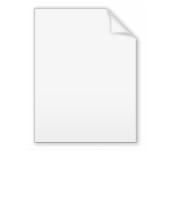
Iron Metallurgy in Africa
Encyclopedia
African iron metallurgy encompasses a study of iron production across the continent and an understanding of how it influenced aspects of African archaeology. Extraordinary diversity has originated from iron production creating advanced farming techniques through tools, deadly warfare and valuable items for trade. These developments subsequently influenced social, cultural and political aspects of African life.
in Africa is hotly disputed by archaeologists. The first evidence for iron in Africa dates back as far as the second millennium BC (Bocoum (ed.) 2002). The vast scale of the continent, accessibility, political and cultural barriers have caused difficulties in finding a good database of evidence to help diagnose when and where origins lie. It has now been recognised that trying to put the origins in some kind of chronological order is not currently possible with the archaeological evidence available and controversial when attempted.
Archaeologists hold several standpoints on the origins of iron production in Africa:
1. Indigenous Invention
Some archaeologists believe that it was indigenously invented without influence from outside countries already practising production. It is possible that the process was an innovation of the smelting techniques already used in Africa to make copper. Iron oxides were used as a flux in the copper smelting process and so with some experimentation the process could have resulted in accidental production of iron, which could have then been developed into purely iron smelting. However although copper was smelted in some regions before iron, evidence for copper production is relatively low due to the poor preservation of copper production techniques. If earlier evidence of copper smelting could be found it would strongly support the argument. The only real evidence from copper smelting is the remaining slag. However in the field this can often be confused for iron slag without metallographic analysis.
2. Diffusion from surrounding continents
The second argument is that techniques were brought to the continent by surrounding countries by diffusion. Proposed routes by the diffusion process either could be running south to West from Meroe on the Nubian Isle (Childs et al. 2005, pg 278). Or some believe it came on a path from Egypt which dispersed the methods from the North to the Sub-Saharan Africa.
3. Multiple Origins
Africa is a massive continent with extreme geographical context (such as the Sahara dessert separating the North), and so it took time for iron production to spread, resulting in suggestions that there were multiple places of origin. The rich geological distribution of iron ore means they had the raw material readily available creating a high potential for multiple origins of production. Other necessary resources available to a region such as wood and water would have influenced these localities. From archaeological evidence through to production methods used in parts of Africa today there is such diversity in traditions and techniques that for it to have all began from one place and one technique can seem unlikely (Holl 2000, pg 9).
A good example of the issues that arise when trying to implement a theory is a site at the Termit Mountains, in eastern Niger. Artefacts of copper and iron where found which dated as far back as ca 1500 BC and furnaces dating back to ca 800 BC. So does this suggest that the community was importing these objects before they started to produce it themselves or worked out the technology to produce it themselves? Or was it simply that the archaeological evidence for the earlier furnaces did not survive whilst the artefacts themselves did (Childs et al. 2005 pg 278)? Whilst a definite conclusion cannot be put to these situations its important to bear in mind other aspects of the problem, such as is there any evidence for mining, beneficiation, are there the local resources available such as wood, iron ore, water or would they have had to be traded in? Also iron production techniques were kept a closely guarded secret and so perhaps this influenced the time it took for them to be able to implement the technique.
of iron ore can also be used as evidence; however it is possible that after beneficiation
the ore travelled far to the next stage of production. Evidence for mining is often lost due to more recent mining of iron ore outcrops. Dating can be done through slag analysis and radiocarbon dating of the charcoal used to fuel the furnace. Both of these pieces of evidence are useful as they will always be produced in all smelting even if the technique varies. Metallography
and petrographic analysis are also performed on specimens of slag and charcoal to help understand the conditions created within the furnace. Archaeologists have made reconstructions of the technology used for iron smelting as an important process in understanding how the ancient technology worked and to inspire confidence that their perception of the techniques used are correct.
, magnetite
and limonite
(Childs et al. 2005 pg 282). The production process included mining, beneficiation
, travel, smithing and forging
. The mining and preparation of ores was carried out by men, women and children. It is likely that beneficiation
occurred relatively near the site so the iron ore was then ready for transportation to the smelting site or alternatively ready to be traded. The original iron production technique in Africa is thought to have been the ‘bloomery
process’. Bowl, shaft and natural draft furnaces have been recovered. Iron ore would be put into a furnace along with charcoal at temperatures ranging 1,100- 1,200oC. For this process it would have been necessary for the smelters to use tuyères to blow oxygen into the furnace creating the high temperatures necessary. As the iron separated from the waste slag the raw iron product is called the bloom. The bloom is then removed, reheated and forged by a smith into shapes for use. Evidence from the shape of slag found at smelting sites suggested the furnaces were tapped.
The Iron Age of Africa was based around the agricultural revolution, driven by the use of iron tools. Tools for cultivation and farming made production far more efficient and possible on much larger scales. Fishing hooks, arrow heads and spears aided hunting. Iron weapons also influenced warfare. These items, in addition to the production of other iron goods helped stimulate economic activity, the rise of chiefdoms and even states. The control of iron production was often by ironworkers themselves, or a “central power” in larger societies such as kingdoms or states (Barros 2000, pg154). The demand for trade is believed to have resulted in some societies working only as smelters or smiths, specialising in just one of the many skills necessary to the production process. It is possible that this also led to tradesmen specialising in transporting and trading iron (Barros 2000, pg152). However not every region benefited from industrialising iron production, some suffered environmentally from problems that arose due to the massive deforestation required to provide the charcoal for fuelling furnaces (for example the ecological crisis of the Mema Region (Holl 2000, pg48)).
Iron smelters and smiths received different social status depending on their culture. Some were lower in society due to the aspect of manual labour and associations with witchcraft, for example in the Maasai and Tuareg (Childs et al. 2005 pg 288). In other cultures the skills are often passed down through family and would receive great social status (sometimes even considered as witchdoctors) within their community. Their powerful knowledge allowed them to produce materials on which the whole community relied. In some communities they were believed to have such strong supernatural powers that they were regarded as highly as the king or chief. For example an excavation at the royal tomb of King Rugira (Great Lakes, Eastern Africa) found two iron anvils placed at his head (Childs et al. 2005, pg 288 in Herbert 1993:ch.6), suggesting their importance and powerful significance. In some cultures mythical stories have been built around the premise of the iron smelter emphasising their god like significance.
Some cultures associated sexual symbolism with iron production. Smelting is integrated with the fertility of their society, as with natural reproduction the production of the bloom is compared to the conception and birth. There are many strict taboos surrounding the process. The smelting process is carried out entirely by men and often away from the village. For women to touch any of the materials or be present could jeopardise the success of the production. With the men away from the fertile women it reduces temptation which otherwise could depreciate the productivity of the smelt. The furnaces are also often extravagantly adorned to resemble a woman, the mother of the bloom.
Origins
The origin of iron metallurgyMetallurgy
Metallurgy is a domain of materials science that studies the physical and chemical behavior of metallic elements, their intermetallic compounds, and their mixtures, which are called alloys. It is also the technology of metals: the way in which science is applied to their practical use...
in Africa is hotly disputed by archaeologists. The first evidence for iron in Africa dates back as far as the second millennium BC (Bocoum (ed.) 2002). The vast scale of the continent, accessibility, political and cultural barriers have caused difficulties in finding a good database of evidence to help diagnose when and where origins lie. It has now been recognised that trying to put the origins in some kind of chronological order is not currently possible with the archaeological evidence available and controversial when attempted.
Archaeologists hold several standpoints on the origins of iron production in Africa:
1. Indigenous Invention
Some archaeologists believe that it was indigenously invented without influence from outside countries already practising production. It is possible that the process was an innovation of the smelting techniques already used in Africa to make copper. Iron oxides were used as a flux in the copper smelting process and so with some experimentation the process could have resulted in accidental production of iron, which could have then been developed into purely iron smelting. However although copper was smelted in some regions before iron, evidence for copper production is relatively low due to the poor preservation of copper production techniques. If earlier evidence of copper smelting could be found it would strongly support the argument. The only real evidence from copper smelting is the remaining slag. However in the field this can often be confused for iron slag without metallographic analysis.
2. Diffusion from surrounding continents
The second argument is that techniques were brought to the continent by surrounding countries by diffusion. Proposed routes by the diffusion process either could be running south to West from Meroe on the Nubian Isle (Childs et al. 2005, pg 278). Or some believe it came on a path from Egypt which dispersed the methods from the North to the Sub-Saharan Africa.
3. Multiple Origins
Africa is a massive continent with extreme geographical context (such as the Sahara dessert separating the North), and so it took time for iron production to spread, resulting in suggestions that there were multiple places of origin. The rich geological distribution of iron ore means they had the raw material readily available creating a high potential for multiple origins of production. Other necessary resources available to a region such as wood and water would have influenced these localities. From archaeological evidence through to production methods used in parts of Africa today there is such diversity in traditions and techniques that for it to have all began from one place and one technique can seem unlikely (Holl 2000, pg 9).
A good example of the issues that arise when trying to implement a theory is a site at the Termit Mountains, in eastern Niger. Artefacts of copper and iron where found which dated as far back as ca 1500 BC and furnaces dating back to ca 800 BC. So does this suggest that the community was importing these objects before they started to produce it themselves or worked out the technology to produce it themselves? Or was it simply that the archaeological evidence for the earlier furnaces did not survive whilst the artefacts themselves did (Childs et al. 2005 pg 278)? Whilst a definite conclusion cannot be put to these situations its important to bear in mind other aspects of the problem, such as is there any evidence for mining, beneficiation, are there the local resources available such as wood, iron ore, water or would they have had to be traded in? Also iron production techniques were kept a closely guarded secret and so perhaps this influenced the time it took for them to be able to implement the technique.
Archaeological evidence
Archaeological evidence for iron production has often been based on iron artefacts found in the field. Artefacts are often in poor condition from corrosion and can be unidentifiable. Basing a context of origins to the specimens is unreliable as it is possible that the artefact may have been made somewhere completely different to where it was discovered (possibly even imported!). Solid evidence for iron production includes; the used bowl (foundation) of furnaces, tuyères and slag (from the furnace or forging process). The bloom itself and bellows are rarely found. Evidence of mining and beneficiationBeneficiation
In mining, beneficiation is a variety of processes whereby extracted ore from mining is separated into mineral and gangue, the former suitable for further processing or direct use....
of iron ore can also be used as evidence; however it is possible that after beneficiation
Beneficiation
In mining, beneficiation is a variety of processes whereby extracted ore from mining is separated into mineral and gangue, the former suitable for further processing or direct use....
the ore travelled far to the next stage of production. Evidence for mining is often lost due to more recent mining of iron ore outcrops. Dating can be done through slag analysis and radiocarbon dating of the charcoal used to fuel the furnace. Both of these pieces of evidence are useful as they will always be produced in all smelting even if the technique varies. Metallography
Metallography
Metallography is the study of the physical structure and components of metals, typically using microscopy.Ceramic and polymeric materials may also be prepared using metallographic techniques, hence the terms ceramography, plastography and, collectively, materialography.-Preparing metallographic...
and petrographic analysis are also performed on specimens of slag and charcoal to help understand the conditions created within the furnace. Archaeologists have made reconstructions of the technology used for iron smelting as an important process in understanding how the ancient technology worked and to inspire confidence that their perception of the techniques used are correct.
Techniques
Iron ore is readily available over Africa. Often a diagnostic red colour, it would have made it easy to make surface finds. Common ores used were likely to be hematiteHematite
Hematite, also spelled as haematite, is the mineral form of iron oxide , one of several iron oxides. Hematite crystallizes in the rhombohedral system, and it has the same crystal structure as ilmenite and corundum...
, magnetite
Magnetite
Magnetite is a ferrimagnetic mineral with chemical formula Fe3O4, one of several iron oxides and a member of the spinel group. The chemical IUPAC name is iron oxide and the common chemical name is ferrous-ferric oxide. The formula for magnetite may also be written as FeO·Fe2O3, which is one part...
and limonite
Limonite
Limonite is an ore consisting in a mixture of hydrated iron oxide-hydroxide of varying composition. The generic formula is frequently written as FeO·nH2O, although this is not entirely accurate as limonite often contains a varying amount of oxide compared to hydroxide.Together with hematite, it has...
(Childs et al. 2005 pg 282). The production process included mining, beneficiation
Beneficiation
In mining, beneficiation is a variety of processes whereby extracted ore from mining is separated into mineral and gangue, the former suitable for further processing or direct use....
, travel, smithing and forging
Forging
Forging is a manufacturing process involving the shaping of metal using localized compressive forces. Forging is often classified according to the temperature at which it is performed: '"cold," "warm," or "hot" forging. Forged parts can range in weight from less than a kilogram to 580 metric tons...
. The mining and preparation of ores was carried out by men, women and children. It is likely that beneficiation
Beneficiation
In mining, beneficiation is a variety of processes whereby extracted ore from mining is separated into mineral and gangue, the former suitable for further processing or direct use....
occurred relatively near the site so the iron ore was then ready for transportation to the smelting site or alternatively ready to be traded. The original iron production technique in Africa is thought to have been the ‘bloomery
Bloomery
A bloomery is a type of furnace once widely used for smelting iron from its oxides. The bloomery was the earliest form of smelter capable of smelting iron. A bloomery's product is a porous mass of iron and slag called a bloom. This mix of slag and iron in the bloom is termed sponge iron, which...
process’. Bowl, shaft and natural draft furnaces have been recovered. Iron ore would be put into a furnace along with charcoal at temperatures ranging 1,100- 1,200oC. For this process it would have been necessary for the smelters to use tuyères to blow oxygen into the furnace creating the high temperatures necessary. As the iron separated from the waste slag the raw iron product is called the bloom. The bloom is then removed, reheated and forged by a smith into shapes for use. Evidence from the shape of slag found at smelting sites suggested the furnaces were tapped.
Uses
Iron was not the only metal to be used in Africa; copper and brass were widely utilised too. However the steady spread of iron meant it must have had more favourable properties for many different uses. Its durability over copper meant that it was used to make many tools from farming pieces to weaponry. Iron was used for personal adornment in jewellery, impressive pieces of artwork and even instruments. It was used for coins and currencies of varying forms. For example kisi pennies; a traditional form of iron currency used for trading in West Africa. They are twisted iron rods ranging from <30 cm to >2m in length. Suggestions for their uses vary from marital transactions, or simply that they were a convenient shape for transportation, melting down and reshaping into a desired object. There are many different forms of iron currency, often regionally differing in shape and value. Iron did not replace other materials, such as stone and wooden tools, but the quantity of production and variety of uses met were significantly high by comparison.Social and Cultural Significance
It is important to recognise that whilst iron production had great influence over Africa both culturally in trade and expansion (Martinelli, 1993, 1996, 2004), as well as socially in beliefs and rituals, there is great regional variation. Much of the evidence for cultural significance comes from the practises still carried out today by different African cultures. Ethnographical information has been very useful in reconstructing the events surrounding iron production in the past, however the reconstructions could have become distorted through time and influence by anthropologist’s studies.The Iron Age of Africa was based around the agricultural revolution, driven by the use of iron tools. Tools for cultivation and farming made production far more efficient and possible on much larger scales. Fishing hooks, arrow heads and spears aided hunting. Iron weapons also influenced warfare. These items, in addition to the production of other iron goods helped stimulate economic activity, the rise of chiefdoms and even states. The control of iron production was often by ironworkers themselves, or a “central power” in larger societies such as kingdoms or states (Barros 2000, pg154). The demand for trade is believed to have resulted in some societies working only as smelters or smiths, specialising in just one of the many skills necessary to the production process. It is possible that this also led to tradesmen specialising in transporting and trading iron (Barros 2000, pg152). However not every region benefited from industrialising iron production, some suffered environmentally from problems that arose due to the massive deforestation required to provide the charcoal for fuelling furnaces (for example the ecological crisis of the Mema Region (Holl 2000, pg48)).
Iron smelters and smiths received different social status depending on their culture. Some were lower in society due to the aspect of manual labour and associations with witchcraft, for example in the Maasai and Tuareg (Childs et al. 2005 pg 288). In other cultures the skills are often passed down through family and would receive great social status (sometimes even considered as witchdoctors) within their community. Their powerful knowledge allowed them to produce materials on which the whole community relied. In some communities they were believed to have such strong supernatural powers that they were regarded as highly as the king or chief. For example an excavation at the royal tomb of King Rugira (Great Lakes, Eastern Africa) found two iron anvils placed at his head (Childs et al. 2005, pg 288 in Herbert 1993:ch.6), suggesting their importance and powerful significance. In some cultures mythical stories have been built around the premise of the iron smelter emphasising their god like significance.
Rituals
The smelting process was often carried out away from the rest of the community. Ironworkers became experts in rituals to encourage good production and to ward of bad spirits, including song and prayers, plus the giving of medicines and even sacrifices. The latter are usually put in the furnace itself or buried under the base of the furnace. Examples of these date back as far as the early Iron Age in Tanzania and Rwanda (Schmidt 1997 in Childs et al., 2005 pg293).Some cultures associated sexual symbolism with iron production. Smelting is integrated with the fertility of their society, as with natural reproduction the production of the bloom is compared to the conception and birth. There are many strict taboos surrounding the process. The smelting process is carried out entirely by men and often away from the village. For women to touch any of the materials or be present could jeopardise the success of the production. With the men away from the fertile women it reduces temptation which otherwise could depreciate the productivity of the smelt. The furnaces are also often extravagantly adorned to resemble a woman, the mother of the bloom.
See also
- AfricaAfricaAfrica is the world's second largest and second most populous continent, after Asia. At about 30.2 million km² including adjacent islands, it covers 6% of the Earth's total surface area and 20.4% of the total land area...
- ArchaeometallurgyArchaeometallurgyArchaeometallurgy is the study of the history and prehistory of metals and their use through humans. It is a sub-discipline of archaeology and archaeological science...
- Bantu expansionBantu expansionThe Bantu expansion or the Bantu Migration was a millennia-long series of migrations of speakers of the original proto-Bantu language group...
- BeneficiationBeneficiationIn mining, beneficiation is a variety of processes whereby extracted ore from mining is separated into mineral and gangue, the former suitable for further processing or direct use....
- BloomeryBloomeryA bloomery is a type of furnace once widely used for smelting iron from its oxides. The bloomery was the earliest form of smelter capable of smelting iron. A bloomery's product is a porous mass of iron and slag called a bloom. This mix of slag and iron in the bloom is termed sponge iron, which...
- Copper metallurgy in AfricaCopper metallurgy in AfricaCopper metallurgy in Africa encompasses the study of copper production across the continent and an understanding of how it influenced aspects of African archaeology.- Origins :...
- IronIronIron is a chemical element with the symbol Fe and atomic number 26. It is a metal in the first transition series. It is the most common element forming the planet Earth as a whole, forming much of Earth's outer and inner core. It is the fourth most common element in the Earth's crust...
- Iron ore
- MetallurgyMetallurgyMetallurgy is a domain of materials science that studies the physical and chemical behavior of metallic elements, their intermetallic compounds, and their mixtures, which are called alloys. It is also the technology of metals: the way in which science is applied to their practical use...
- MiningMiningMining is the extraction of valuable minerals or other geological materials from the earth, from an ore body, vein or seam. The term also includes the removal of soil. Materials recovered by mining include base metals, precious metals, iron, uranium, coal, diamonds, limestone, oil shale, rock...
- SlagSlagSlag is a partially vitreous by-product of smelting ore to separate the metal fraction from the unwanted fraction. It can usually be considered to be a mixture of metal oxides and silicon dioxide. However, slags can contain metal sulfides and metal atoms in the elemental form...
- SmeltingSmeltingSmelting is a form of extractive metallurgy; its main use is to produce a metal from its ore. This includes iron extraction from iron ore, and copper extraction and other base metals from their ores...
- Tuyères