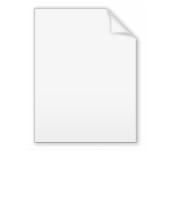
Process Redesign
Encyclopedia
The Process Redesign methodology was developed by H. James Harrington
in the early 1980s and is applied to the current process to remove all of its waste and to streamline its activities. It first streamlines the processes, and then uses IT techniques to perform the routine and repetitive activities. It is effective at reducing cost and cycle time between 20-60% and improving quality from 40-200%.
during the early 1980s. It was refined through the 1980s and it became a tool used by Ernst & Young
in the early 1990s. It was first published to the general public in Business Process Improvement – the Breakthrough Strategy for Total Quality, Productivity, and Competitiveness, published by McGraw-Hill
published in 1991 and authored by H. James Harrington.
Process Reengineering operates under the belief that the current process is so obsolete that it should be ignored and the redesign team should start over from scratch and design a totally new process. This typically takes between nine - twelve months to accomplish. Typically Process Reengineering is applied to a process when cost or cycle time needs to be improved between 60-90%. In other words, when a current process is being performed by a 100 people and to be competitive, it needs to be done by less than 40 people. Only about 10% of the process improvement activities need to be reengineered.
To define the critical business processes the executive team should look at each macro process and define three to ten major processes included in each macro process. Once a list of 30 or more major processes are identified, the Executive Improvement Team (EIT) needs to establish a prioritization matrix based upon the organization’s business plan, competitive positioning, its core capabilities and competencies, and the key process issues like changeability, opportunity for improvement, impact on the external customer, etc. The executive team should then develop a prioritization index for each of the major processes, using real data if possible, by first selecting the ten processes that have the highest priority and then selecting one to three of these processes that will be started first.
Training for the following ten fundamental Process Redesign tools can be provided on a just-in-time basis.
The importance of establishing a good process change plan and implementing it cannot be overemphasized. The objectives of the Change Management Plan should be to:
The purpose of Phase II is for the PIT to gain detailed knowledge of the process and its matrices (cost, cycle time, processing time, error rates, etc.). The flowchart and simulation model of the present process (the “as-is” model of the process) will be used to improve the process during Phase III.
The PIT team now will block diagram the total process, following the process flow. Using the block diagram, start with the inputs to the process and develop the flowchart so that all activities within the process under study have been charted. Normally, flowcharts go down to the activity level only but often some important activities are flowcharted down to the task level. Once you have completed the flowchart, look at each block on the flowchart and estimate the following:
At this point in time, the processing time, cycle time and cost are based upon the best judgment of the PIT. Later on in this phase, actual data will be collected.
The importance of developing a simulation model cannot be over-emphasized. It is a monumental job to try to accumulate and manipulate the data that is involved in analyzing a business process by hand. There are a number of good software packages. Among them are: WorkDraw from EDGE Software Inc., Pleasanton, California; and Envision written by Future Tech Systems Inc., Auburn, Washington.
We recommend that more than one future-state solution be developed for each process. Each solution should be developed based upon a different set of constraints or objectives. For example:
The Focused Improvement approach to streamlining the business process consists of eleven tasks. They are:
Note: The last task in the Focused Improvement activity is the use of IT enablers. It should not be applied until the other 10 have been completed, as it will greatly reduce the cost of implementing IT solutions. In Focused Improvement, best current IT practices are considered. E-business solutions in the 1990s were considered process reengineering applications as they pushed the state of the art. Today they are considered current-state solutions and as such became a Focused Improvement tool. Advanced IT solutions evolve around voice recognition and mobile device applications.
Each time an activity is considered to be removed or changed, the simulation model should be updated to determine the impact upon the total process. Frequently, an activity that is changed may have a positive impact on a specific part of the process, but a negative impact on the total process. The simulation model allows you to quickly determine total impact. In many other cases, an activity can be changed in a number of different ways. Each of the options needs to be evaluated from a total process standpoint before one is selected. Continue to look for the best option, not the first way of eliminating a root cause. Using Focused Improvement, the PIT typically can complete Phases I through III in 90 days.
An implementation plan will be prepared for each change.
A good measurement and feedback system is one in which the measurements are made as close to the activity as possible. Self-measurement is best because there is no delay in corrective action. Often, though, self-measurements are not practical and/or possible.
Although we need ongoing feedback to the employees involved in the process, we also need summary reports for the same people and for management. The summary reports should be exception reports so that masses of data do not waste management’s and the employee’s time. Exception reporting allows everyone to focus in on where improvements can be made.
, IBM
, 3-M, Corning
, Nutrasweet
, McDonnell Douglas
--and you will get a resounding yes. The following are some typical examples of results:
McDonnell Douglas
Federal-Mogul
Aetna Life and Casualty Co.
To be competitive today does not mean that you need to throw away your current processes and start over. In over 80% of the cases, the current process can be redesigned to give the organization the needed performance improvement to make it very competitive and to grow the organization's market share.
H. James Harrington
H. James Harrington is a American author, engineer, entrepreneur, and consultant in performance improvement. Over his career he has developed many concepts, including poor-quality cost and business process improvement....
in the early 1980s and is applied to the current process to remove all of its waste and to streamline its activities. It first streamlines the processes, and then uses IT techniques to perform the routine and repetitive activities. It is effective at reducing cost and cycle time between 20-60% and improving quality from 40-200%.
Definition
The Process Redesign methodology consists of five phases as shown in Figure 1 below.Benefits
The benefits of Process Redesign are:- It documents and quantifies the current process.
- It prepares a simulation model of the current and future state processes.
- It reduces cost and cycle time between 30-60%.
- It improves quality between 40-200%.
- It reduces risk by 50-100%.
- It increases customer satisfaction.
- It reduces internal conflict.
Features
The major features of Process Redesign are:- It boxes in the current process.
- It prepares a value-state map for the current process.
- It develops three alternative future-state solutions.
- It provides value analysis to the current-state process.
- It provides simplification to the current state process.
- It applies error proofing to the future-state solution.
- It applies risk analysis to the future-state solution.
- It provides bureaucracy elimination to the current-state process.
- It applies cycle time reduction to the current-state process.
- It has a customer-improvement phase built in to the methodology.
- It focuses on good communication of the future-state solution.
- It uses IT approaches to refine the future-state solution.
- It uses Lean approaches to refine the future-state processes
Background
The Process Redesign approach started in IBMIBM
International Business Machines Corporation or IBM is an American multinational technology and consulting corporation headquartered in Armonk, New York, United States. IBM manufactures and sells computer hardware and software, and it offers infrastructure, hosting and consulting services in areas...
during the early 1980s. It was refined through the 1980s and it became a tool used by Ernst & Young
Ernst & Young
Ernst & Young is one of the largest professional services networks in the world and one of the "Big Four" accountancy firms, along with Deloitte, KPMG and PricewaterhouseCoopers ....
in the early 1990s. It was first published to the general public in Business Process Improvement – the Breakthrough Strategy for Total Quality, Productivity, and Competitiveness, published by McGraw-Hill
McGraw-Hill
The McGraw-Hill Companies, Inc., is a publicly traded corporation headquartered in Rockefeller Center in New York City. Its primary areas of business are financial, education, publishing, broadcasting, and business services...
published in 1991 and authored by H. James Harrington.
Overall Process
Process Redesign is very different from Process Reengineering. Process Redesign operates under the concept that the current process has many good features and that the current process could be redefined and streamlined. A typical Process Redesign approach takes about 30 days to develop a future-state solution.Process Reengineering operates under the belief that the current process is so obsolete that it should be ignored and the redesign team should start over from scratch and design a totally new process. This typically takes between nine - twelve months to accomplish. Typically Process Reengineering is applied to a process when cost or cycle time needs to be improved between 60-90%. In other words, when a current process is being performed by a 100 people and to be competitive, it needs to be done by less than 40 people. Only about 10% of the process improvement activities need to be reengineered.
How to Improve Your Business Processes
The complexity of our business environment and the many organizations involved in the critical business processes make it necessary to develop a very formal approach to Process Redesign. This methodology is conveniently divided into five sub-processes called "phases" that consist of 25 different activities.- Phase I Organizing for Improvement (7 activities)
- Phase II Understanding the Process (6 activities)
- Phase III Streamlining the Process (4 activities)
- Phase IV Implementation, Measurements and Controls (5 activities)
- Phase V Continuous Improvement (3 activities)
Phase I - Organizing For Improvement
During Phase I, upper management is trained on the Process Redesign methodology, selects the critical processes and assigns someone (the process owner) who will be held responsible for improving the selected process’ total performance, even though parts of the process include activities performed in more than one function. The process owners organize a Process Improvement Team (PIT) that sets boundaries, establishes total process measurements, identifies process improvement objectives, and develops a project plan.Activity 1 - Defining Critical Business Processes
There are thousands of business processes going on all the time within most organizations. Management needs to select a few key processes for the organization to focus on. One to three critical processes are normally selected to start the improvement process.To define the critical business processes the executive team should look at each macro process and define three to ten major processes included in each macro process. Once a list of 30 or more major processes are identified, the Executive Improvement Team (EIT) needs to establish a prioritization matrix based upon the organization’s business plan, competitive positioning, its core capabilities and competencies, and the key process issues like changeability, opportunity for improvement, impact on the external customer, etc. The executive team should then develop a prioritization index for each of the major processes, using real data if possible, by first selecting the ten processes that have the highest priority and then selecting one to three of these processes that will be started first.
Activity 2 - Selecting Process Owners
It is the lack of ownership of the total businesses process that is creating the major problem. To offset this lack of process ownership, management should appoint a process owner for the processes selected in Phase I, Activity 1; they should select someone whose salary and future growth will be based upon how well the total process performs. Management should select the process owner from the people who have a lot to gain from improving the total process performance. For example, if the process selected in Activity 1 was New Product Development, the Product Engineering manager might be selected as the process owner. This additional assignment will increase the process owner’s workload for a period of 3 to 4 months but, in the long run, it will greatly reduce his or her total workload because the process itself will become more effective, efficient, and adaptable.Activity 3 - Defining Preliminary Boundaries
One of the first jobs the process owner undertakes is to define where the process starts and where it ends. This is harder than it sounds because different people involved with the same process see it in very different ways. It is important that the process owner defines the process broadly enough to resolve known problems, while being careful not to make it so large that it becomes unmanageable. The larger the process is defined, the more opportunity there is for improvement. Let’s use the New Product Development process as an example. It could start when marketing conducts its surveys, or it could start when marketing delivers the product requirements to development engineering. It could end when the product specifications are released or when the first product is delivered to an external customer. Depending on the size of the organization, and the number of departments that are involved, the boundaries are set. It is always desirable to make the process as large as possible so that the opportunities for improvement are great, without making the PIT unwieldy. The PIT should have between six to twelve members.Activity 4 - Forming and Training Process Improvement Teams
The process owner should then block diagram the process down to the department level. Each major department involved in the process should be represented on the PIT. If the department is significantly involved in the selective process, the department manager should assign a representative to serve on the PIT. The PIT will then be trained in basic team skills, because no team should meet until it has been trained in the basic team tools first.Training for the following ten fundamental Process Redesign tools can be provided on a just-in-time basis.
- Process Redesign concepts.
- Flowcharting.
- Interviewing techniques.
- Process Redesign measurement methods.
- No-value-added activity elimination methods.
- Bureaucracy elimination.
- Process and paperwork simplification techniques.
- Simple language analysis and methods.
- Process walk-through methods.
- Cost and cycle time analysis (activity based costing).
Activity 5 - Boxing In the Process
When the process is boxed-in, all the departments involved in the process, all the major inputs to the process, and all the major outputs are defined to the best of the PIT’s knowledge. The PIT will now establish the finalized beginning and end boundaries plus upper and lower boundaries. The addition of the upper and lower boundaries completes boxing in the process. The upper boundary is used to define where inputs enter the process at points within the process. The lower boundary is used to define what leaves the process from points within the process.Activity 6 - Establishing Measurements and Controls
The PIT will now look at the total process to determine how it should be measured. Measurements for efficiency, effectiveness and frequently for adaptability needs to be established at this point. Don’t stop when you define your internal customer requirements. If you only look at you internal customer you may miss the real business objective. Once the desired measurements are defined, the PIT should establish a system for collecting the measurement data on an ongoing basis. Initial values should be established as soon as possible. It is important that not only average values be determined but that minimum and maximum values are also measured, since it is often the exception to the norm that loses a good customer.Activity 7 - Developing Project and Change Management Plans
The PIT now needs to prepare a project plan for the process under study. The project plan will include:- The PIT mission
- The name of the project.
- A list of key measurements and improvement goals.
- Timetable for performing the analysis.
- A change management plan to prepare the process stakeholders for the new process.
- Resources required to complete Phases II and III.
The importance of establishing a good process change plan and implementing it cannot be overemphasized. The objectives of the Change Management Plan should be to:
- Maximize the degree of commitment that the sponsors have to the change.
- Minimize the degree of resistance that the individuals that live in and with the process will have to the change.
- Maximize the effectiveness of the change implementation team.
- Minimize the time and resources required to implement the change.
Phase II - Understanding The Process
Unfortunately, most business processes are not documented, and often when they are documented, the processes are not followed. During this phase the PIT will draw a picture of the present process (“as-is” process), analyze compliance to present procedures, collect cost and cycle time data, and align the day-to-day activities with the procedures. There are six activities in this phase.The purpose of Phase II is for the PIT to gain detailed knowledge of the process and its matrices (cost, cycle time, processing time, error rates, etc.). The flowchart and simulation model of the present process (the “as-is” model of the process) will be used to improve the process during Phase III.
Activity 1 - Flowcharting the Process
There are many different types of flowcharts that can be used to draw a picture of the business process. Some of the most common are:- Block Diagram.
- ANSI Standard.
- Geographic.
- Functional.
- Data Flow.
The PIT team now will block diagram the total process, following the process flow. Using the block diagram, start with the inputs to the process and develop the flowchart so that all activities within the process under study have been charted. Normally, flowcharts go down to the activity level only but often some important activities are flowcharted down to the task level. Once you have completed the flowchart, look at each block on the flowchart and estimate the following:
- Processing time.
- Cycle time.
- Cost per activity.
- Percentage of items that go through that activity.
At this point in time, the processing time, cycle time and cost are based upon the best judgment of the PIT. Later on in this phase, actual data will be collected.
Activity 2 - Preparing the Simulation Model
The data developed during the flowcharting activity is put into a computer along with other information like controlling documents, where the activity is performed, cost, cycle time, and processing time estimates. The computer program will define the process’ critical path, overall processing time, cycle time, and cost per cycle. The computer program will also regroup the data so that it can be flowcharted in any one of the many flowchart conventions, providing the PIT with a number of ways to look at the process. There is a great deal of value in looking at the process in different ways. As actual data is collected, it will be used to update the simulation model. This model will also be used during Phase III to evaluate the impact of proposed changes to the total process.The importance of developing a simulation model cannot be over-emphasized. It is a monumental job to try to accumulate and manipulate the data that is involved in analyzing a business process by hand. There are a number of good software packages. Among them are: WorkDraw from EDGE Software Inc., Pleasanton, California; and Envision written by Future Tech Systems Inc., Auburn, Washington.
Activity 3 - Conduct a Process Walk-Through
The PIT is now divided into two- or three-member teams. These walk-through teams personally observe each activity in the process and interview the employees performing the activity. Typical information collected related to each activity includes problems the operator is having, how the activity is performed, cycle time, costs, etc. This information is then used to update the simulation model.Activity 4 - Performing Process Cost and Cycle Time Analysis
Although the walk-through teams do their best to collect actual processing costs, processing time, and cycle time during the walk-through activity, there are often voids in the data and frequently, the total processing time exceeds the available head count actually performing the activity. During this activity, validity checks are made on the basic information and voids are filled in.Activity 5 - Implementing Quick Fixes
By now the PIT should have identified many opportunities to improve the process. Many of them are things that can be done right away at little or no cost. These quick fixes often can save a lot of money and/or improve performance. As a rule of thumb, the change that has a three-month savings of three times the implementation cost should be implemented at this time. In this activity, the PIT eliminates the dumb things that are going on in the process.Activity 6 - Aligning the Process and the Procedures
The process walk-through usually reveals a number of activities that are not being performed in accordance with the documentation. If the employees have identified a better way of performing the activity, the procedure should be modified to reflect the present method. On the other hand, in cases where the present procedures are correct, employees who are not following the procedure should be retrained.Phase III - Streamlining the Process
The streamlining phase of Process Redesign is the most critical and the most interesting. It is during this phase of the Process Redesign methodology that the creative juices of the PIT members are really put into action. The streamlining phase consists of four activities as shown in Figure 2 below.We recommend that more than one future-state solution be developed for each process. Each solution should be developed based upon a different set of constraints or objectives. For example:
- Solution 1 – Not implementing financial or time constraints.
- Solution 2 – What if you only had $100,000 to implement the solution?
- Solution 3 – What if you had to have the solution implemented within 6 months?
- Solution 4 – What if you totally need to improve cycle time without having a negative impact on quality or cost?
Activity 1 - Focused Improvement
This approach takes the present process and removes waste while reducing cycle time and improving the process effectiveness. After the process is simplified, automation and information technology (IT) is applied, maximizing the process’ ability to improve effectiveness, efficiency and adaptability measurements. This is called Focused Improvement since it focuses its efforts on the present process. It results in improvements that range between 300% and 1000%, or reduces cost and cycle times by 40% to 60%. Focused Improvement is the improvement methodology most frequently used because the risks are lower and the costs are usually less. This is the right answer for approximately 80% of the business processes.The Focused Improvement approach to streamlining the business process consists of eleven tasks. They are:
- Bureaucracy Elimination.
- Value-Added Assessment.
- Duplication Elimination.
- Simplification.
- Cycle Time Reduction.
- Error Proofing.
- Process Upgrading.
- Simple Language.
- Standardization.
- Supplier Partnership.
- Automation, Mechanization, Computerization and Information Technology.
Note: The last task in the Focused Improvement activity is the use of IT enablers. It should not be applied until the other 10 have been completed, as it will greatly reduce the cost of implementing IT solutions. In Focused Improvement, best current IT practices are considered. E-business solutions in the 1990s were considered process reengineering applications as they pushed the state of the art. Today they are considered current-state solutions and as such became a Focused Improvement tool. Advanced IT solutions evolve around voice recognition and mobile device applications.
Each time an activity is considered to be removed or changed, the simulation model should be updated to determine the impact upon the total process. Frequently, an activity that is changed may have a positive impact on a specific part of the process, but a negative impact on the total process. The simulation model allows you to quickly determine total impact. In many other cases, an activity can be changed in a number of different ways. Each of the options needs to be evaluated from a total process standpoint before one is selected. Continue to look for the best option, not the first way of eliminating a root cause. Using Focused Improvement, the PIT typically can complete Phases I through III in 90 days.
Activity 2 - Improvement, Cost, And Risk Analysis
After completing the designs of a number of potential future-state solutions, the PIT does an improvement, cost and risk analysis of each of the new processes. To accomplish this, the PIT needs to look at each process and estimate, with the help of the simulation model, its effectiveness, efficiency and adaptability. In addition, the PIT needs to estimate what the cost will be to implement the change, the length of time required to implement the change, the probability of success, and identify major problems in the implementation as shown in Figure 3 below.Activity 3 - Preferred Process Selection
The analysis of alternatives should be presented to the Executive Improvement Team (EIT) along with the PIT’s recommendations for the Best-Value Future-State Solution (BVFSS) alternative and how the changes should be implemented. The management team must weigh the alternatives and make a decision on how the organization’s resources will be invested. It is the duty of the EIT to identify from the alternatives the Best-Value Future-State Solution that will be implemented and the implementation team.Activity 4 - Preliminary Implementation Plan
Now the PIT will prepare a preliminary implementation plan. The plan will include experiments and pilot runs to verify the performance estimates that were made in Activity 2. This data is used to update the project file.Phase IV - Implementation, Measurements and Controls
During this phase, an implementation team is pulled together to install the selected process, measurement systems, and control systems. The new in-process measurement and control systems will be designed to ensure that there is immediate feedback to the employees, enabling them to contain the gains that have been made and to improve the process further. This phase consists of five activities. They are:- Finalized implementation plan.
- New process implementation.
- In-process measurement systems.
- Feedback data systems.
- Poor-quality cost.
Activity 1 - Finalized Implementation Plan
An implementation team is formed to prepare a detailed implementation plan and coordinate the changes. It may or may not include all the members of the original PIT. Often, Department Improvement Teams (DITs) become part of the implementation plan so that the teams within the functions that will be impacted by the change are part of the group that plan and implement the change. Sometimes the implementation team is divided into sub-teams (example: information system teams). The implementation plan usually is divided into three parts:- Short-term changes - Changes that can be done in 30 days.
- Mid-term changes - Changes that can be done in 90 days.
- Long-term changes - Changes that require more than 90 days to implement.
An implementation plan will be prepared for each change.
Activity 2 - New Process Implementation
The implementation plan and the change management plan are now united to bring about an effective overall implementation of the new process. The implementation team will maintain close control over each change to be sure that it is implemented correctly. Often, complex changes will go through a series of modeling and/or prototyping cycles to prove out the concept and to ensure smooth implementation. After each change is installed, its impact is measured to ensure it accomplishes its intent and has a positive impact upon the total process. As the change is implemented, the simulation model is updated so that it always reflects the present process.Activity 3 - In-Process Measurements
Before you can design a measurement system, you need to define requirements. Each activity on the final flowchart should be analyzed to define the customer requirements and how compliance to these requirements can be effectively evaluated. You will note that up to this point, the measurement system focused on the total process. Now the task is to develop measurements and controls for each major activity within the process.A good measurement and feedback system is one in which the measurements are made as close to the activity as possible. Self-measurement is best because there is no delay in corrective action. Often, though, self-measurements are not practical and/or possible.
Activity 4 - Feedback Systems
Measurement without feedback to the person performing the task is just another no-value-added activity. Feedback always comes before improvement. In most organizations, too much data is collected and too little is used. Employees need ongoing positive and negative feedback about their output.Although we need ongoing feedback to the employees involved in the process, we also need summary reports for the same people and for management. The summary reports should be exception reports so that masses of data do not waste management’s and the employee’s time. Exception reporting allows everyone to focus in on where improvements can be made.
Activity 5 - Poor-Quality Cost
Waste costs money. In many business processes, poor-quality costs run as high as 80% of budget. Poor-quality costs of 50% or more are common in business processes before Process Redesign is applied to them. If that is cut by 50% through the use of Process Redesign, the process is still wasting 25% of the organization’s budget and it is a gold mine for future continuous improvement. More information on Poor-Quality Cost can be found in the book, Poor-Quality Cost, by H. J. Harrington, published by Marcel Dekker, Inc., New York City, 1987.Phase V - Continuous Improvement
Now that the process has undergone a major breakthrough in performance, you cannot stop improving. This is not the end of the improvement activities; it is just the beginning. Now the process must continue to improve, usually at a much slower rate (10-20% per year), but it must continue to improve. The Natural Work Teams or Department Improvement Teams now take over.Does Process Redesign Work
Does Process Design work? Just ask any of the organizations that have tried it--Ford, BoeingBoeing
The Boeing Company is an American multinational aerospace and defense corporation, founded in 1916 by William E. Boeing in Seattle, Washington. Boeing has expanded over the years, merging with McDonnell Douglas in 1997. Boeing Corporate headquarters has been in Chicago, Illinois since 2001...
, IBM
IBM
International Business Machines Corporation or IBM is an American multinational technology and consulting corporation headquartered in Armonk, New York, United States. IBM manufactures and sells computer hardware and software, and it offers infrastructure, hosting and consulting services in areas...
, 3-M, Corning
Corning
- Businesses and organizations :* Corning Incorporated* Dow Corning* Owens Corning* Corning Museum of Glass- People :* Edwin Corning , American businessman and politician* Erastus Corning , American businessman and politician...
, Nutrasweet
NutraSweet
The NutraSweet Company makes and sells NutraSweet, their trademarked brand name for the artificial sweetener aspartame, and Neotame.Aspartame was accidentally discovered in 1965 by James M. Schlatter, a chemist with a master's degree working under Dr. Kurt Rorig, PhD, in charge of new drug research...
, McDonnell Douglas
McDonnell Douglas
McDonnell Douglas was a major American aerospace manufacturer and defense contractor, producing a number of famous commercial and military aircraft. It formed from a merger of McDonnell Aircraft and Douglas Aircraft in 1967. McDonnell Douglas was based at Lambert-St. Louis International Airport...
--and you will get a resounding yes. The following are some typical examples of results:
McDonnell Douglas
- 20-40% overhead reduction.
- 30-70% inventory reduction.
- 5-25% material cost reduction.
- 60-90% quality improvement.
- 20-40% administrative cost reduction.
Federal-Mogul
Federal-Mogul
Federal-Mogul Corporation is a global automotive supplier based in Southfield, Michigan, USA. It is one of the leading engine-parts suppliers in the United States, including engine bearings, pistons, piston pins, piston rings, cylinder liners, valve seats and guides, transmission products and...
- Reduced development process cycle time from 20 weeks to 20 business days, resulting in a 75% reduction in throughput time.
Aetna Life and Casualty Co.
Aetna
Aetna, Inc. is an American health insurance company, providing a range of traditional and consumer directed health care insurance products and related services, including medical, pharmaceutical, dental, behavioral health, group life, long-term care, and disability plans, and medical management...
- Reduced Information Technology workload by 750 employee years per year.
- Consolidated 65 property casualty claim offices to 23.
- Net income rose 50% to $207.2 million.
Summary
The process and the system which controls it represents the real problem facing business today, not the people who work within the boundaries set for them by management. Employees must work within the process and management must work on the process. The improvement efforts and their supporting systems must be directed at the process and not at the individual. This means that all functions must work together to optimize the efficiency, effectiveness, and adaptability of the total process. This can best be accomplished when one person is held accountable for the performance of the total process and is given the authority to bring together members from all the individual functions involved within the process, with the objective of maximizing its total performance.To be competitive today does not mean that you need to throw away your current processes and start over. In over 80% of the cases, the current process can be redesigned to give the organization the needed performance improvement to make it very competitive and to grow the organization's market share.