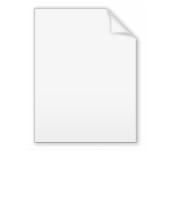
Hydraulic brake
Encyclopedia
The hydraulic brake is an arrangement of braking
mechanism which uses brake fluid
, typically containing ethylene glycol
, to transfer pressure from the controlling unit, which is usually near the operator of the vehicle, to the actual brake mechanism, which is usually at or near the wheel of the vehicle.
The system is usually filled with a glycol-ether
based brake fluid (other fluids may also be used).
At one time, passenger vehicles commonly employed drum brakes on all four wheels. Later, disc brakes were used for the front and drum brakes for the rear. However, because disc brakes have shown a better stopping performance and are therefore generally safer and more effective than drum brakes, four-wheel disc brakes have become increasingly popular, replacing drums on all but the most basic vehicles. Many two-wheel vehicles designs, however, continue to employ a drum brake for the rear wheel.
For simplicity, the braking system described hereafter uses the terminology and configuration for a simple disc brake.
The brake caliper piston(s) then apply force to the brake pads. This causes them to be pushed against the spinning rotor, and the friction between the pads and the rotor causes a braking torque
to be generated, slowing the vehicle. Heat generated from this friction is often dissipated through vents and channels in the rotor and through the pads themselves which are made of specialized heat-tolerant materials (kevlar
, sintered glass, et al.).
Subsequent release of the brake pedal/ lever allows the spring(s) within the master cylinder assembly to return that assembly's piston(s) back into position. This relieves the hydraulic pressure on the caliper allowing the brake piston in the caliper assembly to slide back into its housing and the brake pads to release the rotor. Unless there is a leak somewhere in the system, at no point does any of the brake fluid enter or leave the system.
, we can transfer a huge amount of energy, to stop a spinning object. Let us imagine a very simple brake system, with just two cylinders and a disc brake
. The cylinders are connected via tubes and inside the cylinders is a piston. The cylinders and tubes are filled with oil, which is incompressible. Notice that the two cylinders have the same volume, but has a different diameter, therefore a different surface area. The one with the smallest diameter is called the master cylinder
. The spinning disc brake, will be placed down at the piston with the larger surface area. Let us say that the diameter of the master cylinder is x and the diameter of the other cylinder is 4x, so the master cylinder has a surface area which is 16 times smaller. Now, if we push the piston in the master cylinder down 16 cm, with x kg of force, the other piston will then move 1 cm, with a force of 16*x kg. So if we push the piston in the master cylinder down with 10 kg of force, the other piston with the larger surface area, will then push against the spinning disc brake with 160 kg of force.
We can multiply this force by adding a lever
, which is connected to the piston in the master cylinder
. At the end of the lever we'll place a pedal, in the other end is the pivot
and somewhere between the two, we'll connect the lever to the piston. Let us say the distance from the pedal to the pivot is 3y and the distance from the pivot to the connected piston is y. Because the distance from the pedal to the pivot is 3 times larger than from the pivot to the piston, we are multiplying our force with a factor of 3, when pushing down on the pedal. Now, if we push down on the pedal with 10 kg of force, 30 kg of force will then be applied to the piston in the master cylinder and the other piston will then push against the spinning disc brake, with a total force of 480 kg. With this system we are all in all multiplying our force with a factor of 48.
The brake pedal is a simple lever. One end is attached to the framework of the vehicle, a pushrod extends from a point along its length, and the foot pad is at the other end of the lever. The rod either extends to the master cylinder (manual brakes) or to the vacuum booster (power brakes).
In a four-wheel car, the master cylinder is divided internally into two sections, each of which pressurizes a separate hydraulic circuit. Each section supplies pressure to one circuit. Passenger vehicles typically have either a front/rear split brake system or a diagonal split brake system (the master cylinder in a motorcycle or scooter may only pressurize a single unit, which will be the front brake).
A front/rear split system uses one master cylinder section to pressurize the front caliper pistons and the other section to pressurize the rear caliper pistons. A split circuit braking system is now required by law in most countries for safety reasons; if one circuit fails, the other circuit can stop the vehicle.
Diagonal split systems were used initially on American Motors
automobiles in the 1967 production year. The right front and left rear are served by one actuating piston while the left front and the right rear are served, exclusively, by a second actuating piston (both pistons pressurize their respective coupled lines from a single foot pedal). If either circuit fails, the other, with at least one front wheel braking (the front brakes provide most of the speed reduction) remains intact to stop the mechanically-damaged vehicle. Just before 1970, diagonally split systems had become universal for automobiles sold in the United States.
The diameter and length of the master cylinder has a significant effect on the performance of the brake system. A larger diameter master cylinder delivers more hydraulic fluid to the caliper pistons, yet requires more brake pedal force and less brake pedal stroke to achieve a given deceleration. A smaller diameter master cylinder has the opposite effect.
A master cylinder may also use differing diameters between the two sections to allow for increased fluid volume to one set of caliper pistons or the other.
is used in most modern hydraulic brake systems which contain four wheels. The vacuum booster is attached between the master cylinder and the brake pedal and multiplies the braking force applied by the driver. These units consist of a hollow housing with a movable rubber diaphragm across the center, creating two chambers. When attached to the low-pressure portion of the throttle body or intake manifold of the engine, the pressure in both chambers of the unit is lowered. The equilibrium created by the low pressure in both chambers keeps the diaphragm from moving until the brake pedal is depressed. A return spring keeps the diaphragm in the starting position until the brake pedal is applied. When the brake pedal is applied, the movement opens an air valve which lets in atmospheric pressure air to one chamber of the booster. Since the pressure becomes higher in one chamber, the diaphragm moves toward the lower pressure chamber with a force created by the area of the diaphragm and the differential pressure. This force, in addition to the driver's foot force, pushes on the master cylinder piston. A relatively small diameter booster unit is required; for a very conservative 50% manifold vacuum, an assisting force of about 1500 N (200n) is produced by a 20 cm diaphragm with an area of 0.03 square meters. The diaphragm will stop moving when the forces on both sides of the chamber reach equilibrium. This can be caused by either the air valve closing (due to the pedal apply stopping) or if "run out" is reached. Run out occurs when the pressure in one chamber reaches atmospheric pressure and no additional force can be generated by the now stagnant differential pressure. After the run out point is reached, only the driver's foot force can be used to further apply the master cylinder piston.
The fluid pressure from the master cylinder travels through a pair of steel brake tubes to a pressure differential valve, sometimes referred to as a "brake failure valve", which performs two functions: it equalizes pressure between the two systems, and it provides a warning if one system loses pressure. The pressure differential valve has two chambers (to which the hydraulic lines attach) with a piston between them. When the pressure in either line is balanced, the piston does not move. If the pressure on one side is lost, the pressure from the other side moves the piston. When the piston makes contact with a simple electrical probe in the center of the unit, a circuit is completed, and the operator is warned of a failure in the brake system.
From the pressure differential valve, brake tubing carries the pressure to the brake units at the wheels. Since the wheels do not maintain a fixed relation to the automobile, it is necessary to use hydraulic brake hose from the end of the steel line at the vehicle frame to the caliper at the wheel. Allowing steel brake tubing to flex invites metal fatigue
and, ultimately, brake failure. A common upgrade is to replace the standard rubber hoses with a set which are externally reinforced with braided stainless-steel wires; these have negligible expansion under pressure and can give a firmer feel to the brake pedal with less pedal travel for a given braking effort.
s and reservoir tanks. Hydraulic systems are smaller and less expensive.
Hydraulic fluid
must be non-compressible. Unlike air brakes
, where a valve is opened and air flows into the lines and brake chambers until the pressure rises sufficiently, hydraulic systems rely on a single stroke of a piston to force fluid through the system.
If any vapor is introduced into the system it will compress, and the pressure may not rise sufficiently to actuate the brakes.
Hydraulic braking systems are sometimes subjected to high temperatures during operation, such as when descending steep grades. For this reason, hydraulic fluid must resist vaporization at high temperatures.
Water vaporizes easily with heat and can corrode the metal parts of the system. If it gets into the brake lines, it can degrade brake performance dramatically. This is why light oils are often used as hydraulic fluids. Oil displaces water, protects plastic parts against corrosion, and can tolerate much higher temperatures before vaporizing.
"Brake fade
" is a condition caused by overheating in which braking effectiveness reduces, and may be lost. It may occur for many reasons. The pads which engage the rotating part may become overheated and "glaze over", becoming so smooth and hard that they cannot grip sufficiently to slow the vehicle. Also, vaporization of the hydraulic fluid under temperature extremes or thermal distortion may cause the linings to change their shape and engage less surface area of the rotating part. Thermal distortion may also cause permanent changes in the shape of the metal components, resulting in a reduction in braking capability that requires replacement of the affected parts.
Brake
A brake is a mechanical device which inhibits motion. Its opposite component is a clutch. The rest of this article is dedicated to various types of vehicular brakes....
mechanism which uses brake fluid
Brake fluid
Brake fluid is a type of hydraulic fluid used in hydraulic brake and hydraulic clutch applications in automobiles, motorcycles, light trucks, and some bicycles. It is used to transfer force into pressure...
, typically containing ethylene glycol
Ethylene glycol
Ethylene glycol is an organic compound widely used as an automotive antifreeze and a precursor to polymers. In its pure form, it is an odorless, colorless, syrupy, sweet-tasting liquid...
, to transfer pressure from the controlling unit, which is usually near the operator of the vehicle, to the actual brake mechanism, which is usually at or near the wheel of the vehicle.
History
In 1918 Malcolm Lougheed (who later changed the spelling of his name to Lockheed) developed a hydraulic brake system.Construction
The most common arrangement of hydraulic brakes for passenger vehicles, motorcycles, scooters, and mopeds, consists of the following:- Brake pedal or lever
- A pushrod (also called an actuating rod)
- A master cylinder assemblyMaster cylinderThe master cylinder is a control device that converts non-hydraulic pressure into hydraulic pressure, in order to move other device which are located at the other end of the hydraulic system, such as one or more slave cylinders...
containing a pistonPistonA piston is a component of reciprocating engines, reciprocating pumps, gas compressors and pneumatic cylinders, among other similar mechanisms. It is the moving component that is contained by a cylinder and is made gas-tight by piston rings. In an engine, its purpose is to transfer force from...
assembly (made up of either one or two pistons, a return spring, a series of gaskets/ O-rings and a fluid reservoir) - Reinforced hydraulic lines
- Brake caliper assemblyCaliperA caliper is a device used to measure the distance between two opposing sides of an object. A caliper can be as simple as a compass with inward or outward-facing points...
usually consisting of one or two hollow aluminum or chrome-plated steel pistons (called caliper pistons), a set of thermally conductive brake pads and a rotor (also called a brake disc) or drumDrum brakeA drum brake is a brake in which the friction is caused by a set of shoes or pads that press against a rotating drum-shaped part called a brake drum....
attached to an axle.
The system is usually filled with a glycol-ether
Glycol Ethers
Glycol ethers are a group of solvents based on alkyl ethers of ethylene glycol commonly used in paints. These solvents typically have higher boiling point, together with the favorable solvent properties of lower molecular weight of ethers and alcohols. The word "Cellosolve" was registered in 1924...
based brake fluid (other fluids may also be used).
At one time, passenger vehicles commonly employed drum brakes on all four wheels. Later, disc brakes were used for the front and drum brakes for the rear. However, because disc brakes have shown a better stopping performance and are therefore generally safer and more effective than drum brakes, four-wheel disc brakes have become increasingly popular, replacing drums on all but the most basic vehicles. Many two-wheel vehicles designs, however, continue to employ a drum brake for the rear wheel.
For simplicity, the braking system described hereafter uses the terminology and configuration for a simple disc brake.
System Operation
Within a hydraulic brake system, as the brake pedal is pressed, a pushrod exerts force on the piston(s) in the master cylinder causing fluid from the brake fluid reservoir to flow into a pressure chamber through a compensating port which results in an increase in the pressure of the entire hydraulic system. This forces fluid through the hydraulic lines toward one or more calipers where it acts upon one or two caliper pistons sealed by one or more seated O-rings which prevent the escape of any fluid from around the piston.The brake caliper piston(s) then apply force to the brake pads. This causes them to be pushed against the spinning rotor, and the friction between the pads and the rotor causes a braking torque
Torque
Torque, moment or moment of force , is the tendency of a force to rotate an object about an axis, fulcrum, or pivot. Just as a force is a push or a pull, a torque can be thought of as a twist....
to be generated, slowing the vehicle. Heat generated from this friction is often dissipated through vents and channels in the rotor and through the pads themselves which are made of specialized heat-tolerant materials (kevlar
Kevlar
Kevlar is the registered trademark for a para-aramid synthetic fiber, related to other aramids such as Nomex and Technora. Developed at DuPont in 1965, this high strength material was first commercially used in the early 1970s as a replacement for steel in racing tires...
, sintered glass, et al.).
Subsequent release of the brake pedal/ lever allows the spring(s) within the master cylinder assembly to return that assembly's piston(s) back into position. This relieves the hydraulic pressure on the caliper allowing the brake piston in the caliper assembly to slide back into its housing and the brake pads to release the rotor. Unless there is a leak somewhere in the system, at no point does any of the brake fluid enter or leave the system.
An example of a hydraulic brake system
When using hydraulicsHydraulics
Hydraulics is a topic in applied science and engineering dealing with the mechanical properties of liquids. Fluid mechanics provides the theoretical foundation for hydraulics, which focuses on the engineering uses of fluid properties. In fluid power, hydraulics is used for the generation, control,...
, we can transfer a huge amount of energy, to stop a spinning object. Let us imagine a very simple brake system, with just two cylinders and a disc brake
Disc brake
The disc brake or disk brake is a device for slowing or stopping the rotation of a wheel while it is in motion.A brake disc is usually made of cast iron, but may in some cases be made of composites such as reinforced carbon–carbon or ceramic matrix composites. This is connected to the wheel and/or...
. The cylinders are connected via tubes and inside the cylinders is a piston. The cylinders and tubes are filled with oil, which is incompressible. Notice that the two cylinders have the same volume, but has a different diameter, therefore a different surface area. The one with the smallest diameter is called the master cylinder
Master cylinder
The master cylinder is a control device that converts non-hydraulic pressure into hydraulic pressure, in order to move other device which are located at the other end of the hydraulic system, such as one or more slave cylinders...
. The spinning disc brake, will be placed down at the piston with the larger surface area. Let us say that the diameter of the master cylinder is x and the diameter of the other cylinder is 4x, so the master cylinder has a surface area which is 16 times smaller. Now, if we push the piston in the master cylinder down 16 cm, with x kg of force, the other piston will then move 1 cm, with a force of 16*x kg. So if we push the piston in the master cylinder down with 10 kg of force, the other piston with the larger surface area, will then push against the spinning disc brake with 160 kg of force.
We can multiply this force by adding a lever
Lever
In physics, a lever is a rigid object that is used with an appropriate fulcrum or pivot point to either multiply the mechanical force that can be applied to another object or resistance force , or multiply the distance and speed at which the opposite end of the rigid object travels.This leverage...
, which is connected to the piston in the master cylinder
Master cylinder
The master cylinder is a control device that converts non-hydraulic pressure into hydraulic pressure, in order to move other device which are located at the other end of the hydraulic system, such as one or more slave cylinders...
. At the end of the lever we'll place a pedal, in the other end is the pivot
Lever
In physics, a lever is a rigid object that is used with an appropriate fulcrum or pivot point to either multiply the mechanical force that can be applied to another object or resistance force , or multiply the distance and speed at which the opposite end of the rigid object travels.This leverage...
and somewhere between the two, we'll connect the lever to the piston. Let us say the distance from the pedal to the pivot is 3y and the distance from the pivot to the connected piston is y. Because the distance from the pedal to the pivot is 3 times larger than from the pivot to the piston, we are multiplying our force with a factor of 3, when pushing down on the pedal. Now, if we push down on the pedal with 10 kg of force, 30 kg of force will then be applied to the piston in the master cylinder and the other piston will then push against the spinning disc brake, with a total force of 480 kg. With this system we are all in all multiplying our force with a factor of 48.
Component specifics
(For typical light duty automotive braking systems)The brake pedal is a simple lever. One end is attached to the framework of the vehicle, a pushrod extends from a point along its length, and the foot pad is at the other end of the lever. The rod either extends to the master cylinder (manual brakes) or to the vacuum booster (power brakes).
In a four-wheel car, the master cylinder is divided internally into two sections, each of which pressurizes a separate hydraulic circuit. Each section supplies pressure to one circuit. Passenger vehicles typically have either a front/rear split brake system or a diagonal split brake system (the master cylinder in a motorcycle or scooter may only pressurize a single unit, which will be the front brake).
A front/rear split system uses one master cylinder section to pressurize the front caliper pistons and the other section to pressurize the rear caliper pistons. A split circuit braking system is now required by law in most countries for safety reasons; if one circuit fails, the other circuit can stop the vehicle.
Diagonal split systems were used initially on American Motors
American Motors
American Motors Corporation was an American automobile company formed by the 1954 merger of Nash-Kelvinator Corporation and Hudson Motor Car Company. At the time, it was the largest corporate merger in U.S. history.George W...
automobiles in the 1967 production year. The right front and left rear are served by one actuating piston while the left front and the right rear are served, exclusively, by a second actuating piston (both pistons pressurize their respective coupled lines from a single foot pedal). If either circuit fails, the other, with at least one front wheel braking (the front brakes provide most of the speed reduction) remains intact to stop the mechanically-damaged vehicle. Just before 1970, diagonally split systems had become universal for automobiles sold in the United States.
The diameter and length of the master cylinder has a significant effect on the performance of the brake system. A larger diameter master cylinder delivers more hydraulic fluid to the caliper pistons, yet requires more brake pedal force and less brake pedal stroke to achieve a given deceleration. A smaller diameter master cylinder has the opposite effect.
A master cylinder may also use differing diameters between the two sections to allow for increased fluid volume to one set of caliper pistons or the other.
Power brakes
The vacuum booster or vacuum servoVacuum servo
A vacuum servo is a component used on motor vehicles in their braking system, to provide assistance to the driver by decreasing the braking effort. In the USA it is commonly called a brake booster.-Background:...
is used in most modern hydraulic brake systems which contain four wheels. The vacuum booster is attached between the master cylinder and the brake pedal and multiplies the braking force applied by the driver. These units consist of a hollow housing with a movable rubber diaphragm across the center, creating two chambers. When attached to the low-pressure portion of the throttle body or intake manifold of the engine, the pressure in both chambers of the unit is lowered. The equilibrium created by the low pressure in both chambers keeps the diaphragm from moving until the brake pedal is depressed. A return spring keeps the diaphragm in the starting position until the brake pedal is applied. When the brake pedal is applied, the movement opens an air valve which lets in atmospheric pressure air to one chamber of the booster. Since the pressure becomes higher in one chamber, the diaphragm moves toward the lower pressure chamber with a force created by the area of the diaphragm and the differential pressure. This force, in addition to the driver's foot force, pushes on the master cylinder piston. A relatively small diameter booster unit is required; for a very conservative 50% manifold vacuum, an assisting force of about 1500 N (200n) is produced by a 20 cm diaphragm with an area of 0.03 square meters. The diaphragm will stop moving when the forces on both sides of the chamber reach equilibrium. This can be caused by either the air valve closing (due to the pedal apply stopping) or if "run out" is reached. Run out occurs when the pressure in one chamber reaches atmospheric pressure and no additional force can be generated by the now stagnant differential pressure. After the run out point is reached, only the driver's foot force can be used to further apply the master cylinder piston.
The fluid pressure from the master cylinder travels through a pair of steel brake tubes to a pressure differential valve, sometimes referred to as a "brake failure valve", which performs two functions: it equalizes pressure between the two systems, and it provides a warning if one system loses pressure. The pressure differential valve has two chambers (to which the hydraulic lines attach) with a piston between them. When the pressure in either line is balanced, the piston does not move. If the pressure on one side is lost, the pressure from the other side moves the piston. When the piston makes contact with a simple electrical probe in the center of the unit, a circuit is completed, and the operator is warned of a failure in the brake system.
From the pressure differential valve, brake tubing carries the pressure to the brake units at the wheels. Since the wheels do not maintain a fixed relation to the automobile, it is necessary to use hydraulic brake hose from the end of the steel line at the vehicle frame to the caliper at the wheel. Allowing steel brake tubing to flex invites metal fatigue
Metal Fatigue
Metal Fatigue , is a futuristic science fiction, real-time strategy computer game developed by Zono Incorporated and published by Psygnosis and TalonSoft .-Plot:...
and, ultimately, brake failure. A common upgrade is to replace the standard rubber hoses with a set which are externally reinforced with braided stainless-steel wires; these have negligible expansion under pressure and can give a firmer feel to the brake pedal with less pedal travel for a given braking effort.
Special considerations
Air brake systems are bulky, and require air compressorAir compressor
An air compressor is a device that converts power into kinetic energy by compressing and pressurizing air, which, on command, can be released in quick bursts...
s and reservoir tanks. Hydraulic systems are smaller and less expensive.
Hydraulic fluid
Hydraulic fluid
Hydraulic fluids, also called hydraulic liquids, are the medium by which power is transferred in hydraulic machinery. Common hydraulic fluids are based on mineral oil or water...
must be non-compressible. Unlike air brakes
Air brake (road vehicle)
Air brakes are used in trucks, buses, trailers, and semi-trailers. George Westinghouse first developed air brakes for use in railway service. He patented a safer air brake on March 5, 1872. Originally designed and built for use on railroad train application, air brakes remain the exclusive systems...
, where a valve is opened and air flows into the lines and brake chambers until the pressure rises sufficiently, hydraulic systems rely on a single stroke of a piston to force fluid through the system.
If any vapor is introduced into the system it will compress, and the pressure may not rise sufficiently to actuate the brakes.
Hydraulic braking systems are sometimes subjected to high temperatures during operation, such as when descending steep grades. For this reason, hydraulic fluid must resist vaporization at high temperatures.
Water vaporizes easily with heat and can corrode the metal parts of the system. If it gets into the brake lines, it can degrade brake performance dramatically. This is why light oils are often used as hydraulic fluids. Oil displaces water, protects plastic parts against corrosion, and can tolerate much higher temperatures before vaporizing.
"Brake fade
Brake fade
Vehicle braking system fade, or brake fade, is the reduction in stopping power that can occur after repeated or sustained application of the brakes, especially in high load or high speed conditions...
" is a condition caused by overheating in which braking effectiveness reduces, and may be lost. It may occur for many reasons. The pads which engage the rotating part may become overheated and "glaze over", becoming so smooth and hard that they cannot grip sufficiently to slow the vehicle. Also, vaporization of the hydraulic fluid under temperature extremes or thermal distortion may cause the linings to change their shape and engage less surface area of the rotating part. Thermal distortion may also cause permanent changes in the shape of the metal components, resulting in a reduction in braking capability that requires replacement of the affected parts.
See also
- HydraulicsHydraulicsHydraulics is a topic in applied science and engineering dealing with the mechanical properties of liquids. Fluid mechanics provides the theoretical foundation for hydraulics, which focuses on the engineering uses of fluid properties. In fluid power, hydraulics is used for the generation, control,...
- Hydraulic circuitHydraulic circuitA hydraulic circuit is a system comprising an interconnected set of discrete components that transport liquid. The purpose of this system may be to control where fluid flows or to control fluid pressure...
- Fuse (hydraulic)Fuse (hydraulic)In hydraulic systems, a fuse is a component which prevents the sudden loss of hydraulic fluid pressure. It is a safety feature, designed to allow systems to continue operating, or at least to not fail catastrophically, in the event of a system breach...
- Bicycle brake systemsBicycle brake systemsA bicycle brake is used to slow down or stop a bicycle. There have been various types of brake used throughout history, and several are still in use today...
- Vehicle brakeVehicle brakeA vehicle brake is a brake used to slow down a vehicle by converting its kinetic energy into heat. The basic hydraulic system, most commonly used, usually has six main stages...
- Brake bleedingBrake bleedingBrake bleeding is the procedure performed on hydraulic brake systems whereby the brake lines are purged of any air bubbles...
- Brake-by-wireBrake-by-wireDrive-by-wire technology in automotive industry replaces the traditional mechanical and hydraulic control systems with electronic control systems using electromechanical actuators and human-machine interfaces such as pedal and steering feel emulators...