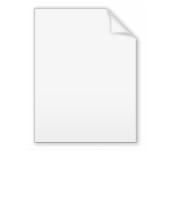
Nanoimprint Lithography
Encyclopedia
Nanoimprint lithography is a method of fabricating nanometer scale patterns. It is a simple nanolithography
process with low cost, high throughput and high resolution. It creates patterns by mechanical deformation of imprint resist and subsequent processes. The imprint resist is typically a monomer
or polymer
formulation that is cured by heat or UV light during the imprinting. Adhesion between the resist and the template is controlled to allow proper release.
(ITRS) for the 32
and 22
nm nodes.
Thermoplastic nanoimprint lithography (T-NIL) is the earliest nanoimprint lithography developed by Prof. Stephen Chou's group.
In a standard T-NIL process, a thin layer of imprint resist (thermoplastic polymer) is spin coated
onto the sample substrate. Then the mold, which has predefined topological patterns, is brought into contact with the sample and they are pressed together under certain pressure. When heated up above the glass transition temperature of the polymer, the pattern on the mold is pressed into the softened polymer film . After being cooled down, the mold is separated from the sample and the pattern resist is left on the substrate. A pattern transfer process (reactive ion etching
, normally) can be used to transfer the pattern in the resist to the underneath substrate.
Alternatively, cold welding
between two metal surfaces could also transfer low dimensional nanostructured metal without heating (especially for critical sizes less than ~10nm) ,. Three-dimensional structures can be fabricated by repeating this procedure. The cold welding approach has the advantage of reducing surface contact contamination or defect due to no heating process, which is a main problem in the latest development and fabrication of organic electronic devices as well as novel solar cells.
liquid resist is applied to the sample substrate and the mold is normally made of transparent material like fused silica. After the mold and the substrate are pressed together, the resist is cured in UV light and becomes solid. After mold separation, a similar pattern transfer process can be used to transfer the pattern in resist onto the underneath material. The use of a UV-transparent mold is difficult in a vacuum, because a vacuum chuck to hold the mold would not be possible.
To ensure the pressure and pattern uniformities of full wafer nanoimprint processes and prolong the mold lifetime, a pressing method utilizing isotropic fluid pressure, named Air Cushion Press (ACP) by its inventors, is developed and being used by commercial nanoimprint systems.
For electronics devices, NIL has been used to fabricate MOSFET
, O-TFT, single electron memory.
For optics and photonics, intensive study has been conducted in fabrication of subwavelength resonant grating filter, polarizer
s, waveplate, anti-reflective structures, integrated photonics
circuit and plasmontic devices by NIL.
sub-10 nm nanofluidic channels had been fabricated using NIL and used in DNA strenching experiment. Currently, NIL is used to shrink the size of biomolecular sorting device an order of magnitude smaller and more efficient.
s and immense stacks of precision ground lens elements to achieve nanometer scale resolution. There is no need for complex optics or high-energy radiation sources with a nanoimprint tool. There is no need for finely tailored photoresist
s designed for both resolution and sensitivity at a given wavelength. The simplified requirements of the technology lead to its low cost.
Imprint lithography is inherently a three-dimensional patterning process. Imprint molds can be fabricated with multiple layers of topography stacked vertically. Resulting imprints replicate both layers with a single imprint step, which allows chip manufactures to reduce chip fabrication costs and improve product throughput.
As mentioned above, the imprint material does not need to be finely tuned for high resolution and sensitivity. A broader range of materials with varying properties are available for use with imprint lithography. The increased material variability gives chemists the freedom to design new functional materials rather than sacrificial etch resistant polymers. A functional material may be imprinted directly to form a layer in a chip with no need for pattern transfer into underlying materials. The successful implementation of a functional imprint material would result in significant cost reductions and increased throughput by eliminating many difficult chip fabrication processing steps.
capability is 10 nm. Overlay has a better chance with step-and-scan approaches as opposed to full-wafer imprint.
, defect control is expected to improve as the technology matures. Defects from the template with size below the post-imprint process bias can be eliminated. Other defects would require effective template cleaning and/or the use of intermediate polymer stamps. When vacuum is not used during the imprint process, air can get trapped, resulting in bubble defects. This is because the imprint resist layer and the template or stamp features are not perfectly flat. There is an elevated risk when the intermediate or master stamp contains depressions (which are especially easy air traps), or when the imprint resist is dispensed as droplets just before imprinting, rather than pre-spun onto the substrate. Sufficient time must be allowed for the air to escape.
or focused ion beam
patterning; however at the smallest resolution, the throughput is very slow. As a result, optical patterning tools will be more helpful if they have sufficient resolution. Such an approach has been successfully demonstrated by Greener et al. whereby robust templates were rapidly fabricated by optical patterning of a photoresist-coated metal substrate through a photomask
. Other patterning techniques (including even double patterning
) may also be used. Kumar and Schroers at Yale developed the nanopatterning of amorphous metals which can be used as inexpensive templates for nanoimprinting.
materials. These materials are not stiff and, as part of the substrate, are readily damaged mechanically by the pressure of the imprint process.
. When the stamp is contacted with metal, electrochemical etching can be carried out with an applied voltage. The electrochemical reaction generates metal ions which move from the original film into the stamp. Eventually all the metal is removed and the complementary stamp pattern is transferred to the remaining metal.
will provide the ultimate solution for templates of periodic patterns at scales of 10 nm and less. It is also possible to resolve the template generation issue by using a programmable template in a scheme based on double patterning
.
As of October 2007, Toshiba
is the only company to have validated nanoimprint lithography for 22 nm and beyond. What is more significant is that nanoimprint lithography is the first sub-30 nm lithography to be validated by an industrial user.
Nanolithography
Nanolithography is the branch of nanotechnology concerned with the study and application of fabricating nanometer-scale structures, meaning patterns with at least one lateral dimension between the size of an individual atom and approximately 100 nm...
process with low cost, high throughput and high resolution. It creates patterns by mechanical deformation of imprint resist and subsequent processes. The imprint resist is typically a monomer
Monomer
A monomer is an atom or a small molecule that may bind chemically to other monomers to form a polymer; the term "monomeric protein" may also be used to describe one of the proteins making up a multiprotein complex...
or polymer
Polymer
A polymer is a large molecule composed of repeating structural units. These subunits are typically connected by covalent chemical bonds...
formulation that is cured by heat or UV light during the imprinting. Adhesion between the resist and the template is controlled to allow proper release.
History
The term "Nanoimprint Lithography" (NIL) was coined in the scientific literature in 1996, when Prof. Stephen Chou and his students published a report in Science, although hot embossing (now taken as a synonym of NIL) of thermoplastics had been appearing in the patent literature for a few years already. Soon after the Science paper, many researchers developed many different variations and implementations. At this point, nanoimprint lithography has been added to the International Technology Roadmap for SemiconductorsInternational Technology Roadmap for Semiconductors
The International Technology Roadmap for Semiconductors is a set of documents produced by a group of semiconductor industry experts. These experts are representative of the sponsoring organisations which include the Semiconductor Industry Associations of the US, Europe, Japan, South Korea and...
(ITRS) for the 32
32 nanometer
The 32 nm process is the step following the 45 nanometer process in CMOS semiconductor device fabrication. 32 nanometer refers to the average half-pitch of a memory cell at this technology level...
and 22
22 nanometer
The 22 nanometer node is the CMOS process step following 32 nm. It was introduced by semiconductor companies in 2011. The typical half-pitch for a memory cell is around 22 nm...
nm nodes.
Processes
There are many different types of nanoimprint lithography, but two of them are most important: thermoplastic nanoimprint lithography and photo nanoimprint lithography.Thermoplastic nanoimprint lithography
Thermoplastic nanoimprint lithography (T-NIL) is the earliest nanoimprint lithography developed by Prof. Stephen Chou's group.
In a standard T-NIL process, a thin layer of imprint resist (thermoplastic polymer) is spin coated
Spin coating
Spin coating is a procedure used to apply uniform thin films to flat substrates. In short, an excess amount of a solution is placed on the substrate, which is then rotated at high speed in order to spread the fluid by centrifugal force...
onto the sample substrate. Then the mold, which has predefined topological patterns, is brought into contact with the sample and they are pressed together under certain pressure. When heated up above the glass transition temperature of the polymer, the pattern on the mold is pressed into the softened polymer film . After being cooled down, the mold is separated from the sample and the pattern resist is left on the substrate. A pattern transfer process (reactive ion etching
Reactive ion etching
Reactive-ion etching is an etching technology used in microfabrication. It uses chemically reactive plasma to remove material deposited on wafers. The plasma is generated under low pressure by an electromagnetic field...
, normally) can be used to transfer the pattern in the resist to the underneath substrate.
Alternatively, cold welding
Cold welding
Cold or contact welding is a solid-state welding process in which joining takes place without fusion/heating at the interface of the two parts to be welded. Unlike in the fusion-welding processes, no liquid or molten phase is present in the joint....
between two metal surfaces could also transfer low dimensional nanostructured metal without heating (especially for critical sizes less than ~10nm) ,. Three-dimensional structures can be fabricated by repeating this procedure. The cold welding approach has the advantage of reducing surface contact contamination or defect due to no heating process, which is a main problem in the latest development and fabrication of organic electronic devices as well as novel solar cells.
Photo nanoimprint lithography
In photo nanoimprint lithography (P-NIL), a photo(UV) curableCuring (chemistry)
Curing is a term in polymer chemistry and process engineering that refers to the toughening or hardening of a polymer material by cross-linking of polymer chains, brought about by chemical additives, ultraviolet radiation, electron beam or heat...
liquid resist is applied to the sample substrate and the mold is normally made of transparent material like fused silica. After the mold and the substrate are pressed together, the resist is cured in UV light and becomes solid. After mold separation, a similar pattern transfer process can be used to transfer the pattern in resist onto the underneath material. The use of a UV-transparent mold is difficult in a vacuum, because a vacuum chuck to hold the mold would not be possible.
Full wafer nanoimprint
In a full wafer nanoimprint scheme, all the patterns are contained in a single nanoimprint field and will be transferred in a single imprint step. This allows a high throughput and uniformity. An at least 8 inches (203 mm) diameter full-wafer nanoimprint with high fidelity is possible.To ensure the pressure and pattern uniformities of full wafer nanoimprint processes and prolong the mold lifetime, a pressing method utilizing isotropic fluid pressure, named Air Cushion Press (ACP) by its inventors, is developed and being used by commercial nanoimprint systems.
Step and repeat nanoimprint
Nanoimprint can be performed in a way similar to the step and repeat optical lithography. The imprint field (die) is typically much smaller than the full wafer nanoimprint field. The die is repeatedly imprinted to the substrate with certain step size. This scheme is good for nanoimprint mold creation.Applications
Nanoimprint lithography has been used to fabricate devices for electrical, optical, photonic and biological applications.For electronics devices, NIL has been used to fabricate MOSFET
MOSFET
The metal–oxide–semiconductor field-effect transistor is a transistor used for amplifying or switching electronic signals. The basic principle of this kind of transistor was first patented by Julius Edgar Lilienfeld in 1925...
, O-TFT, single electron memory.
For optics and photonics, intensive study has been conducted in fabrication of subwavelength resonant grating filter, polarizer
Polarizer
A polarizer is an optical filter that passes light of a specific polarization and blocks waves of other polarizations. It can convert a beam of light of undefined or mixed polarization into a beam with well-defined polarization. The common types of polarizers are linear polarizers and circular...
s, waveplate, anti-reflective structures, integrated photonics
Photonics
The science of photonics includes the generation, emission, transmission, modulation, signal processing, switching, amplification, detection and sensing of light. The term photonics thereby emphasizes that photons are neither particles nor waves — they are different in that they have both particle...
circuit and plasmontic devices by NIL.
sub-10 nm nanofluidic channels had been fabricated using NIL and used in DNA strenching experiment. Currently, NIL is used to shrink the size of biomolecular sorting device an order of magnitude smaller and more efficient.
Benefits
A key benefit of nanoimprint lithography is its sheer simplicity. The single greatest cost associated with chip fabrication is the optical lithography tool used to print the circuit patterns. Optical lithography requires high powered excimer laserExcimer laser
An excimer laser is a form of ultraviolet laser which is commonly used in the production of microelectronic devices , eye surgery, and micromachining....
s and immense stacks of precision ground lens elements to achieve nanometer scale resolution. There is no need for complex optics or high-energy radiation sources with a nanoimprint tool. There is no need for finely tailored photoresist
Photoresist
A photoresist is a light-sensitive material used in several industrial processes, such as photolithography and photoengraving to form a patterned coating on a surface.-Tone:Photoresists are classified into two groups: positive resists and negative resists....
s designed for both resolution and sensitivity at a given wavelength. The simplified requirements of the technology lead to its low cost.
Imprint lithography is inherently a three-dimensional patterning process. Imprint molds can be fabricated with multiple layers of topography stacked vertically. Resulting imprints replicate both layers with a single imprint step, which allows chip manufactures to reduce chip fabrication costs and improve product throughput.
As mentioned above, the imprint material does not need to be finely tuned for high resolution and sensitivity. A broader range of materials with varying properties are available for use with imprint lithography. The increased material variability gives chemists the freedom to design new functional materials rather than sacrificial etch resistant polymers. A functional material may be imprinted directly to form a layer in a chip with no need for pattern transfer into underlying materials. The successful implementation of a functional imprint material would result in significant cost reductions and increased throughput by eliminating many difficult chip fabrication processing steps.
Concerns
The key concerns for nanoimprint lithography are overlay, defects, template patterning and template wear. However, recently Kumar et al. have shown that amorphous metals (metallic glasses) can be patterned on sub-100 nm scale, which can significantly reduce the template cost.Overlay
The current overlay 3 sigmaStandard deviation
Standard deviation is a widely used measure of variability or diversity used in statistics and probability theory. It shows how much variation or "dispersion" there is from the average...
capability is 10 nm. Overlay has a better chance with step-and-scan approaches as opposed to full-wafer imprint.
Defects
As with immersion lithographyImmersion lithography
Immersion lithography is a photolithography resolution enhancement technique for manufacturing integrated circuits that replaces the usual air gap between the final lens and the wafer surface with a liquid medium that has a refractive index greater than one. The resolution is increased by a factor...
, defect control is expected to improve as the technology matures. Defects from the template with size below the post-imprint process bias can be eliminated. Other defects would require effective template cleaning and/or the use of intermediate polymer stamps. When vacuum is not used during the imprint process, air can get trapped, resulting in bubble defects. This is because the imprint resist layer and the template or stamp features are not perfectly flat. There is an elevated risk when the intermediate or master stamp contains depressions (which are especially easy air traps), or when the imprint resist is dispensed as droplets just before imprinting, rather than pre-spun onto the substrate. Sufficient time must be allowed for the air to escape.
Template patterning
High resolution template patterning can currently be performed by electron beam lithographyElectron beam lithography
Electron beam lithography is the practice of emitting a beam of electrons in a patterned fashion across a surface covered with a film , and of selectively removing either exposed or non-exposed regions of the resist...
or focused ion beam
Focused ion beam
Focused ion beam, also known as FIB, is a technique used particularly in the semiconductor industry, materials science and increasingly in the biological field for site-specific analysis, deposition, and ablation of materials. An FIB setup is a scientific instrument that resembles a scanning...
patterning; however at the smallest resolution, the throughput is very slow. As a result, optical patterning tools will be more helpful if they have sufficient resolution. Such an approach has been successfully demonstrated by Greener et al. whereby robust templates were rapidly fabricated by optical patterning of a photoresist-coated metal substrate through a photomask
Photomask
A photomask is an opaque plate with holes or transparencies that allow light to shine through in a defined pattern. They are commonly used in photolithography.-Overview:...
. Other patterning techniques (including even double patterning
Double patterning
Multiple patterning is a class of technologies for manufacturing integrated circuits , developed for photolithography to enhance the feature density. The simplest case of multiple patterning is double patterning, where a conventional lithography process is enhanced to produce double the expected...
) may also be used. Kumar and Schroers at Yale developed the nanopatterning of amorphous metals which can be used as inexpensive templates for nanoimprinting.
Template wear
The use of substantial pressure to not only contact but also penetrate a layer during imprinting accelerates the wear of imprint templates compared to other types of lithographic masks.Other
Future applications of nanoimprint lithography may involve the use of porous low-kLow-K
In semiconductor manufacturing, a low-κ dielectric is a material with a small dielectric constant relative to silicon dioxide. Although the proper symbol for the dielectric constant is the Greek letter κ , in conversation such materials are referred to as being "low-k" rather than "low-κ"...
materials. These materials are not stiff and, as part of the substrate, are readily damaged mechanically by the pressure of the imprint process.
Removal of residual layers
A key characteristic of nanoimprint lithography (except for electrochemical nanoimprinting) is the residual layer following the imprint process. It is preferable to have thick enough residual layers to support alignment and throughput and low defects. However, this renders the nanoimprint lithography step less critical for critical dimension (CD) control than the etch step used to remove the residual layer. Hence, it is important to consider the residual layer removal an integrated part of the overall nanoimprint patterning process. In a sense, the residual layer etch is similar to the develop process in conventional lithography. It has been proposed to combine photolithography and nanoimprint lithography techniques in one step in order to eliminate the residual layer.Proximity effects
Nanoimprint lithography relies on displacing polymer. This could lead to systematic effects over long distances. For example, a large, dense array of protrusions will displace significantly more polymer than an isolated protrusion. Depending on the distance of this isolated protrusion from the array, the isolated feature may not imprint correctly due to polymer displacement and thickening. Resist holes can form in between groups of protrusions. Likewise, wider depressions in the template do not fill up with as much polymer as narrower depressions, resulting in misshapen wide lines. In addition, a depression at the edge of a large array fills up much earlier than one located in the center of the array, resulting in within-array uniformity issues.3D-patterning
A unique benefit of nanoimprint lithography is the ability to pattern 3D structures, such as damascene interconnects and T-gates, in fewer steps than required for conventional lithography. This is achieved by building the T-shape into the protrusion on the template.Electrochemical nanoimprinting
Electrochemical nanoimprinting can be achieved using a stamp made from a superionic conductor such as silver sulfideSilver sulfide
Silver sulfide, Ag2S, is the sulfide of silver. This dense black solid constitutes the tarnish that forms over time on silverware and other silver objects. Silver sulfide is insoluble in all solvents, but is degraded by strong acids. Silver sulfide features a covalent bond, as it is made up of...
. When the stamp is contacted with metal, electrochemical etching can be carried out with an applied voltage. The electrochemical reaction generates metal ions which move from the original film into the stamp. Eventually all the metal is removed and the complementary stamp pattern is transferred to the remaining metal.
Laser assisted direct imprint
Laser assisted direct imprint (LADI) is a rapid technique for patterning nanostructures in solid substrates and it does not require etching. A single or multiple excimer laser pulses melt a thin surface layer of substrate material, and a mold is embossed into the resulting liquid layer. A variety of structures with resolution better than 10 nm have been imprinted into silicon using LADI, and the embossing time is less than 250 ns. The high resolution and speed of LADI, attributed to molten silicon’s low viscosity (one-third that of water), could open up a variety of applications and be extended to other materials and processing techniques.The future of nanoimprint
Nanoimprint lithography is a simple pattern transfer process that is neither limited by diffraction nor scattering effects nor secondary electrons, and does not require any sophisticated radiation chemistry. It is also a potentially simple and inexpensive technique. However, a lingering barrier to nanometer-scale patterning is the current reliance on other lithography techniques to generate the template. It is possible that self-assembled structuresSelf-assembly
Self-assembly is a term used to describe processes in which a disordered system of pre-existing components forms an organized structure or pattern as a consequence of specific, local interactions among the components themselves, without external direction...
will provide the ultimate solution for templates of periodic patterns at scales of 10 nm and less. It is also possible to resolve the template generation issue by using a programmable template in a scheme based on double patterning
Double patterning
Multiple patterning is a class of technologies for manufacturing integrated circuits , developed for photolithography to enhance the feature density. The simplest case of multiple patterning is double patterning, where a conventional lithography process is enhanced to produce double the expected...
.
As of October 2007, Toshiba
Toshiba
is a multinational electronics and electrical equipment corporation headquartered in Tokyo, Japan. It is a diversified manufacturer and marketer of electrical products, spanning information & communications equipment and systems, Internet-based solutions and services, electronic components and...
is the only company to have validated nanoimprint lithography for 22 nm and beyond. What is more significant is that nanoimprint lithography is the first sub-30 nm lithography to be validated by an industrial user.