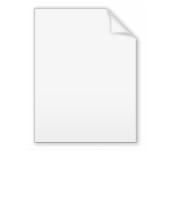
Peen plating
Encyclopedia
Mechanical plating, also known as peen plating, mechanical deposition, or impact plating, is a plating
process that imparts the coating by cold welding
fine metal particles to a workpiece. Mechanical galvanization is the same process, but applies to coatings that are thicker than 0.001 in (0.0254 mm). It is commonly used to overcome hydrogen embrittlement
problems. Commonly plated workpieces include nails, screw
s, nut
s, washer
s, stamping
s, springs
, clips, and sintered
iron
components.
The process involves tumbling the workpieces with a mixture of water, metal powder, media, and additives. Common coating materials are zinc
, cadmium
, tin
, copper
, and aluminium
.
Invented by the Tainton Company in the 1950s it was further developed by the 3M
company.
, while the media removes any residual scale
or oxide
s. Finally, accelerators, promoters and metal powder are added to the mix. The accelerators and promoters provide the proper chemical environment for the plating to occur, such as the maintenance of a pH
level of 1 to 2 to prevent oxidation and promote adhesion. The media that is already in the mixture cold welds the metal powder to the workpiece through impacts that are induced by the tumbling action of the tumbler. At this point the surface finish
is typically matte
to a semi-bright finish, however the finish can be improved with a water polish. The time required for the above process is approximately 50 minutes.
For some thinly coated workpieces a chromate passivation is necessary. Finally, the workpiece, whether passivated or not, is dried.
The media material is usually soda lime glass or a ceramic
. It is usually spherical in form, but angular shapes are also used. For plating, media usage is usually 1 part media for every workpiece, but for galvanization the ratio is 2:1. However, various sized media are used in each batch with a typical batch consisting of 50% 4–5 in (101.6–127 mm) sized beads, 25% 2–2.5 in (50.8–63.5 mm) sized beads, and 25% 1–1.25 in (25.4–31.8 mm) sized beads. The smaller media are omitted when the workpiece has a cavity that the media can get caught in, such as a fastener's recessed head. Note that the media is reused many times.
This process works better if the workpieces' surface finish
is slightly rough.
or stainless steel
and lined with an acid and abrasion resistant material, such as neoprene
, polypropylene
, and polybutylene
. The barrel sizes range from 0.04 cubic metre, however the working volume is only 25 to 35% of the total volume. For most plating applications the tumbler is rotated at 60 RPM, however it can vary. If the speed is too fast then lumpy deposits will form on the workpieces, but if the speed is too slow then the metal powder will not deposit onto the workpiece.
The separator separates the coated workpieces from the media after coating. It can be as simple as a screen with water nozzles or as complicated as a vibratory system with magnetic separators. A media handling machine then takes the separated media and transports it to a storage tank for reuse.
The separated workpieces are then taken to a dryer to remove any moisture. Usually centrifugal dryers are used, however oven are used for larger parts or loads.
does, it still offers equivalent corrosion
protection. There is a great cost savings in using mechanical plating over electroplating on hardened workpieces, because the electroplating processes requires a pre- and post-plating operation to overcome hydrogen embrittlement problems. Moreover, because mechanical plating occurs at room temperature there is no tempering of hardened workpieces.
Another advantage is that mechanical plating evenly coats all surfaces and features, unlike electroplating which has issues plating recesses. Mechanical plating can evenly coat up to 75 μm thick. For thicker plating mechanical plating is especially cost advantageous versus electroplating, because the cycle time does not increase much for the thicker plating, unlike electroplating.
One of the disadvantages is the processes size limitations. Workpieces heavier than 1 lb (0.45359237 kg) can be damaged by the process, while flat lightweight workpieces tend to stick together so they are not properly plated.
Plating
Plating is a surface covering in which a metal is deposited on a conductive surface. Plating has been done for hundreds of years, but it is also critical for modern technology...
process that imparts the coating by cold welding
Cold welding
Cold or contact welding is a solid-state welding process in which joining takes place without fusion/heating at the interface of the two parts to be welded. Unlike in the fusion-welding processes, no liquid or molten phase is present in the joint....
fine metal particles to a workpiece. Mechanical galvanization is the same process, but applies to coatings that are thicker than 0.001 in (0.0254 mm). It is commonly used to overcome hydrogen embrittlement
Hydrogen embrittlement
Hydrogen embrittlement is the process by which various metals, most importantly high-strength steel, become brittle and fracture following exposure to hydrogen...
problems. Commonly plated workpieces include nails, screw
Screw
A screw, or bolt, is a type of fastener characterized by a helical ridge, known as an external thread or just thread, wrapped around a cylinder. Some screw threads are designed to mate with a complementary thread, known as an internal thread, often in the form of a nut or an object that has the...
s, nut
Nut (hardware)
A nut is a type of hardware fastener with a threaded hole. Nuts are almost always used opposite a mating bolt to fasten a stack of parts together. The two partners are kept together by a combination of their threads' friction, a slight stretch of the bolt, and compression of the parts...
s, washer
Washer (hardware)
A washer is a thin plate with a hole that is normally used to distribute the load of a threaded fastener, such as a screw or nut. Other uses are as a spacer, spring , wear pad, preload indicating device, locking device, and to reduce vibration...
s, stamping
Stamping (metalworking)
Stamping includes a variety of sheet-metal forming manufacturing processes, such as punching using a machine press or stamping press, blanking, embossing, bending, flanging, and coining. This could be a single stage operation where every stroke of the press produce the desired form on the sheet...
s, springs
Spring (device)
A spring is an elastic object used to store mechanical energy. Springs are usually made out of spring steel. Small springs can be wound from pre-hardened stock, while larger ones are made from annealed steel and hardened after fabrication...
, clips, and sintered
Sintering
Sintering is a method used to create objects from powders. It is based on atomic diffusion. Diffusion occurs in any material above absolute zero, but it occurs much faster at higher temperatures. In most sintering processes, the powdered material is held in a mold and then heated to a temperature...
iron
Iron
Iron is a chemical element with the symbol Fe and atomic number 26. It is a metal in the first transition series. It is the most common element forming the planet Earth as a whole, forming much of Earth's outer and inner core. It is the fourth most common element in the Earth's crust...
components.
The process involves tumbling the workpieces with a mixture of water, metal powder, media, and additives. Common coating materials are zinc
Zinc
Zinc , or spelter , is a metallic chemical element; it has the symbol Zn and atomic number 30. It is the first element in group 12 of the periodic table. Zinc is, in some respects, chemically similar to magnesium, because its ion is of similar size and its only common oxidation state is +2...
, cadmium
Cadmium
Cadmium is a chemical element with the symbol Cd and atomic number 48. This soft, bluish-white metal is chemically similar to the two other stable metals in group 12, zinc and mercury. Similar to zinc, it prefers oxidation state +2 in most of its compounds and similar to mercury it shows a low...
, tin
Tin
Tin is a chemical element with the symbol Sn and atomic number 50. It is a main group metal in group 14 of the periodic table. Tin shows chemical similarity to both neighboring group 14 elements, germanium and lead and has two possible oxidation states, +2 and the slightly more stable +4...
, copper
Copper
Copper is a chemical element with the symbol Cu and atomic number 29. It is a ductile metal with very high thermal and electrical conductivity. Pure copper is soft and malleable; an exposed surface has a reddish-orange tarnish...
, and aluminium
Aluminium
Aluminium or aluminum is a silvery white member of the boron group of chemical elements. It has the symbol Al, and its atomic number is 13. It is not soluble in water under normal circumstances....
.
Invented by the Tainton Company in the 1950s it was further developed by the 3M
3M
3M Company , formerly known as the Minnesota Mining and Manufacturing Company, is an American multinational conglomerate corporation based in Maplewood, Minnesota, United States....
company.
Process
The process begins with a descaling and removing soil from the workpiece. This can be done in the tumbler or in a separate cleaning system. After cleaning, the parts are prepared by combining them with water, media, and a surface conditioner. The surface conditioner lightly coats the workpiece in copperCopper
Copper is a chemical element with the symbol Cu and atomic number 29. It is a ductile metal with very high thermal and electrical conductivity. Pure copper is soft and malleable; an exposed surface has a reddish-orange tarnish...
, while the media removes any residual scale
Scale
-Length:* Architect's scale, a ruler-like device which facilitates the production of technical drawings* Engineer's scale, a ruler-like device similar to the Architect's scale, they are helpful when drawing rooms...
or oxide
Oxide
An oxide is a chemical compound that contains at least one oxygen atom in its chemical formula. Metal oxides typically contain an anion of oxygen in the oxidation state of −2....
s. Finally, accelerators, promoters and metal powder are added to the mix. The accelerators and promoters provide the proper chemical environment for the plating to occur, such as the maintenance of a pH
PH
In chemistry, pH is a measure of the acidity or basicity of an aqueous solution. Pure water is said to be neutral, with a pH close to 7.0 at . Solutions with a pH less than 7 are said to be acidic and solutions with a pH greater than 7 are basic or alkaline...
level of 1 to 2 to prevent oxidation and promote adhesion. The media that is already in the mixture cold welds the metal powder to the workpiece through impacts that are induced by the tumbling action of the tumbler. At this point the surface finish
Surface finish
Surface finish, also known as surface texture, is the characteristics of a surface. It has three components: lay, surface roughness, and waviness.-Lay:...
is typically matte
Matte
Matte may refer to:In film:* Matte , filmmaking and video production technology* Matte painting, a process of creating sets used in film and video* Matte box, a camera accessory for controlling lens glare...
to a semi-bright finish, however the finish can be improved with a water polish. The time required for the above process is approximately 50 minutes.
For some thinly coated workpieces a chromate passivation is necessary. Finally, the workpiece, whether passivated or not, is dried.
The media material is usually soda lime glass or a ceramic
Ceramic
A ceramic is an inorganic, nonmetallic solid prepared by the action of heat and subsequent cooling. Ceramic materials may have a crystalline or partly crystalline structure, or may be amorphous...
. It is usually spherical in form, but angular shapes are also used. For plating, media usage is usually 1 part media for every workpiece, but for galvanization the ratio is 2:1. However, various sized media are used in each batch with a typical batch consisting of 50% 4–5 in (101.6–127 mm) sized beads, 25% 2–2.5 in (50.8–63.5 mm) sized beads, and 25% 1–1.25 in (25.4–31.8 mm) sized beads. The smaller media are omitted when the workpiece has a cavity that the media can get caught in, such as a fastener's recessed head. Note that the media is reused many times.
This process works better if the workpieces' surface finish
Surface finish
Surface finish, also known as surface texture, is the characteristics of a surface. It has three components: lay, surface roughness, and waviness.-Lay:...
is slightly rough.
Equipment
The most important piece of equipment in the process is the tumbler. It is constructed of steelSteel
Steel is an alloy that consists mostly of iron and has a carbon content between 0.2% and 2.1% by weight, depending on the grade. Carbon is the most common alloying material for iron, but various other alloying elements are used, such as manganese, chromium, vanadium, and tungsten...
or stainless steel
Stainless steel
In metallurgy, stainless steel, also known as inox steel or inox from French "inoxydable", is defined as a steel alloy with a minimum of 10.5 or 11% chromium content by mass....
and lined with an acid and abrasion resistant material, such as neoprene
Neoprene
Neoprene or polychloroprene is a family of synthetic rubbers that are produced by polymerization of chloroprene. Neoprene in general has good chemical stability, and maintains flexibility over a wide temperature range...
, polypropylene
Polypropylene
Polypropylene , also known as polypropene, is a thermoplastic polymer used in a wide variety of applications including packaging, textiles , stationery, plastic parts and reusable containers of various types, laboratory equipment, loudspeakers, automotive components, and polymer banknotes...
, and polybutylene
Polybutylene
Polybutylene is a polyolefin or saturated polymer with the chemical formula n. It should not be confused with polybutene, a low molecular weight oligomer with a different repeat unit....
. The barrel sizes range from 0.04 cubic metre, however the working volume is only 25 to 35% of the total volume. For most plating applications the tumbler is rotated at 60 RPM, however it can vary. If the speed is too fast then lumpy deposits will form on the workpieces, but if the speed is too slow then the metal powder will not deposit onto the workpiece.
The separator separates the coated workpieces from the media after coating. It can be as simple as a screen with water nozzles or as complicated as a vibratory system with magnetic separators. A media handling machine then takes the separated media and transports it to a storage tank for reuse.
The separated workpieces are then taken to a dryer to remove any moisture. Usually centrifugal dryers are used, however oven are used for larger parts or loads.
Advantages and disadvantages
The greatest advantage of the process is its ability to overcome hydrogen embrittlement problems, which is important for workpieces that have a hardness greater than HRC 40. Note that there still is some embrittlement of the workpiece. While this process does not cause problems with hydrogen embrittlement, and electroplatingElectroplating
Electroplating is a plating process in which metal ions in a solution are moved by an electric field to coat an electrode. The process uses electrical current to reduce cations of a desired material from a solution and coat a conductive object with a thin layer of the material, such as a metal...
does, it still offers equivalent corrosion
Corrosion
Corrosion is the disintegration of an engineered material into its constituent atoms due to chemical reactions with its surroundings. In the most common use of the word, this means electrochemical oxidation of metals in reaction with an oxidant such as oxygen...
protection. There is a great cost savings in using mechanical plating over electroplating on hardened workpieces, because the electroplating processes requires a pre- and post-plating operation to overcome hydrogen embrittlement problems. Moreover, because mechanical plating occurs at room temperature there is no tempering of hardened workpieces.
Another advantage is that mechanical plating evenly coats all surfaces and features, unlike electroplating which has issues plating recesses. Mechanical plating can evenly coat up to 75 μm thick. For thicker plating mechanical plating is especially cost advantageous versus electroplating, because the cycle time does not increase much for the thicker plating, unlike electroplating.
One of the disadvantages is the processes size limitations. Workpieces heavier than 1 lb (0.45359237 kg) can be damaged by the process, while flat lightweight workpieces tend to stick together so they are not properly plated.