour.
Resist and discharge techniques were particularly fashionable in the 19th century, as were combination techniques in which indigo
Indigo dye
Indigo dye is an organic compound with a distinctive blue color . Historically, indigo was a natural dye extracted from plants, and this process was important economically because blue dyes were once rare. Nearly all indigo dye produced today — several thousand tons each year — is synthetic...
resist was used to create blue backgrounds prior to block-printing of other colours. Most modern industrialised printing uses direct printing techniques.
Origins
Woodblock printingWoodblock printing
Woodblock printing is a technique for printing text, images or patterns used widely throughout East Asia and originating in China in antiquity as a method of printing on textiles and later paper....
is a technique for printing
Printing
Printing is a process for reproducing text and image, typically with ink on paper using a printing press. It is often carried out as a large-scale industrial process, and is an essential part of publishing and transaction printing....
text, images or patterns used widely throughout East Asia
East Asia
East Asia or Eastern Asia is a subregion of Asia that can be defined in either geographical or cultural terms...
and probably originating in China
China
Chinese civilization may refer to:* China for more general discussion of the country.* Chinese culture* Greater China, the transnational community of ethnic Chinese.* History of China* Sinosphere, the area historically affected by Chinese culture...
in antiquity as a method of printing on textile
Textile
A textile or cloth is a flexible woven material consisting of a network of natural or artificial fibres often referred to as thread or yarn. Yarn is produced by spinning raw fibres of wool, flax, cotton, or other material to produce long strands...
s and later paper
Paper
Paper is a thin material mainly used for writing upon, printing upon, drawing or for packaging. It is produced by pressing together moist fibers, typically cellulose pulp derived from wood, rags or grasses, and drying them into flexible sheets....
. As a method of printing on cloth, the earliest surviving examples from China
China
Chinese civilization may refer to:* China for more general discussion of the country.* Chinese culture* Greater China, the transnational community of ethnic Chinese.* History of China* Sinosphere, the area historically affected by Chinese culture...
date to before 220, and from Egypt
Egypt
Egypt , officially the Arab Republic of Egypt, Arabic: , is a country mainly in North Africa, with the Sinai Peninsula forming a land bridge in Southwest Asia. Egypt is thus a transcontinental country, and a major power in Africa, the Mediterranean Basin, the Middle East and the Muslim world...
to the 4th century.
Textile printing was known in Europe, via the Islamic world, from about the 12th century, and widely used. However, the European dyes tended to run, which restricted the use of printed patterns. Fairly large and ambitious designs were printed for decorative purposes such as wall-hangings and lectern
Lectern
A lectern is a reading desk with a slanted top, usually placed on a stand or affixed to some other form of support, on which documents or books are placed as support for reading aloud, as in a scripture reading, lecture, or sermon...
-cloths, where this was less of a problem as they did not need washing. When paper became common, the technology was rapidly used on that for woodcut
Woodcut
Woodcut—occasionally known as xylography—is a relief printing artistic technique in printmaking in which an image is carved into the surface of a block of wood, with the printing parts remaining level with the surface while the non-printing parts are removed, typically with gouges...
prints
Old master print
An old master print is a work of art produced by a printing process within the Western tradition . A date of about 1830 is usually taken as marking the end of the period whose prints are covered by this term. The main techniques concerned are woodcut, engraving and etching, although there are...
. Superior cloth was also imported from Islamic countries, but this was much more expensive.
The Incas of Peru, Chile and the Aztecs of Mexico also practiced textile printing previous to the Spanish Invasion in 1519; but, owing to the imperfect character of their records before that date, it is impossible to say whether they discovered the art for themselves, or, in some way, learned its principles from the Asiatics.
During the latter half of the 17th century the French brought directly by sea, from their colonies on the east coast of India, samples of Indian blue and white resist prints, and along with them, particulars of the processes by which they had been produced, which produced washable fabrics.
Technology
Textile printing was introduced into England in 1676 by an French refugee who opened works, in that year, on the banks of the Thames near Richmond. Curiously enough this is the first print-works on record; but the nationality and political status of its founder are sufficient to prove that printing was previously carried on in France. In Germany, too, textile printing was in all probability well established before it spread to England, for, towards the end of the 17th century, the district of Augsburg was celebrated for its printed linens, a reputation not likely to have been built up had the industry been introduced later than 1676.On the continent of Europe the commercial importance of calico printing seems to have been almost immediately recognized, and in consequence it spread and developed there much more rapidly than in England, where it was neglected and practically at a standstill for nearly ninety years after its introduction. During the last two decades of the 17th century and the earlier ones of the 18th new works were started in France, Germany, Switzerland and Austria; but it was only in 1738 that calico printing was first, practiced in Scotland, and not until twenty-six years later that Messrs Clayton of Bamber Bridge, near Preston, established in 1764 the first print-works in Lancashire, and thus laid the foundation of the industry. At the present time calico printing is carried on extensively in every quarter of the globe, and it is pretty safe to say that there is scarcely a civilized country in either hemisphere where a print-works does not exist.
From an artistic point of view most of the pioneer work in calico printing was done by the French; and so rapid was their advance in this branch of the business that they soon came to be acknowledged as its leading exponents. Their styles of design and schemes of colour were closely followed-even deliberately copied by all other European printers; and, from the early days of the industry down to the latter half of the 20th century, the productions of the French printers in Jouy, Beauvais, Rouen, Alsace-Lorraine, &c., were looked upon as representing all that was best in artistic calico printing. This reputation was established by the superiority of their earlier work, which, whatever else it may have lacked, possessed in a high degree the two main qualities essential to all good decorative work, viz., appropriateness of pattern and excellency of workmanship. If, occasionally, the earlier designers permitted themselves to indulge in somewhat bizarre fancies, they at least carefully refrained from any attempt to produce those pseudo-realistic effects the undue straining after which in later times ultimately led to the degradation of not only French calico printing design, but of that of all other European nations who followed their lead. The practice of the older craftsmen, at their best, was to treat their ornament in a way at once broad, simple and direct, thoroughly artistic and perfectly adapted to the means by which it had to be reproduced. The result was that their designs were characterized, on the one hand, by those qualities of breadth, flatness of field, simplicity of treatment arid pureness of tint so rightly prized by the artist; and, on the other, by their entire freedom from those meretricious effects of naturalistic projection and recession so dear to the modern mind and so utterly opposed to the principles of applied art.
Methods of printing
There are seven distinct methods at present in use for producing coloured patterns on cloth:Hand block printing
This process, though considered by some to be the most artistic, is the earliest, simplest and slowest of all methods of printing.In this process, a design is drawn on, or transferred to, a prepared wooden block. A separate block is required for each distinct colour in the design.
A blockcutter carves out the wood around the heavier masses first, leaving the finer and more delicate work until the last so as to avoid any risk of injuring it during the cutting of the coarser parts. When finished, the block presents the appearance of flat relief carving, with the design standing out.
Fine details are very difficult to cut in wood, and, even when successfully cut, wear down very rapidly or break off in printing. They are therefore almost invariably built up in strips of brass or copper, bent to shape and driven edgewise into the flat surface of the block. This method is known as coppering.
To print the design on the fabric, the printer applies colour to the block and presses it firmly and steadily on the cloth, ensuring a good impression by striking it smartly on the back with a wooden mallet. The second impression is made in the same way, the printer taking care to see that it fits exactly to the first, a point which he can make sure of by means of the pins with which the blocks are provided at each corner and which are arranged in such a way that when those at the right side or at the top of the block fall upon those at the left side or the bottom of the previous impression the two printings join up exactly and continue the pattern without a break. Each succeeding impression is made in precisely the same manner until the length of cloth is fully printed. When this is done it is wound over the drying rollers, thus bringing forward a fresh length to be treated similarly.
If the pattern contains several colours the cloth is usually first printed throughout with one, then dried, and printed with the second, the same operations being repeated until all the colours are printed.
Block printing by hand is a slow process it is, however, capable of yielding highly artistic results, some of which are unobtainable by any other method.
Perrotine printing
The perrotine is a block-printing machine invented by Perrot of Rouen in 1834, and practically speaking is the only successful mechanical device ever introduced for this purpose. For some reason or other it has rarely been used in England, but its value was almost immediately recognized on the Continent, and although block printing of all sorts has been replaced to such an enormous extent by roller printing, the perrotine is still largely employed in French, German and Italian works.The construction of this ingenious machine is too complex to describe here without the aid of several detailed drawings, but its mode of action is roughly as follows: Three large blocks (3 ft. long by 3 to 5 in. wide), with the pattern cut or cast on them in relief, are brought to bear successively on the three faces of a specially constructed printing table over which the cloth passes (together with its backing of printers blanket) after each impression. The faces of the table are arranged at right angles to each other, and the blocks work in slides similarly placed, so that their engraved faces are perfectly parallel to the tables. Each block is moreover provided with its own particular colour trough, distributing brush, and woolen colour pad or sieve, and is supplied automatically with colour by these appliances during the whole time that the machine is in motion. The first effect of starting the machine is to cause the colour sieves, which have a reciprocating motion, to pass over, and receive a charge of colour from, the rollers, fixed to revolve, in the colour troughs. They then return to their original position between the tables and the printing blocks, coming in contact on the way with the distributing brushes, which spread the colour evenly over their entire surfaces. At this point the blocks advance and are gently pressed twice against the colour pads (or sieves) which then retreat once more towards the colour troughs. During this last movement the cloth to be printed is drawn forward over the first table, and, immediately the colour pads are sufficiently out of the way, the block advances and, with some force, stamps the first impression on it. The second block is now put into gear and the foregoing operations are repeated for both blocks, the cloth advancing, after each impression, a distance exactly equal to the width of the blocks. After the second block has made its impression the third comes into play in precisely the same way, so that as the cloth leaves the machines it's fully printed in three separate colours, each fitting into its proper place and completing the pattern. If necessary the forward movement of the cloth can be arrested without in any way interfering with the motion of the block, san arrangement which allows any insufficiently printed impression to be repeated in exactly the same place with a precision practically impossible in hand printing.
For certain classes of work the perrotine possesses great advantages over the hand-block; for not only is the rate of production greatly increased, but the joining up of the various impressions to each other is much more exacting fact, as a rule, no sign of a break in continuity of line can be noticed in well-executed work. On the other hand, however, the perrotine can only be applied to the production of patterns containing not more than three colours nor exceeding five inches in vertical repeat, whereas hand block printing can cope with patterns of almost any scale and continuing any number of colours. All things considered, therefore, the two processes cannot be compared on the same basis: the perrotine is best for work of a utilitarian character and the hand-block for decorative work in which the design only repeats every 15 to 20 in. and contains colours varying in number from one to a dozen. -
Engraved copperplate printing
The printing of textiles from engraved copperplates was first practiced in the United Kingdom by Thomas Bell in 1770.The presses first used were of the ordinary letterpress type, the engraved plate being fixed in the place of the type. In later improvements the well-known cylinder press was employed; the plate was inked mechanically and cleaned off by passing under a sharp blade of steel; and the cloth, instead of being laid on the plate, was passed round the pressure cylinder. The plate was raised into frictional contact with the cylinder and in passing under it transferred its ink to the cloth.
The great difficulty in plate printing was to make the various impressions join up exactly; and, as this could never be done with any certainty, the process was eventually confined to patterns complete in one repeat, and was made obsolete by roller printing.
Roller printing, cylinder printing, or machine printing
This elegant and efficient process was patented and worked by Bell in 1785 only fifteen years after his application of the engraved plate to textiles. Bell's first patent was for a machine to print six colours at once, but, owing probably to its incomplete development, this was not immediately successful, although the principle of the method was shown to be practical by the printing of one colour with perfectly satisfactory results. The difficulty was to keep the six rollers, each carrying a portion of the pattern, in perfect register with each other. This defect was soon overcome by Adam Parkinson of Manchester, and in 1785, the year of its invention, Bells machine with Parkinson's improvement was successfully employed by Messrs Livesey, Hargreaves, Hall & Co., of Bamber Bridge, Preston, for the printing of calico in from two to six colours at a single operation.The advantages possessed by roller printing over other contemoporary processes were three: firstly, its high productivity, 10,000 to 12,000 yards being commonly printed in one day of ten hours by a single-colour machine; secondly, by its capacity of being applied to the reproduction of every style of design, ranging from the fine delicate lines of copperplate engraving and the small repeats and limited colours of the perrotine to the broadest effects of block printing and to patterns varying in repeat from I to 80 in.; and thirdly, the wonderful exactitude with which each portion of an elaborate multicolour pattern can be fitted into its proper place without faulty joints at its points of repetition.
Stencil printing
The art of stenciling is very new. It has been applied to the decoration of textile fabrics from time immemorial by the Japanese, and, of late years, has found increasing employment in Europe for certain classes of decorative work on woven goods for furnishing purposes.The pattern is cut out of a sheet of stout paper or thin metal with a sharp-pointed knife, the uncut portions representing the part that is to be reserved or left uncoloured. The sheet is now laid on the material to be decorated and colour is brushed through its interstices.
It is obvious that with suitable planning an all over pattern may be just as easily produced by this process as by hand or machine printing, and that moreover, if several plates are used, as many colours as plates may be introduced into it. The peculiarity of stenciled patterns is that they have to be held together by ties, that is to say, certain parts of them have to be left uncut, so as to connect them with each other, and prevent them from falling apart in separate pieces. For instance, a complete circle cannot be cut without its center dropping out, and, consequently, its outline has to be interrupted at convenient points by ties or uncut portions. Similarly with other objects. The necessity for ties exercises great influence on the design, and in the hands of a designer of indifferent ability they may be very unsightly. On the other hand, a capable man utilizes them to supply the drawing, and when thus treated they form an integral part of the pattern and enhance its artistic value whilst complying with the conditions and the process.
For single-colour work a stenciling machine was patented in 1894 by S. H. Sharp. It consists of an endless stencil plate of thin sheet steel that passes continuously over a revolving cast iron cylinder. Between the two the cloth to be ornamented passes and the colour is forced on to it, through the holes in the stencil, by mechanical means.
Screen-printing
Screen printing is by far the most used technology today. Two types exist: rotary screen printing and flat (bed) screen printing. A blade squeezes the printing paste through openings in the screen onto the fabric.Digital textile printing
Digital textile printingDigital textile printing
Digital textile printing is described as any ink jet based method of printing colorants onto fabric. Most notably, digital textile printing is referred to when identifying either printing smaller designs onto garments and printing larger designs onto large format rolls of textile...
, often referred to as direct to garment printing, DTG printing, and digital garment printing is a process of printing on textiles and garments using specialized or modified inkjet technology. Inkjet printing on fabric is also possible with an inkjet printer by using fabric sheets with a removable paper backing. Today major inkjet technology manufacturers can offer specialized products designed for direct printing on textiles, not only for sampling but also for bulk production. Since the early 1990's, inkjet technology and specially developed water-based ink (known as dye-sublimation or disperse direct ink) has offered the possibility of printing directly onto polyester fabric. This is mainly related to visual communication in retail and brand promotion (flags, banners and other point of sales applications). Printing onto nylon and silk can be done by using an acid ink. Reactive ink is used for cellulose based fibers, such as cotton and linen. Using inkjet technology in digital textile printing allows for single pieces, mid-run production and even long-run alternatives to screen printed fabric.
Other methods of printing
Although most work is executed throughout by one or other of the seven distinct processes mentioned above, combinations of them are frequently employed. Sometimes a pattern is printed partly by machine and partly by block; and sometimes a cylindrical block is used along with engraved copper-rollers in the ordinary printing machine. The block in this latter case is in all respects, except that of shape, identical with a flat wood or coppered block, but, instead of being dipped in colour, it receives its supply from an endless blanket, one part of which works in contact with colour-furnishing rollers and the other part with the cylindrical block. This block is known as a surface or peg roller. Many attempts have been made to print multicolour patterns with surface rollers alone, but hitherto with little success, owing to their irregularity in action and to the difficulty of preventing them from warping. These defects are not present in the printing of linoleum in which opaque oil colours are used, colours that neither sink into the body of the hard linoleum nor tend to warp the roller.'Inkjet Printing on Fabric'is a way anyone can print on fabric using their home printer. Specially treated Cotton as well as various types of Silk fabric sheets are available in various sizes. The fabric sheets have a paper backing which enable the fabric to go through the printer. Family photos printed on fabric are used to make memory quilts, pillows, notebook covers, wall hangings and many other products.The printing of yarns and warping is extensively practiced. It is usually carried on by a simple sort of surface printing machine and calls for no special mention.
Lithographic printing, too, has been applied to textile fabrics with somewhat qualified success. Its irregularity and the difficulty of printing all over patterns to repeat properly, have restricted its use to the production of decorative panels, equal in size to that of the plate or stone, and complete in themselves.
Pad printing
Pad printing
Pad printing is a printing process that can transfer a 2-D image onto a 3-D object. This is accomplished using an indirect offset printing process that involves an image being transferred from the cliché via a silicone pad onto a substrate...
has been recently introduced to textile printing for the specific purpose of printing garment tags (care labels).
Preparation of cloth for printing
Goods intended for calico printing ought to be exceptionally well-bleached, otherwise stains, and other serious defects, are certain to arise during subsequent operations.The chemical preparations used for special styles will be mentioned in their proper places; but a general prepare, employed for most colours that are developed and fixed by steaming only, consists in passing the bleached calico through a weak solution of sulfated or turkey red oil containing from 21/2 per cent, to 5 per cent, of fatty acid. Some colours are printed on pure bleached cloth, but all patterns containing alizarine red, rose and salmon shades, are considerably brightened by the presence of oil, and indeed very few, if any, colours are detrimentally affected by it.
Apart from wet preparations the cloth has always to be brushed, to free it from loose nap, flocks and dust that it picks up whilst stored. Frequently, too, it has to be sheared by being passed over rapidly revolving knives arranged spirally round an axle, which rapidly and effectually cuts off all filaments and knots, leaving the cloth perfectly smooth and clean and in a condition fit to receive impressions of the most delicate engraving. Some figured fabrics, especially those woven in checks, stripes and crossovers, require very careful stretching and straightening on a special machine, known as a stenter, before they can be printed with certain formal styles of pattern which are intended in one way or another to correspond with the cloth pattern. Finally, all descriptions of cloth are wound round hollow wooden or iron centers into rolls of convenient size for mounting on the printing machines.
Preparation of colours
The art of making colours for textile printing demands both chemical knowledge and extensive technical experience, for their ingredients must not only be properly proportioned to each other, but they must be specially chosen and compounded for the particular style of work in hand. For a pattern containing only one colour any mixture whatever may he used so long as it fulfils all conditions as to shade, quality and fastness; but where two or more colours are associated in the same design each must be capable of undergoing without injury the various operations necessary for the development and fixation of the others.All printing pastes whether containing colouring matter or not are known technically as colours, and are referred to as such in the sequence.
Colours vary considerably in composition. The greater number of them contain all the elements necessary for the direct production and fixation of the colour-lake. Some few contain the colouring matter alone and require various after-treatments for its fixation; and others again are simply mordants thickened. A mordant is the metallic salt or other substance that combines with the colouring principle to form an insoluble colour-lake, either directly by steaming, or indirectly by dye
Dye
A dye is a colored substance that has an affinity to the substrate to which it is being applied. The dye is generally applied in an aqueous solution, and requires a mordant to improve the fastness of the dye on the fiber....
ing.
All printing colours require thickening, for the twofold object of enabling them to be transferred from colour-box to cloth without loss and to prevent them from running or spreading beyond the limits of the pattern.
Selecting thickening agents
The printing thickeners used depend on the printing technique and fabric and dyestuff used. Typical thickening agents are starch derivatives, flour, gum arabic, guar gumGuar gum
Guar gum, also called guaran, is a galactomannan. It is primarily the ground endosperm of guar beans. The guar seeds are dehusked, milled and screened to obtain the guar gum. It is typically produced as a free-flowing, pale, off-white-colored, coarse to fine ground powder.-Production:Guar gum is an...
derivatives, tamarind
Tamarind
Tamarind is a tree in the family Fabaceae. The genus Tamarindus is monotypic .-Origin:...
, sodium alginate, sodium polyacrylate
Sodium polyacrylate
Sodium polyacrylate, also known as waterlock, is a polymer with the chemical formula [-CH2-CH-]n widely used in consumer products. It has the ability to absorb as much as 200 to 300 times its mass in water. Acrylate polymers generally are considered to possess an anionic charge...
, gum Senegal and gum tragacanth, British gum or dextrine and albumen.
Hot water soluble tickening agents as native starch are made into pastes by boiling in double or jacketed pans, between the inner and outer casings of which either steam or water may be made to circulate, for boiling and cooling purposes. Mechanical agitators are also fitted in these pans to mix the various ingredients together, and to destroy lumps and prevent the formation of lumps, keeping the contents thoroughly stirred up during the whole time they are being boiled and cooled to make a smooth paste. Most thickening agents used today are cold soluble and require only extensive stirring.
Starch paste
This is made from wheat starch, cold water, and olive oil, and boiled for thickening.Non modified Starch
Starch
Starch or amylum is a carbohydrate consisting of a large number of glucose units joined together by glycosidic bonds. This polysaccharide is produced by all green plants as an energy store...
was the most extensively used of all the thickenings. It is applicable to all but strongly alkaline or strongly acid colours. With the former it thickens up to a stiff unworkable jelly, while mineral acids or acid salts convert it into dextrine, thus diminishing its viscosity
Viscosity
Viscosity is a measure of the resistance of a fluid which is being deformed by either shear or tensile stress. In everyday terms , viscosity is "thickness" or "internal friction". Thus, water is "thin", having a lower viscosity, while honey is "thick", having a higher viscosity...
or thickening power. Acetic and formic acids have no action on it even at the boil. Today mostly modified carboxymethylated cold soluble starches
Modified starch
Modified starch, also called starch derivatives, are prepared by physically, enzymatically, or chemically treating native starch, thereby changing the properties of the starch. Modified starches are used in practically all starch applications, such as in food products as a thickening agent,...
are used which have a stable viscosity and are easier to rinse out of the fabric and give reproducible "short" pasty rheology
Rheology
Rheology is the study of the flow of matter, primarily in the liquid state, but also as 'soft solids' or solids under conditions in which they respond with plastic flow rather than deforming elastically in response to an applied force....
.
Flour paste is made in a similar way to starch paste. At the present time it is rarely used for anything but the thickening of aluminum and iron mordants.
In the impressive textile traditions of Japan, several techniques using starch paste resists of rice flour have been perfected over several centuries.
Gums
Gum arabicGum arabic
220px|thumb|right|Acacia gumGum arabic, also known as acacia gum, chaar gund, char goond, or meska, is a natural gum made of hardened sap taken from two species of the acacia tree; Acacia senegal and Acacia seyal...
and gum Senegal are both very old thickenings, but their expense prevents them from being used for any but pale delicate tints. They are especially useful thickenings for the light ground colours of soft muslins and sateens on account of the property they possess of dissolving completely out of the fibers of the cloth in the washing process after printing and have a long flowing, viscous rheology, giving sharp print and good penetration in the cloth. Today guar gum and tamarind derivates offer a cheaper alternative.
British gum or dextrin
Dextrin
Dextrins are a group of low-molecular-weight carbohydrates produced by the hydrolysis of starch or glycogen. Dextrins are mixtures of polymers of D-glucose units linked by α- or α- glycosidic bonds....
is prepared by heating starch. It varies considerably in composition sometimes being only slightly roasted and consequently only partly converted into dextrine, and at other times being highly torrefied, and almost completely soluble in cold water and very dark in colour. Its thickening power decreases and its gummy nature increases as the temperature at which it is roasted is raised. The lighter coloured gums or dextrines will make a good thickening with from 2 to 3 lb of gum to one gallon of water, but the darkest and most highly calcined require from 6 to lb per gallon to give a substantial paste. Between these limits all qualities are obtainable. The darkest qualities are very useful for strongly acid colours, and with the exception of gum Senegal, are the best for strongly alkaline colours and discharges.
Like the natural gums, neither light nor dark British gums penetrate as well into the fiber of the cloth so deeply as pure starch or flour, and are therefore unsuitable for very dark strong colours.
Gum tragacanth, or Dragon, is one of the most indispensable thickening agents possessed by the textile printer. It may be mixed in any proportion with starch or flour and is equally useful for pigment colours and mordant colours. When added to starch paste it increases its penetrative power, adds to its softness without diminishing its thickness, makes it easier to wash Out of the fabric and produces much more level colours than starch paste alone. Used by itself it is suitable for printing all kinds of dark grounds on goods that are required to retain their soft clothy feel. A tragacanth mucilage may be made either by allowing it to stand a day or two in contact with cold water or by soaking it for twenty-four hours in warm water and then boiling it up until it is perfectly smooth and homogeneous. If boiled under pressure it gives a very fine, smooth mucilage (not a solution proper), much thinner than if made in the cold.
Starch always leave on the printed cloth somewhat harsh in feel (unless modified carboxymethylated starches are used) but are well suited to obtain very dark colours. Gum Senegal, gum arabic or modified guar gum thickening are yielding beautifully clear and perfectly even tints comparing to starch, but give lighter colours and are washedaway too much during the rinsing or washing of the printed fabric and are thuss less suited for very dark colours. (The gums are apparently preventing the colours from combining fully with the fibers.) So a printing stock solution is mostly a combination of modified starch and gum stock solutions usually made by dissolving 6 or 8 lb of either in one gallon of water.
Albumen
Albumen is both a thickening and a fixing agent for insoluble pigments such as chrome yellow, the ochres, vermilion and ultramarine. Albumen is always dissolved in the cold, a process that takes several days when large quantities are required. The usual strength of the solution is 4 lb per gallon of water for blood albumen, and 6 lb per gallon for egg albumen. The latter is expensive and only used for the lightest shades. For most purposes one part of albumen solution is mixed with one part of tragacanth mucilage, this proportion of albumen being found amply sufficient for the fixation of all ordinary pigment colours. In special instances the blood albumen solution is made as strong as 50 per cent, but this is only in cases where very dark colours are required to be absolutely fast to washing. After printing, albumen thickened colours are exposed to hot steam, which coagulates the albumen and effectually fixes the colours.Printing thickeners and the dye system
Combinations of cold water soluble carboxymethylated starch, guar gum and tamarind derivatives are most commonly used today in disperse screen printing on polyester, for cotton printing with reactive dyeReactive dye
In a reactive dye a chromophore contains a substituent that is activated and allowed to directly react to the surface of the substrate. Reactive dyes have good fastness properties owing to the bonding that occurs during dyeing....
s alginates are used, sodium polyacrylates for pigment
Pigment
A pigment is a material that changes the color of reflected or transmitted light as the result of wavelength-selective absorption. This physical process differs from fluorescence, phosphorescence, and other forms of luminescence, in which a material emits light.Many materials selectively absorb...
printing and with vat dye
Vat dye
Vat dyes are an ancient class of dyes, based on the natural dye, indigo, which is now produced synthetically.-Overview:The process "vat dyeing" refers to dyeing in a bucket or vat. It can be performed whenever a liquid, even shade over the entire garment is desired. Almost any dye can be used,...
s on cotton only carboxymethylated starch is used.
Printing paste preparation
Formerly colours were always prepared for printing by boiling the thickening agent, the colouring matter and solvents, &c., together, then cooling and adding the various fixing agents. At the present time, however, concentrated solutions of the colouring matters and other adjuncts are often simply added to the cold thickenings, of which large quantities are kept in stock.Colours are reduced in shade by simply adding more stock (printing) paste. For example, a dark blue containing 4 oz. of methylene blue per gallon may readily be made into a pale shade by adding to it thirty times its bulk of starch paste or gum, as the case may be. Similarly with other colours.
Before printing it is very essential to strain or sieve all colours in order to free them from lumps, fine sand, &c., which would inevitably damage the highly polished surface of the engraved rollers and result in bad printing. Every scratch on the surface of a roller prints a fine line in the cloth, and too much care, therefore, cannot be taken to remove, as far as possible, all grit and other hard particles from every colour.
The straining is usually done by squeezing the colour through filter cloths as artisanal fine cotton, silk or industrial woven nylon. Fine sieves can also be employed for colours that are used hot or are very strongly alkaline or acid.
Silk printing
Silk printing calls for no special mention. The colours and methods employed are the same as for wool, except that in the case of silk no preparation of the material is required before printing and the ordinary dry steaming is preferable to damp steaming.Both acid and basic dyes play an important role in silk printing, which for the most part is confined to the production of articles for wearing apparel dress goods, handkerchiefs, scarves, articles for which bright colours are in demand. Alizarine and other mordant colours are mainly used, or ought to be, for any goods that have to resist repeated washings and prolonged exposure to light. In this case the silk frequently requires to be prepared in alizarine oil, after which it is treated in all respects like cotton steamed, washed and soaped the colours used being the same.
Silk is especially adapted to discharge and reserve effects. Most of the acid dyes can be discharged in the same way as when they are dyed on wool; and reserved effects are produced by printing mechanical resists, such as waxes and fats, on the cloth and then dyeing it up in cold dye-liquor. The great affinity of the silk fiber for basic and acid dyestuffs enables it to extract colouring matter from cold solutions, and permanently combine with it to form an insoluble lake. After dyeing, the reserve prints are washed, first in cold water to get rid of any colour not fixed on the fibre, and then in hot water or benzene, to dissolve out the resisting bodies.
As a rule, after steaming, silk goods are only washed in hot water, but, of course, those printed entirely in mordant dyes will stand soaping, and indeed require it to brighten the colours and soften the material. (E. K.)