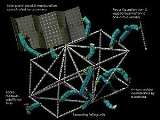
Self-Reconfiguring Modular Robotics
Encyclopedia
Modular self-reconfiguring robot
ic systems or self-reconfigurable modular robots are autonomous kinematic machines with variable morphology
. Beyond conventional actuation, sensing and control typically found in fixed-morphology robots, self-reconfiguring robots are also able to deliberately change their own shape by rearranging the connectivity of their parts, in order to adapt to new circumstances, perform new tasks, or recover from damage.
For example, a robot made of such components could assume a worm
-like shape to move through a narrow pipe, reassemble into something with spider
-like legs to cross uneven terrain, then form a third arbitrary object (like a ball or wheel that can spin itself) to move quickly over a fairly flat terrain; it can also be used for making "fixed" objects, such as walls, shelters, or buildings.
In some cases this involves each module having 2 or more connectors for connecting several together. They can contain electronics
, sensor
s, computer processors, memory
, and power supplies; they can also contain actuator
s that are used for manipulating their location in the environment and in relation with each other. A feature found in some cases is the ability of the modules to automatically connect and disconnect themselves to and from each other, and to form into many objects or perform many tasks moving or manipulating the environment.
By saying "self-reconfiguring" or "self-reconfigurable" it means that the mechanism or device is capable of utilizing its own system of control such as with actuators or stochastic means to change its overall structural shape. Having the quality of being "modular" in "self-reconfiguring modular robotics" is to say that the same module or set of modules can be added to or removed from the system, as opposed to being generically "modularized" in the broader sense. The underlying intent is to have an indefinite number of identical modules, or a finite and relatively small set of identical modules, in a mesh or matrix structure of self-reconfigurable modules.
Self-reconfiguration is also different from the concept of self-replication
, and self-replication is not necessarily a quality that a self-reconfigurable module or collection of such modules can or must possess. A matrix of N-number of modules does not need to be able to increase the quantity of modules to greater than N to be considered self-reconfigurable. It is sufficient for self-reconfigurable modules to be a device that is produced at a conventional factory, where dedicated machines stamp or mold components, and factory workers on an assembly line assemble the components to build each module.
There are two basic types of methods of segment articulation that self-reconfigurable mechanisms can utilize to reshape their structures, chain reconfiguration and lattice reconfiguration.
The modular building blocks usually consist of some primary structural actuated unit, and potentially additional specialized units such as grippers, feet, wheels, cameras, payload and energy storage and generation.
Modular robotic systems can also be classified according to the way by which units are reconfigured (moved) into place.
Modular robotic system are also generally classified depending on the design of the modules.
Other modular robotic systems exist which are not self-reconfigurable, and thus do not formally belong to this family of robots though they may have similar appearance. For example, self-assembling systems may be composed of multiple modules but cannot dynamically control their target shape. Similarly, tensegrity robotics may be composed of multiple interchangeable modules but cannot self-reconfigure.
Both these advantages have not yet been fully realized. A modular robot is likely to be inferior in performance to any single custom robot tailored for a specific task. However, the advantage of modular robotics is only apparent when considering multiple tasks that would normally require a set of different robots.
The added degrees of freedom make modular robots more versatile in their potential capabilities, but also incur a performance tradeoff and increased mechanical and computational complexities.
The quest for self-reconfiguring robotic structures is to some extent inspired by envisioned applications such as long-term space missions, that require long-term self-sustaining robotic ecology that can handle unforeseen situations and may require self repair. A second source of inspiration are biological systems that are self-constructed out of a relatively small repertoire of lower-level building blocks (cells or amino acids, depending on scale of interest). This architecture underlies biological systems’ ability to physically adapt, grow, heal, and even self replicate – capabilities that would be desirable in many engineered systems.
” has been somewhat elusive. Here are several examples:
three-dimensional replicas of people or objects, so lifelike that human senses would accept them as real. This would eliminate the need for cumbersome virtual reality gear and overcome the viewing angle limitations of modern 3D approaches. The replicas would mimic the shape and appearance of a person or object being imaged in real time, and as the originals moved, so would their replicas. One aspect of this application is that the main development thrust is geometric representation rather than applying forces to the environment as in a typical robotic manipulation task.
This project is widely known as claytronics or programmable matter.
One source of inspiration for the development of these systems comes from the application. A second source is biological systems that are self-constructed out of a relatively small repertoire of lower-level building blocks (cells or amino acids, depending on scale of interest). This architecture underlies biological systems’ ability to physically adapt, grow, heal, and even self replicate – capabilities that would be desirable in many engineered systems.
The early 1990s saw further development from Greg Chirikjian, Mark Yim, Joseph Michael, and Satoshi Murata. Chirikjian, Michael, and Murata developed lattice reconfiguration systems and Yim developed a chain based system. While these researchers started with from a mechanical engineering emphasis, designing and building modules then developing code to program them, the work of Daniela Rus and Wei-min Shen developed hardware but had a greater impact on the programming aspects. They started a trend towards provable or verifiable distributed algorithms for the control of large numbers of modules.
One of the more interesting hardware platforms recently has been the MTRAN II and III systems developed by Satoshi Murata et al. This system is a hybrid chain and lattice system. It has the advantage of being able to achieve tasks more easily like chain systems, yet reconfigure like a lattice system.
More recently new efforts in stochastic self-assembly have been pursued by Hod Lipson and Eric Klavins. A large effort at CMU headed by Seth Goldstein and Todd Mowry has started looking at issues in developing millions of modules.
Many tasks have been shown to be achievable, especially with chain reconfiguration modules. This demonstrates the versatility of these systems however, the other two advantages, robustness and low cost have not been demonstrated. In general the prototype systems developed in the labs have been fragile and expensive as would be expected during any initial development.
There is a growing number of research groups actively involved in modular robotics research. To date, about 30 systems have been designed and constructed, some of which are shown below.
A chain/tree hyper-redundant
modular robotic system invented by Charles Khairallah from Robotics Design Inc in Montreal
, Quebec
, Canada
. This robot is designed with ANAT Technology (Articulated Nimble Adaptable Trunk) and is currently used for industrial manipulating under the name ANAT AMI-100. Robotics Design's patented U and H shaped modules, of which this robot is composed, form the other robots in the ANAT robotics family. This robot can re-configure and/or self-reconfigure to form different shapes, due to its LEGO
-like sets of modules with one degree of freedom each. This allows robots to be designed using ANAT modules with n° of freedom. Configurations range from mobile robots (ANATROLLER), manipulators (ANAT AMI-100), to walking robots (ANAT Walker).
PolyBot G3 (2002)
A chain self-reconfiguration system. Each module is about 50 mm on a side, and has 1 rotational DOF. It is part of the PolyBot modular robot family that has demonstrated many modes of locomotion including walking: biped, 14 legged, slinky-like, snake-like: concertina in a gopher hole, inchworm gaits, rectilinear undulation and sidewinding gaits, rolling like a tread at up to 1.4m/s, riding a tricycle, climbing: stairs, poles pipes, ramps etc. More information can be found at the polybot webpage at PARC.
M-TRAN III (2005)
A hybrid type self-reconfigurable system. Each module is two cube size (65 mm side), and has 2 rotational DOF and 6 flat surfaces for connection. It is the 3rd M-TRAN prototypes. Compared with the former (M-TRAN II), speed and reliability of connection is largely improved. As a chain type system, locomotion by CPG (Central Pattern Generator) controller in vaious shapes has been demonstrated by M-TRAN II. As a lattice type system, it can change its configuration, e.g., between a 4 legged walker to a caterpillar like robot. See the M-TRAN webpage at AIST.
AMOEBA-I (2005)
AMOEBA-I, a three-module reconfigurable mobile robot was developed in Shenyang Institute of Automation (SIA), Chinese Academy of Sciences (CAS) by Liu J G et al.http://ieeexplore.ieee.org/xpls/abs_all.jsp?arnumber=1708645http://www.springerlink.com/content/m81820061n48jh32/.AMOEBA-I has nine kinds of non-isomorphic configurations and high mobility under unstructured environments.Four generations of its platform have been developed and a series of researches have been carried out on their reconfiguration mechanism, non-isomorphic configurations, tipover stability, and reconfiguration planning. Experiments have demonstrated that such kind structure permits good mobility and high flexibility to uneven terrain. Being hyper-redundant, modularized and reconfigurable, AMOEBA-I has many possible applications such as Urban Search and Rescue (USAR) and space exploration.
Ref_1: see http://ieeexplore.ieee.org/xpls/abs_all.jsp?arnumber=1708645;
Ref_2: see http://www.springerlink.com/content/m81820061n48jh32/
Stochastic-3D (2005)
High spatial resolution for arbitrary three-dimensional shape formation with modular robots can be accomplished using lattice system with large quantities of very small, prospectively microscopic modules. At small scales, and with large quantities of modules, deterministic control over reconfiguration of individual modules will become unfeasible, while stochastic mechanisms will naturally prevail. Microscopic size of modules will make the use of electromagnetic actuation and interconnection prohibitive, as well, as the use of on-board power storage.
Three large scale prototypes were built in attempt to demonstrate dynamically programmable three-dimensional stochastic reconfiguration in a neutral-buoyancy environment. The first prototype used electromagnets for module reconfiguration and interconnection. The modules were 100 mm cubes and weighed 0.81 kg. The second prototype used stochastic fluidic reconfiguration and interconnection mechanism. Its 130 mm cubic modules weighed 1.78 kg each and made reconfiguration experiments excessively slow. The current third implementation inherits the fluidic reconfiguration principle. The lattice grid size is 80 mm, and the reconfiguration experiments are under way. More information can be found at the CCSL Stochastic Modular Robotics webpage.
Molecubes (2005)
This chain self-reconfiguring system was built by the Cornell Computational Synthesis Lab to physically demonstrate artificial kinematic self-reproduction. Each module is a 0.65 kg cube with 100 mm long edges and one rotational degree of freedom. The axis of rotation is aligned with the cube's longest diagonal. Physical self-reproduction of a three- and a four-module robots was demonstrated. It was also shown that, disregarding the gravity constraints, an infinite number of self-reproducing chain meta-structures can be built from Molecubes. More information can be found at the CCSL Self-Replication webpage.
The Programmable Parts (2005)
The programmable parts are stirred randomly on an air-hockey table by randomly actuated air jets. When they collide and stick, they can communicate and decide whether to stay stuck, or if and when to detach. Local interaction rules can be devised and optimized to guide the robots to make any desired global shape. More information can be found at the programmable parts web page.
SuperBot (2006)
The SuperBot modules fall into the chain/tree architecture. The modules have three degrees of freedom each. The design is based on two previous systems: Conro (by the same research group) and MTRAN (by Murata et al.). Each module can connect to another module through one of its six dock connectors. They can communicate and share power through their dock connectors. Several locomotion gaits have been developed for different arrangements of modules. For high-level communication the modules use hormone-based control, a distributed, scalable protocol that does not require the modules to have unique ID's.
Miche (2006)
The Miche system is a modular lattice system capable of arbitrary shape formation. Each module is an autonomous robot module capable of connecting to and communicating with its immediate neighbors. When assembled into a structure, the modules form a system that can be virtually sculpted using a computer interface and a distributed process. The group of modules collectively decide who is on the final shape and who is not using algorithms that minimize the information transmission and storage. Finally, the modules not in the structure let go and fall off under the control of an external force, in this case gravity.
More details at Miche (Rus et al.).
Roombots (2009)
Roombots have a hybrid chain/tree architecture. Each module has three degree of freedom, two of them using the diametrical axis within a regular cube, and a third (center) axis of rotation connecting the two spherical parts. All three axes are continuously rotatory. The outer Roombots DOF is using the same axis-orientation as Molecubes, the third, central Roombots axis enables the module to rotate its two outer DOF against each other. This novel feature enables a single Roombots module to locomote on flat terrain, but also to climb a wall, or to cross a concave, perpendicular edge. Convex edges require the assembly of at least two modules into a Roombots "Metamodule". Each module has ten available connector slots, currently two of them are equipped with an active connection mechanism based on mechanical latches.
Roombots are designed for two tasks: to eventually shape objects of daily life, e.g. furniture, and to locomote, e.g. as a quadruped or a tripod robot made from multiple modules.
More information can be found at Biorobotics Laboratory Roombots webpage.
here. The rather limited exploration down this avenue is probably a consequence of the historical lack of need in any applications for such an approach.
ic systems or self-reconfigurable modular robots are autonomous kinematic machines with variable morphology
. Beyond conventional actuation, sensing and control typically found in fixed-morphology robots, self-reconfiguring robots are also able to deliberately change their own shape by rearranging the connectivity of their parts, in order to adapt to new circumstances, perform new tasks, or recover from damage.
For example, a robot made of such components could assume a worm
-like shape to move through a narrow pipe, reassemble into something with spider
-like legs to cross uneven terrain, then form a third arbitrary object (like a ball or wheel that can spin itself) to move quickly over a fairly flat terrain; it can also be used for making "fixed" objects, such as walls, shelters, or buildings.
In some cases this involves each module having 2 or more connectors for connecting several together. They can contain electronics
, sensor
s, computer processors, memory
, and power supplies; they can also contain actuator
s that are used for manipulating their location in the environment and in relation with each other. A feature found in some cases is the ability of the modules to automatically connect and disconnect themselves to and from each other, and to form into many objects or perform many tasks moving or manipulating the environment.
By saying "self-reconfiguring" or "self-reconfigurable" it means that the mechanism or device is capable of utilizing its own system of control such as with actuators or stochastic means to change its overall structural shape. Having the quality of being "modular" in "self-reconfiguring modular robotics" is to say that the same module or set of modules can be added to or removed from the system, as opposed to being generically "modularized" in the broader sense. The underlying intent is to have an indefinite number of identical modules, or a finite and relatively small set of identical modules, in a mesh or matrix structure of self-reconfigurable modules.
Self-reconfiguration is also different from the concept of self-replication
, and self-replication is not necessarily a quality that a self-reconfigurable module or collection of such modules can or must possess. A matrix of N-number of modules does not need to be able to increase the quantity of modules to greater than N to be considered self-reconfigurable. It is sufficient for self-reconfigurable modules to be a device that is produced at a conventional factory, where dedicated machines stamp or mold components, and factory workers on an assembly line assemble the components to build each module.
There are two basic types of methods of segment articulation that self-reconfigurable mechanisms can utilize to reshape their structures, chain reconfiguration and lattice reconfiguration.
The modular building blocks usually consist of some primary structural actuated unit, and potentially additional specialized units such as grippers, feet, wheels, cameras, payload and energy storage and generation.
Modular robotic systems can also be classified according to the way by which units are reconfigured (moved) into place.
Modular robotic system are also generally classified depending on the design of the modules.
Other modular robotic systems exist which are not self-reconfigurable, and thus do not formally belong to this family of robots though they may have similar appearance. For example, self-assembling systems may be composed of multiple modules but cannot dynamically control their target shape. Similarly, tensegrity robotics may be composed of multiple interchangeable modules but cannot self-reconfigure.
Both these advantages have not yet been fully realized. A modular robot is likely to be inferior in performance to any single custom robot tailored for a specific task. However, the advantage of modular robotics is only apparent when considering multiple tasks that would normally require a set of different robots.
The added degrees of freedom make modular robots more versatile in their potential capabilities, but also incur a performance tradeoff and increased mechanical and computational complexities.
The quest for self-reconfiguring robotic structures is to some extent inspired by envisioned applications such as long-term space missions, that require long-term self-sustaining robotic ecology that can handle unforeseen situations and may require self repair. A second source of inspiration are biological systems that are self-constructed out of a relatively small repertoire of lower-level building blocks (cells or amino acids, depending on scale of interest). This architecture underlies biological systems’ ability to physically adapt, grow, heal, and even self replicate – capabilities that would be desirable in many engineered systems.
” has been somewhat elusive. Here are several examples:
three-dimensional replicas of people or objects, so lifelike that human senses would accept them as real. This would eliminate the need for cumbersome virtual reality gear and overcome the viewing angle limitations of modern 3D approaches. The replicas would mimic the shape and appearance of a person or object being imaged in real time, and as the originals moved, so would their replicas. One aspect of this application is that the main development thrust is geometric representation rather than applying forces to the environment as in a typical robotic manipulation task.
This project is widely known as claytronics or programmable matter.
One source of inspiration for the development of these systems comes from the application. A second source is biological systems that are self-constructed out of a relatively small repertoire of lower-level building blocks (cells or amino acids, depending on scale of interest). This architecture underlies biological systems’ ability to physically adapt, grow, heal, and even self replicate – capabilities that would be desirable in many engineered systems.
The early 1990s saw further development from Greg Chirikjian, Mark Yim, Joseph Michael, and Satoshi Murata. Chirikjian, Michael, and Murata developed lattice reconfiguration systems and Yim developed a chain based system. While these researchers started with from a mechanical engineering emphasis, designing and building modules then developing code to program them, the work of Daniela Rus and Wei-min Shen developed hardware but had a greater impact on the programming aspects. They started a trend towards provable or verifiable distributed algorithms for the control of large numbers of modules.
One of the more interesting hardware platforms recently has been the MTRAN II and III systems developed by Satoshi Murata et al. This system is a hybrid chain and lattice system. It has the advantage of being able to achieve tasks more easily like chain systems, yet reconfigure like a lattice system.
More recently new efforts in stochastic self-assembly have been pursued by Hod Lipson and Eric Klavins. A large effort at CMU headed by Seth Goldstein and Todd Mowry has started looking at issues in developing millions of modules.
Many tasks have been shown to be achievable, especially with chain reconfiguration modules. This demonstrates the versatility of these systems however, the other two advantages, robustness and low cost have not been demonstrated. In general the prototype systems developed in the labs have been fragile and expensive as would be expected during any initial development.
There is a growing number of research groups actively involved in modular robotics research. To date, about 30 systems have been designed and constructed, some of which are shown below.
A chain/tree hyper-redundant
modular robotic system invented by Charles Khairallah from Robotics Design Inc in Montreal
, Quebec
, Canada
. This robot is designed with ANAT Technology (Articulated Nimble Adaptable Trunk) and is currently used for industrial manipulating under the name ANAT AMI-100. Robotics Design's patented U and H shaped modules, of which this robot is composed, form the other robots in the ANAT robotics family. This robot can re-configure and/or self-reconfigure to form different shapes, due to its LEGO
-like sets of modules with one degree of freedom each. This allows robots to be designed using ANAT modules with n° of freedom. Configurations range from mobile robots (ANATROLLER), manipulators (ANAT AMI-100), to walking robots (ANAT Walker).
PolyBot G3 (2002)
A chain self-reconfiguration system. Each module is about 50 mm on a side, and has 1 rotational DOF. It is part of the PolyBot modular robot family that has demonstrated many modes of locomotion including walking: biped, 14 legged, slinky-like, snake-like: concertina in a gopher hole, inchworm gaits, rectilinear undulation and sidewinding gaits, rolling like a tread at up to 1.4m/s, riding a tricycle, climbing: stairs, poles pipes, ramps etc. More information can be found at the polybot webpage at PARC.
M-TRAN III (2005)
A hybrid type self-reconfigurable system. Each module is two cube size (65 mm side), and has 2 rotational DOF and 6 flat surfaces for connection. It is the 3rd M-TRAN prototypes. Compared with the former (M-TRAN II), speed and reliability of connection is largely improved. As a chain type system, locomotion by CPG (Central Pattern Generator) controller in vaious shapes has been demonstrated by M-TRAN II. As a lattice type system, it can change its configuration, e.g., between a 4 legged walker to a caterpillar like robot. See the M-TRAN webpage at AIST.
AMOEBA-I (2005)
AMOEBA-I, a three-module reconfigurable mobile robot was developed in Shenyang Institute of Automation (SIA), Chinese Academy of Sciences (CAS) by Liu J G et al.http://ieeexplore.ieee.org/xpls/abs_all.jsp?arnumber=1708645http://www.springerlink.com/content/m81820061n48jh32/.AMOEBA-I has nine kinds of non-isomorphic configurations and high mobility under unstructured environments.Four generations of its platform have been developed and a series of researches have been carried out on their reconfiguration mechanism, non-isomorphic configurations, tipover stability, and reconfiguration planning. Experiments have demonstrated that such kind structure permits good mobility and high flexibility to uneven terrain. Being hyper-redundant, modularized and reconfigurable, AMOEBA-I has many possible applications such as Urban Search and Rescue (USAR) and space exploration.
Ref_1: see http://ieeexplore.ieee.org/xpls/abs_all.jsp?arnumber=1708645;
Ref_2: see http://www.springerlink.com/content/m81820061n48jh32/
Stochastic-3D (2005)
High spatial resolution for arbitrary three-dimensional shape formation with modular robots can be accomplished using lattice system with large quantities of very small, prospectively microscopic modules. At small scales, and with large quantities of modules, deterministic control over reconfiguration of individual modules will become unfeasible, while stochastic mechanisms will naturally prevail. Microscopic size of modules will make the use of electromagnetic actuation and interconnection prohibitive, as well, as the use of on-board power storage.
Three large scale prototypes were built in attempt to demonstrate dynamically programmable three-dimensional stochastic reconfiguration in a neutral-buoyancy environment. The first prototype used electromagnets for module reconfiguration and interconnection. The modules were 100 mm cubes and weighed 0.81 kg. The second prototype used stochastic fluidic reconfiguration and interconnection mechanism. Its 130 mm cubic modules weighed 1.78 kg each and made reconfiguration experiments excessively slow. The current third implementation inherits the fluidic reconfiguration principle. The lattice grid size is 80 mm, and the reconfiguration experiments are under way. More information can be found at the CCSL Stochastic Modular Robotics webpage.
Molecubes (2005)
This chain self-reconfiguring system was built by the Cornell Computational Synthesis Lab to physically demonstrate artificial kinematic self-reproduction. Each module is a 0.65 kg cube with 100 mm long edges and one rotational degree of freedom. The axis of rotation is aligned with the cube's longest diagonal. Physical self-reproduction of a three- and a four-module robots was demonstrated. It was also shown that, disregarding the gravity constraints, an infinite number of self-reproducing chain meta-structures can be built from Molecubes. More information can be found at the CCSL Self-Replication webpage.
The Programmable Parts (2005)
The programmable parts are stirred randomly on an air-hockey table by randomly actuated air jets. When they collide and stick, they can communicate and decide whether to stay stuck, or if and when to detach. Local interaction rules can be devised and optimized to guide the robots to make any desired global shape. More information can be found at the programmable parts web page.
SuperBot (2006)
The SuperBot modules fall into the chain/tree architecture. The modules have three degrees of freedom each. The design is based on two previous systems: Conro (by the same research group) and MTRAN (by Murata et al.). Each module can connect to another module through one of its six dock connectors. They can communicate and share power through their dock connectors. Several locomotion gaits have been developed for different arrangements of modules. For high-level communication the modules use hormone-based control, a distributed, scalable protocol that does not require the modules to have unique ID's.
Miche (2006)
The Miche system is a modular lattice system capable of arbitrary shape formation. Each module is an autonomous robot module capable of connecting to and communicating with its immediate neighbors. When assembled into a structure, the modules form a system that can be virtually sculpted using a computer interface and a distributed process. The group of modules collectively decide who is on the final shape and who is not using algorithms that minimize the information transmission and storage. Finally, the modules not in the structure let go and fall off under the control of an external force, in this case gravity.
More details at Miche (Rus et al.).
Roombots (2009)
Roombots have a hybrid chain/tree architecture. Each module has three degree of freedom, two of them using the diametrical axis within a regular cube, and a third (center) axis of rotation connecting the two spherical parts. All three axes are continuously rotatory. The outer Roombots DOF is using the same axis-orientation as Molecubes, the third, central Roombots axis enables the module to rotate its two outer DOF against each other. This novel feature enables a single Roombots module to locomote on flat terrain, but also to climb a wall, or to cross a concave, perpendicular edge. Convex edges require the assembly of at least two modules into a Roombots "Metamodule". Each module has ten available connector slots, currently two of them are equipped with an active connection mechanism based on mechanical latches.
Roombots are designed for two tasks: to eventually shape objects of daily life, e.g. furniture, and to locomote, e.g. as a quadruped or a tripod robot made from multiple modules.
More information can be found at Biorobotics Laboratory Roombots webpage.
here. The rather limited exploration down this avenue is probably a consequence of the historical lack of need in any applications for such an approach.
ic systems or self-reconfigurable modular robots are autonomous kinematic machines with variable morphology
. Beyond conventional actuation, sensing and control typically found in fixed-morphology robots, self-reconfiguring robots are also able to deliberately change their own shape by rearranging the connectivity of their parts, in order to adapt to new circumstances, perform new tasks, or recover from damage.
For example, a robot made of such components could assume a worm
-like shape to move through a narrow pipe, reassemble into something with spider
-like legs to cross uneven terrain, then form a third arbitrary object (like a ball or wheel that can spin itself) to move quickly over a fairly flat terrain; it can also be used for making "fixed" objects, such as walls, shelters, or buildings.
In some cases this involves each module having 2 or more connectors for connecting several together. They can contain electronics
, sensor
s, computer processors, memory
, and power supplies; they can also contain actuator
s that are used for manipulating their location in the environment and in relation with each other. A feature found in some cases is the ability of the modules to automatically connect and disconnect themselves to and from each other, and to form into many objects or perform many tasks moving or manipulating the environment.
By saying "self-reconfiguring" or "self-reconfigurable" it means that the mechanism or device is capable of utilizing its own system of control such as with actuators or stochastic means to change its overall structural shape. Having the quality of being "modular" in "self-reconfiguring modular robotics" is to say that the same module or set of modules can be added to or removed from the system, as opposed to being generically "modularized" in the broader sense. The underlying intent is to have an indefinite number of identical modules, or a finite and relatively small set of identical modules, in a mesh or matrix structure of self-reconfigurable modules.
Self-reconfiguration is also different from the concept of self-replication
, and self-replication is not necessarily a quality that a self-reconfigurable module or collection of such modules can or must possess. A matrix of N-number of modules does not need to be able to increase the quantity of modules to greater than N to be considered self-reconfigurable. It is sufficient for self-reconfigurable modules to be a device that is produced at a conventional factory, where dedicated machines stamp or mold components, and factory workers on an assembly line assemble the components to build each module.
There are two basic types of methods of segment articulation that self-reconfigurable mechanisms can utilize to reshape their structures, chain reconfiguration and lattice reconfiguration.
The modular building blocks usually consist of some primary structural actuated unit, and potentially additional specialized units such as grippers, feet, wheels, cameras, payload and energy storage and generation.
Modular robotic systems can also be classified according to the way by which units are reconfigured (moved) into place.
Modular robotic system are also generally classified depending on the design of the modules.
Other modular robotic systems exist which are not self-reconfigurable, and thus do not formally belong to this family of robots though they may have similar appearance. For example, self-assembling systems may be composed of multiple modules but cannot dynamically control their target shape. Similarly, tensegrity robotics may be composed of multiple interchangeable modules but cannot self-reconfigure.
Both these advantages have not yet been fully realized. A modular robot is likely to be inferior in performance to any single custom robot tailored for a specific task. However, the advantage of modular robotics is only apparent when considering multiple tasks that would normally require a set of different robots.
The added degrees of freedom make modular robots more versatile in their potential capabilities, but also incur a performance tradeoff and increased mechanical and computational complexities.
The quest for self-reconfiguring robotic structures is to some extent inspired by envisioned applications such as long-term space missions, that require long-term self-sustaining robotic ecology that can handle unforeseen situations and may require self repair. A second source of inspiration are biological systems that are self-constructed out of a relatively small repertoire of lower-level building blocks (cells or amino acids, depending on scale of interest). This architecture underlies biological systems’ ability to physically adapt, grow, heal, and even self replicate – capabilities that would be desirable in many engineered systems.
” has been somewhat elusive. Here are several examples:
three-dimensional replicas of people or objects, so lifelike that human senses would accept them as real. This would eliminate the need for cumbersome virtual reality gear and overcome the viewing angle limitations of modern 3D approaches. The replicas would mimic the shape and appearance of a person or object being imaged in real time, and as the originals moved, so would their replicas. One aspect of this application is that the main development thrust is geometric representation rather than applying forces to the environment as in a typical robotic manipulation task.
This project is widely known as claytronics or programmable matter.
One source of inspiration for the development of these systems comes from the application. A second source is biological systems that are self-constructed out of a relatively small repertoire of lower-level building blocks (cells or amino acids, depending on scale of interest). This architecture underlies biological systems’ ability to physically adapt, grow, heal, and even self replicate – capabilities that would be desirable in many engineered systems.
The early 1990s saw further development from Greg Chirikjian, Mark Yim, Joseph Michael, and Satoshi Murata. Chirikjian, Michael, and Murata developed lattice reconfiguration systems and Yim developed a chain based system. While these researchers started with from a mechanical engineering emphasis, designing and building modules then developing code to program them, the work of Daniela Rus and Wei-min Shen developed hardware but had a greater impact on the programming aspects. They started a trend towards provable or verifiable distributed algorithms for the control of large numbers of modules.
One of the more interesting hardware platforms recently has been the MTRAN II and III systems developed by Satoshi Murata et al. This system is a hybrid chain and lattice system. It has the advantage of being able to achieve tasks more easily like chain systems, yet reconfigure like a lattice system.
More recently new efforts in stochastic self-assembly have been pursued by Hod Lipson and Eric Klavins. A large effort at CMU headed by Seth Goldstein and Todd Mowry has started looking at issues in developing millions of modules.
Many tasks have been shown to be achievable, especially with chain reconfiguration modules. This demonstrates the versatility of these systems however, the other two advantages, robustness and low cost have not been demonstrated. In general the prototype systems developed in the labs have been fragile and expensive as would be expected during any initial development.
There is a growing number of research groups actively involved in modular robotics research. To date, about 30 systems have been designed and constructed, some of which are shown below.
A chain/tree hyper-redundant
modular robotic system invented by Charles Khairallah from Robotics Design Inc in Montreal
, Quebec
, Canada
. This robot is designed with ANAT Technology (Articulated Nimble Adaptable Trunk) and is currently used for industrial manipulating under the name ANAT AMI-100. Robotics Design's patented U and H shaped modules, of which this robot is composed, form the other robots in the ANAT robotics family. This robot can re-configure and/or self-reconfigure to form different shapes, due to its LEGO
-like sets of modules with one degree of freedom each. This allows robots to be designed using ANAT modules with n° of freedom. Configurations range from mobile robots (ANATROLLER), manipulators (ANAT AMI-100), to walking robots (ANAT Walker).
PolyBot G3 (2002)
A chain self-reconfiguration system. Each module is about 50 mm on a side, and has 1 rotational DOF. It is part of the PolyBot modular robot family that has demonstrated many modes of locomotion including walking: biped, 14 legged, slinky-like, snake-like: concertina in a gopher hole, inchworm gaits, rectilinear undulation and sidewinding gaits, rolling like a tread at up to 1.4m/s, riding a tricycle, climbing: stairs, poles pipes, ramps etc. More information can be found at the polybot webpage at PARC.
M-TRAN III (2005)
A hybrid type self-reconfigurable system. Each module is two cube size (65 mm side), and has 2 rotational DOF and 6 flat surfaces for connection. It is the 3rd M-TRAN prototypes. Compared with the former (M-TRAN II), speed and reliability of connection is largely improved. As a chain type system, locomotion by CPG (Central Pattern Generator) controller in vaious shapes has been demonstrated by M-TRAN II. As a lattice type system, it can change its configuration, e.g., between a 4 legged walker to a caterpillar like robot. See the M-TRAN webpage at AIST.
AMOEBA-I (2005)
AMOEBA-I, a three-module reconfigurable mobile robot was developed in Shenyang Institute of Automation (SIA), Chinese Academy of Sciences (CAS) by Liu J G et al.http://ieeexplore.ieee.org/xpls/abs_all.jsp?arnumber=1708645http://www.springerlink.com/content/m81820061n48jh32/.AMOEBA-I has nine kinds of non-isomorphic configurations and high mobility under unstructured environments.Four generations of its platform have been developed and a series of researches have been carried out on their reconfiguration mechanism, non-isomorphic configurations, tipover stability, and reconfiguration planning. Experiments have demonstrated that such kind structure permits good mobility and high flexibility to uneven terrain. Being hyper-redundant, modularized and reconfigurable, AMOEBA-I has many possible applications such as Urban Search and Rescue (USAR) and space exploration.
Ref_1: see http://ieeexplore.ieee.org/xpls/abs_all.jsp?arnumber=1708645;
Ref_2: see http://www.springerlink.com/content/m81820061n48jh32/
Stochastic-3D (2005)
High spatial resolution for arbitrary three-dimensional shape formation with modular robots can be accomplished using lattice system with large quantities of very small, prospectively microscopic modules. At small scales, and with large quantities of modules, deterministic control over reconfiguration of individual modules will become unfeasible, while stochastic mechanisms will naturally prevail. Microscopic size of modules will make the use of electromagnetic actuation and interconnection prohibitive, as well, as the use of on-board power storage.
Three large scale prototypes were built in attempt to demonstrate dynamically programmable three-dimensional stochastic reconfiguration in a neutral-buoyancy environment. The first prototype used electromagnets for module reconfiguration and interconnection. The modules were 100 mm cubes and weighed 0.81 kg. The second prototype used stochastic fluidic reconfiguration and interconnection mechanism. Its 130 mm cubic modules weighed 1.78 kg each and made reconfiguration experiments excessively slow. The current third implementation inherits the fluidic reconfiguration principle. The lattice grid size is 80 mm, and the reconfiguration experiments are under way. More information can be found at the CCSL Stochastic Modular Robotics webpage.
Molecubes (2005)
This chain self-reconfiguring system was built by the Cornell Computational Synthesis Lab to physically demonstrate artificial kinematic self-reproduction. Each module is a 0.65 kg cube with 100 mm long edges and one rotational degree of freedom. The axis of rotation is aligned with the cube's longest diagonal. Physical self-reproduction of a three- and a four-module robots was demonstrated. It was also shown that, disregarding the gravity constraints, an infinite number of self-reproducing chain meta-structures can be built from Molecubes. More information can be found at the CCSL Self-Replication webpage.
The Programmable Parts (2005)
The programmable parts are stirred randomly on an air-hockey table by randomly actuated air jets. When they collide and stick, they can communicate and decide whether to stay stuck, or if and when to detach. Local interaction rules can be devised and optimized to guide the robots to make any desired global shape. More information can be found at the programmable parts web page.
SuperBot (2006)
The SuperBot modules fall into the chain/tree architecture. The modules have three degrees of freedom each. The design is based on two previous systems: Conro (by the same research group) and MTRAN (by Murata et al.). Each module can connect to another module through one of its six dock connectors. They can communicate and share power through their dock connectors. Several locomotion gaits have been developed for different arrangements of modules. For high-level communication the modules use hormone-based control, a distributed, scalable protocol that does not require the modules to have unique ID's.
Miche (2006)
The Miche system is a modular lattice system capable of arbitrary shape formation. Each module is an autonomous robot module capable of connecting to and communicating with its immediate neighbors. When assembled into a structure, the modules form a system that can be virtually sculpted using a computer interface and a distributed process. The group of modules collectively decide who is on the final shape and who is not using algorithms that minimize the information transmission and storage. Finally, the modules not in the structure let go and fall off under the control of an external force, in this case gravity.
More details at Miche (Rus et al.).
Roombots (2009)
Roombots have a hybrid chain/tree architecture. Each module has three degree of freedom, two of them using the diametrical axis within a regular cube, and a third (center) axis of rotation connecting the two spherical parts. All three axes are continuously rotatory. The outer Roombots DOF is using the same axis-orientation as Molecubes, the third, central Roombots axis enables the module to rotate its two outer DOF against each other. This novel feature enables a single Roombots module to locomote on flat terrain, but also to climb a wall, or to cross a concave, perpendicular edge. Convex edges require the assembly of at least two modules into a Roombots "Metamodule". Each module has ten available connector slots, currently two of them are equipped with an active connection mechanism based on mechanical latches.
Roombots are designed for two tasks: to eventually shape objects of daily life, e.g. furniture, and to locomote, e.g. as a quadruped or a tripod robot made from multiple modules.
More information can be found at Biorobotics Laboratory Roombots webpage.
here. The rather limited exploration down this avenue is probably a consequence of the historical lack of need in any applications for such an approach.
Robot
A robot is a mechanical or virtual intelligent agent that can perform tasks automatically or with guidance, typically by remote control. In practice a robot is usually an electro-mechanical machine that is guided by computer and electronic programming. Robots can be autonomous, semi-autonomous or...
ic systems or self-reconfigurable modular robots are autonomous kinematic machines with variable morphology
Morphology
Morphology may mean:*Morphology , the study of the structure and content of word forms*Morphology , the study of the form or shape of an organism or part thereof...
. Beyond conventional actuation, sensing and control typically found in fixed-morphology robots, self-reconfiguring robots are also able to deliberately change their own shape by rearranging the connectivity of their parts, in order to adapt to new circumstances, perform new tasks, or recover from damage.
For example, a robot made of such components could assume a worm
Worm
The term worm refers to an obsolete taxon used by Carolus Linnaeus and Jean-Baptiste Lamarck for all non-arthropod invertebrate animals, and stems from the Old English word wyrm. Currently it is used to describe many different distantly-related animals that typically have a long cylindrical...
-like shape to move through a narrow pipe, reassemble into something with spider
Spider
Spiders are air-breathing arthropods that have eight legs, and chelicerae with fangs that inject venom. They are the largest order of arachnids and rank seventh in total species diversity among all other groups of organisms...
-like legs to cross uneven terrain, then form a third arbitrary object (like a ball or wheel that can spin itself) to move quickly over a fairly flat terrain; it can also be used for making "fixed" objects, such as walls, shelters, or buildings.
In some cases this involves each module having 2 or more connectors for connecting several together. They can contain electronics
Electronics
Electronics is the branch of science, engineering and technology that deals with electrical circuits involving active electrical components such as vacuum tubes, transistors, diodes and integrated circuits, and associated passive interconnection technologies...
, sensor
Sensor
A sensor is a device that measures a physical quantity and converts it into a signal which can be read by an observer or by an instrument. For example, a mercury-in-glass thermometer converts the measured temperature into expansion and contraction of a liquid which can be read on a calibrated...
s, computer processors, memory
Memory
In psychology, memory is an organism's ability to store, retain, and recall information and experiences. Traditional studies of memory began in the fields of philosophy, including techniques of artificially enhancing memory....
, and power supplies; they can also contain actuator
Actuator
An actuator is a type of motor for moving or controlling a mechanism or system. It is operated by a source of energy, usually in the form of an electric current, hydraulic fluid pressure or pneumatic pressure, and converts that energy into some kind of motion. An actuator is the mechanism by which...
s that are used for manipulating their location in the environment and in relation with each other. A feature found in some cases is the ability of the modules to automatically connect and disconnect themselves to and from each other, and to form into many objects or perform many tasks moving or manipulating the environment.
By saying "self-reconfiguring" or "self-reconfigurable" it means that the mechanism or device is capable of utilizing its own system of control such as with actuators or stochastic means to change its overall structural shape. Having the quality of being "modular" in "self-reconfiguring modular robotics" is to say that the same module or set of modules can be added to or removed from the system, as opposed to being generically "modularized" in the broader sense. The underlying intent is to have an indefinite number of identical modules, or a finite and relatively small set of identical modules, in a mesh or matrix structure of self-reconfigurable modules.
Self-reconfiguration is also different from the concept of self-replication
Self-replication
Self-replication is any behavior of a dynamical system that yields construction of an identical copy of that dynamical system. Biological cells, given suitable environments, reproduce by cell division. During cell division, DNA is replicated and can be transmitted to offspring during reproduction...
, and self-replication is not necessarily a quality that a self-reconfigurable module or collection of such modules can or must possess. A matrix of N-number of modules does not need to be able to increase the quantity of modules to greater than N to be considered self-reconfigurable. It is sufficient for self-reconfigurable modules to be a device that is produced at a conventional factory, where dedicated machines stamp or mold components, and factory workers on an assembly line assemble the components to build each module.
There are two basic types of methods of segment articulation that self-reconfigurable mechanisms can utilize to reshape their structures, chain reconfiguration and lattice reconfiguration.
Structure and control
Modular robots are usually composed of multiple building blocks of a relatively small repertoire, with uniform docking interfaces that allow transfer of mechanical forces and moments, electrical power and communication throughout the robot.The modular building blocks usually consist of some primary structural actuated unit, and potentially additional specialized units such as grippers, feet, wheels, cameras, payload and energy storage and generation.
A taxonomy of architectures
Modular self-reconfiguring robotic systems can be generally classified into several architectural groups by the geometric arrangement of their unit (lattice vs. chain). Several systems exhibit hybrid properties.- Lattice architectures have units that are arranged and connected in some regular, space-filling three-dimensional pattern, such as a cubical or hexagonal grid. Control and motion are executed in parallel. Lattice architectures usually offer simpler computational representation that can be more easily scaled to complex systems.
- Chain/tree architectures have units that are connected together in a string or tree topology. This chain or tree can fold up to become space filling, but underlying architecture is serial. Chain architectures can reach any point in space, and are therefore more versatile but more computationally difficult to represent and analyze. Tree architectures may resemble a bush robotBush robotBush robots, as envisioned by Hans Moravec, are the ultimate in dexterity and reconfigurability. They earn their nickname from their appearance: bush robots repeatedly branch in a fractal way into trillions of nanoscale fingers...
Modular robotic systems can also be classified according to the way by which units are reconfigured (moved) into place.
- Deterministic reconfiguration relies on units moving or being directly manipulated into their target location during reconfiguration. The exact location of each unit is known at all times. Reconfiguration times can be guaranteed, but sophisticated feedback control is necessary to assure precise manipulation. Macro-scale systems are usually deterministic.
- Stochastic reconfiguration relies on units moving around using statistical processes (like Brownian motion). The exact location of each unit only known when it is connected to the main structure, but it may take unknown paths to move between locations. Reconfiguration times can be guaranteed only statistically. Stochastic architectures are more favorable at micro scales.
Modular robotic system are also generally classified depending on the design of the modules.
- Homogeneous modular robot system has many same modules coming together to form a structure suitable to perform the required task. Its advantage over other systems is that there are easy to replicate, as there a is only a singular design. their disadvantage being their functionality get leimited depending on the modules design.
- Heterogeneous modular robot system has different modules which do specialized function coming together to form a structure suitable to perform the task. Its advantage beings depending on the requirement of task the modular robot could get new modules to enhance its capabilities.The disadvantage being it becomes a more complex design.
- Hybrid modular robot system has multiple modules of same functions and also of different functions coming together to form a structure suitable to perform the task. Its advantage is it combines the features of its predecessors.
Other modular robotic systems exist which are not self-reconfigurable, and thus do not formally belong to this family of robots though they may have similar appearance. For example, self-assembling systems may be composed of multiple modules but cannot dynamically control their target shape. Similarly, tensegrity robotics may be composed of multiple interchangeable modules but cannot self-reconfigure.
Motivation and inspiration
There are two key motivations for designing modular self-reconfiguring robotic systems.- Functional advantage: Self reconfiguring robotic systems are potentially more robust and more adaptive than conventional systems. The reconfiguration ability allows a robot or a group of robots to disassemble and reassemble machines to form new morphologies that are better suitable for new tasks, such as changing from a legged robot to a snake robot and then to a rolling robot. Since robot parts are interchangeable (within a robot and between different robots), machines can also replace faulty parts autonomously, leading to self-repair.
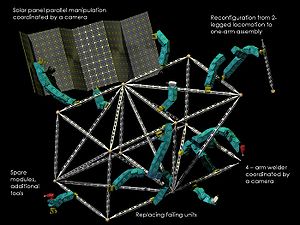
- Economic advantage: Self reconfiguring robotic systems can potentially lower overall robot cost by making a range of complex machines out of a single (or relatively few) types of mass-produced modules.
Both these advantages have not yet been fully realized. A modular robot is likely to be inferior in performance to any single custom robot tailored for a specific task. However, the advantage of modular robotics is only apparent when considering multiple tasks that would normally require a set of different robots.
The added degrees of freedom make modular robots more versatile in their potential capabilities, but also incur a performance tradeoff and increased mechanical and computational complexities.
The quest for self-reconfiguring robotic structures is to some extent inspired by envisioned applications such as long-term space missions, that require long-term self-sustaining robotic ecology that can handle unforeseen situations and may require self repair. A second source of inspiration are biological systems that are self-constructed out of a relatively small repertoire of lower-level building blocks (cells or amino acids, depending on scale of interest). This architecture underlies biological systems’ ability to physically adapt, grow, heal, and even self replicate – capabilities that would be desirable in many engineered systems.
Application areas
Given these advantages, where would a modular self-reconfigurable system be used? While the system has the promise of being capable of doing a wide variety of things, finding the “killer applicationKiller application
A killer application , in the jargon of marketing teams, has been used to refer to any computer program that is so necessary or desirable that it proves the core value of some larger technology, such as computer hardware, gaming console, software, or an operating system...
” has been somewhat elusive. Here are several examples:
Space exploration
One application that highlights the advantages of self-reconfigurable systems is long-term space missions. These require long-term self-sustaining robotic ecology that can handle unforeseen situations and may require self repair. Self-reconfigurable systems have the ability to handle tasks that are not known a priori especially compared to fixed configuration systems. In addition, space missions are highly volume and mass constrained. Sending a robot system that can reconfigure to achieve many tasks is better than sending many robots that each can do one task.Telepario
Another example of an application has been coined “telepario” by CMU professors Todd Mowry and Seth Goldstein. What the researchers propose to make are moving, physical,three-dimensional replicas of people or objects, so lifelike that human senses would accept them as real. This would eliminate the need for cumbersome virtual reality gear and overcome the viewing angle limitations of modern 3D approaches. The replicas would mimic the shape and appearance of a person or object being imaged in real time, and as the originals moved, so would their replicas. One aspect of this application is that the main development thrust is geometric representation rather than applying forces to the environment as in a typical robotic manipulation task.
This project is widely known as claytronics or programmable matter.
Bucket of stuff
A third long term vision for these systems has been called “bucket of stuff”. In this vision, consumers of the future have a container of self-reconfigurable modules say in their garage, basement, or attic. When the need arises, the consumer calls forth the robots to achieve a task such as “clean the gutters” or “change the oil in the car” and the robot assumes the shape needed and does the task.One source of inspiration for the development of these systems comes from the application. A second source is biological systems that are self-constructed out of a relatively small repertoire of lower-level building blocks (cells or amino acids, depending on scale of interest). This architecture underlies biological systems’ ability to physically adapt, grow, heal, and even self replicate – capabilities that would be desirable in many engineered systems.
History and state of the art
The roots of the concept of modular self-reconfigurable robots can be traced back to the “quick change” end effector and automatic tool changers in computer numerical controlled machining centers in the 1970s. Here, special modules each with a common connection mechanism could be automatically swapped out on the end of a robotic arm. However, taking the basic concept of the common connection mechanism and applying it to the whole robot was introduced by Toshio Fukuda with the CEBOT (short for cellular robot) in the late 1980s.The early 1990s saw further development from Greg Chirikjian, Mark Yim, Joseph Michael, and Satoshi Murata. Chirikjian, Michael, and Murata developed lattice reconfiguration systems and Yim developed a chain based system. While these researchers started with from a mechanical engineering emphasis, designing and building modules then developing code to program them, the work of Daniela Rus and Wei-min Shen developed hardware but had a greater impact on the programming aspects. They started a trend towards provable or verifiable distributed algorithms for the control of large numbers of modules.
One of the more interesting hardware platforms recently has been the MTRAN II and III systems developed by Satoshi Murata et al. This system is a hybrid chain and lattice system. It has the advantage of being able to achieve tasks more easily like chain systems, yet reconfigure like a lattice system.
More recently new efforts in stochastic self-assembly have been pursued by Hod Lipson and Eric Klavins. A large effort at CMU headed by Seth Goldstein and Todd Mowry has started looking at issues in developing millions of modules.
Many tasks have been shown to be achievable, especially with chain reconfiguration modules. This demonstrates the versatility of these systems however, the other two advantages, robustness and low cost have not been demonstrated. In general the prototype systems developed in the labs have been fragile and expensive as would be expected during any initial development.
There is a growing number of research groups actively involved in modular robotics research. To date, about 30 systems have been designed and constructed, some of which are shown below.
System | Class, DOF | Author | Year |
---|---|---|---|
CEBOT | Mobile | Fukuda et al. (Tsukuba) | 1988 |
Polypod | chain, 2, 3D | Yim (Stanford) | 1993 |
Metamorphic | lattice, 6, 2D | Chirikjian (Caltech) | 1993 |
Fracta | lattice, 3 2D | Murata (MEL) | 1994 |
Fractal Robots | lattice, 3D | Michael(UK) | 1995 |
Tetrobot | chain, 1 3D | Hamline et al. (RPI) | 1996 |
ANAT Robot | Chain/tree, 8D | Charles Khairallah (CA) | 1997 |
3D Fracta | lattice, 6 3D | Murata et al. (MEL) | 1998 |
Molecule | lattice, 4 3D | Kotay & Rus (Dartmouth) | 1998 |
CONRO | chain, 2 3D | Will & Shen (USC/ISI) | 1998 |
PolyBot | chain, 1 3D | Yim et al. (PARC) | 1998 |
TeleCube | lattice, 6 3D | Suh et al., (PARC) | 1998 |
Vertical | lattice, 2D | Hosakawa et al., (Riken) | 1998 |
Crystalline | lattice, 4 2D | Vona & Rus, (Dartmouth) | 1999 |
I-Cube | lattice, 3D | Unsal, (CMU) | 1999 |
M-TRAN I | hybrid, 2 3D | Murata et al.(AIST) | 1999 |
Pneumatic | lattice, 2D | Inou et al., (TiTech) | 2002 |
Uni Rover | mobile, 2 2D | Hirose et al., (TiTech) | 2002 |
M-TRAN II | hybrid, 2 3D | Murata et al., (AIST) | 2002 |
Atron | lattice, 1 3D | Stoy et al., (U.S Denmark) | 2003 |
S-bot S-bot mobile robot The s-bot is a small differential wheeled mobile robot developed at the LIS at the EPFL in Lausanne, Switzerland between 2001 and 2004. Targeted to swarm robotics, a field of artificial intelligence, it was developed within the Swarm-bots project, a Future and Emerging Technologies project... |
mobile, 3 2D | Mondada Francesco Mondada Francesco Mondada is a Swiss researcher in artificial intelligence and robotics. He is one of the creators of the Khepera, the S-bot and the e-puck mobile robots. He got a Master's degree in Microengineering at the EPFL in 1991 and a Ph.D. degree in 1997.He was the director of from its creation... et al., (EPFL) |
2003 |
Stochastic | lattice, 0 3D | White, Kopanski, Lipson (Cornell) | 2004 |
Superbot | hybrid, 3 3D | Shen et al., (USC/ISI) | 2004 |
Y1 Modules | Chain, 1 3D | Gonzalez-Gomez et al., (UAM) | 2004 |
M-TRAN III | hybrid, 2 3D | Kurokawa et al., (AIST) | 2005 |
AMOEBA-I | Mobile, 7 3D | Liu JG et al., (SIA) | 2005 |
Catom | lattice, 0 2D | Goldstein et al., (CMU) | 2005 |
Stochastic-3D | lattice, 0 3D | White, Zykov, Lipson (Cornell) | 2005 |
Molecubes | chain, 1 3D | Zykov, Mytilinaios, Lipson (Cornell) | 2005 |
Prog. parts | lattice, 0 2D | Klavins, (U. Washington) | 2005 |
Miche | lattice, 0 3D | Rus et al., (MIT) | 2006 |
GZ-I Modules | Chain, 1 3D | Zhang & Gonzalez-Gomez (U. Hamburg, UAM) | 2006 |
Evolve | Chain, 2 3D | Chang Fanxi, Francis (NUS) | 2008 |
Odin | Hybrid, 3 3D | Lyder et al., Modular Robotics Research Lab, (USD) | 2008 |
Roombots | Hybrid, 3 3D | Sproewitz, Moeckel, Ijspeert, Biorobotics Laboratory, (EPFL) | 2009 |
Some current systems
ANAT Robot (1997)A chain/tree hyper-redundant
Redundancy (engineering)
In engineering, redundancy is the duplication of critical components or functions of a system with the intention of increasing reliability of the system, usually in the case of a backup or fail-safe....
modular robotic system invented by Charles Khairallah from Robotics Design Inc in Montreal
Montreal
Montreal is a city in Canada. It is the largest city in the province of Quebec, the second-largest city in Canada and the seventh largest in North America...
, Quebec
Quebec
Quebec or is a province in east-central Canada. It is the only Canadian province with a predominantly French-speaking population and the only one whose sole official language is French at the provincial level....
, Canada
Canada
Canada is a North American country consisting of ten provinces and three territories. Located in the northern part of the continent, it extends from the Atlantic Ocean in the east to the Pacific Ocean in the west, and northward into the Arctic Ocean...
. This robot is designed with ANAT Technology (Articulated Nimble Adaptable Trunk) and is currently used for industrial manipulating under the name ANAT AMI-100. Robotics Design's patented U and H shaped modules, of which this robot is composed, form the other robots in the ANAT robotics family. This robot can re-configure and/or self-reconfigure to form different shapes, due to its LEGO
Lego
Lego is a line of construction toys manufactured by the Lego Group, a privately held company based in Billund, Denmark. The company's flagship product, Lego, consists of colorful interlocking plastic bricks and an accompanying array of gears, minifigures and various other parts...
-like sets of modules with one degree of freedom each. This allows robots to be designed using ANAT modules with n° of freedom. Configurations range from mobile robots (ANATROLLER), manipulators (ANAT AMI-100), to walking robots (ANAT Walker).
PolyBot G3 (2002)
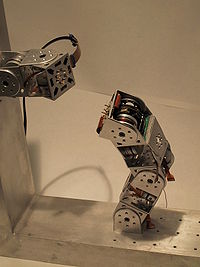
M-TRAN III (2005)
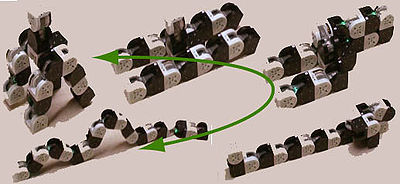
AMOEBA-I (2005)
AMOEBA-I, a three-module reconfigurable mobile robot was developed in Shenyang Institute of Automation (SIA), Chinese Academy of Sciences (CAS) by Liu J G et al.http://ieeexplore.ieee.org/xpls/abs_all.jsp?arnumber=1708645http://www.springerlink.com/content/m81820061n48jh32/.AMOEBA-I has nine kinds of non-isomorphic configurations and high mobility under unstructured environments.Four generations of its platform have been developed and a series of researches have been carried out on their reconfiguration mechanism, non-isomorphic configurations, tipover stability, and reconfiguration planning. Experiments have demonstrated that such kind structure permits good mobility and high flexibility to uneven terrain. Being hyper-redundant, modularized and reconfigurable, AMOEBA-I has many possible applications such as Urban Search and Rescue (USAR) and space exploration.
Ref_1: see http://ieeexplore.ieee.org/xpls/abs_all.jsp?arnumber=1708645;
Ref_2: see http://www.springerlink.com/content/m81820061n48jh32/
Stochastic-3D (2005)
High spatial resolution for arbitrary three-dimensional shape formation with modular robots can be accomplished using lattice system with large quantities of very small, prospectively microscopic modules. At small scales, and with large quantities of modules, deterministic control over reconfiguration of individual modules will become unfeasible, while stochastic mechanisms will naturally prevail. Microscopic size of modules will make the use of electromagnetic actuation and interconnection prohibitive, as well, as the use of on-board power storage.
Three large scale prototypes were built in attempt to demonstrate dynamically programmable three-dimensional stochastic reconfiguration in a neutral-buoyancy environment. The first prototype used electromagnets for module reconfiguration and interconnection. The modules were 100 mm cubes and weighed 0.81 kg. The second prototype used stochastic fluidic reconfiguration and interconnection mechanism. Its 130 mm cubic modules weighed 1.78 kg each and made reconfiguration experiments excessively slow. The current third implementation inherits the fluidic reconfiguration principle. The lattice grid size is 80 mm, and the reconfiguration experiments are under way. More information can be found at the CCSL Stochastic Modular Robotics webpage.
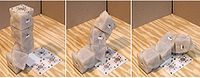
This chain self-reconfiguring system was built by the Cornell Computational Synthesis Lab to physically demonstrate artificial kinematic self-reproduction. Each module is a 0.65 kg cube with 100 mm long edges and one rotational degree of freedom. The axis of rotation is aligned with the cube's longest diagonal. Physical self-reproduction of a three- and a four-module robots was demonstrated. It was also shown that, disregarding the gravity constraints, an infinite number of self-reproducing chain meta-structures can be built from Molecubes. More information can be found at the CCSL Self-Replication webpage.
The Programmable Parts (2005)
The programmable parts are stirred randomly on an air-hockey table by randomly actuated air jets. When they collide and stick, they can communicate and decide whether to stay stuck, or if and when to detach. Local interaction rules can be devised and optimized to guide the robots to make any desired global shape. More information can be found at the programmable parts web page.
SuperBot (2006)
The SuperBot modules fall into the chain/tree architecture. The modules have three degrees of freedom each. The design is based on two previous systems: Conro (by the same research group) and MTRAN (by Murata et al.). Each module can connect to another module through one of its six dock connectors. They can communicate and share power through their dock connectors. Several locomotion gaits have been developed for different arrangements of modules. For high-level communication the modules use hormone-based control, a distributed, scalable protocol that does not require the modules to have unique ID's.
Miche (2006)
The Miche system is a modular lattice system capable of arbitrary shape formation. Each module is an autonomous robot module capable of connecting to and communicating with its immediate neighbors. When assembled into a structure, the modules form a system that can be virtually sculpted using a computer interface and a distributed process. The group of modules collectively decide who is on the final shape and who is not using algorithms that minimize the information transmission and storage. Finally, the modules not in the structure let go and fall off under the control of an external force, in this case gravity.
More details at Miche (Rus et al.).
Roombots (2009)
Roombots have a hybrid chain/tree architecture. Each module has three degree of freedom, two of them using the diametrical axis within a regular cube, and a third (center) axis of rotation connecting the two spherical parts. All three axes are continuously rotatory. The outer Roombots DOF is using the same axis-orientation as Molecubes, the third, central Roombots axis enables the module to rotate its two outer DOF against each other. This novel feature enables a single Roombots module to locomote on flat terrain, but also to climb a wall, or to cross a concave, perpendicular edge. Convex edges require the assembly of at least two modules into a Roombots "Metamodule". Each module has ten available connector slots, currently two of them are equipped with an active connection mechanism based on mechanical latches.
Roombots are designed for two tasks: to eventually shape objects of daily life, e.g. furniture, and to locomote, e.g. as a quadruped or a tripod robot made from multiple modules.
More information can be found at Biorobotics Laboratory Roombots webpage.
Quantitative accomplishment
- The robot with most active modules has 56 units
- The smallest actuated modular unit has a size of
mm - The largest actuated modular unit (by volume) has the size of 8 m^3 <(GHFC)giant helium filled catoms, CMU>
- The strongest actuation modules are able to lift 5 identical horizontally cantilevered units.
- The fastest modular robot can move at 23 unit-sizes/second.
- The largest simulated system contained many 100,000's of units.
Challenges, solutions, and opportunities
Since the early demonstrations of early modular self-reconfiguring systems, the size, robustness and performance has been continuously improving. In parallel, planning and control algorithms have been progressing to handle thousands of units. There are, however, several key steps that are necessary for these systems to realize their promise of adaptability, robustness and low cost. These steps can be broken down into challenges in the hardware design, in planning and control algorithms and in application. These challenges are often intertwined.Hardware design challenges
The extent to which the promise of self-reconfiguring robotic systems can be realized depends critically on the numbers of modules in the system. To date, only systems with up to about 50 units have been demonstrated, with this number stagnating over almost a decade. There are a number of fundamental limiting factors that govern this number:- Limits on strength, precision, and field robustness (both mechanical and electrical) of bonding/docking interfaces between modules
- Limits on motor power, motion precision and energetic efficiency of units, (i.e. specific power, specific torque)
- Hardware/software design. Hardware that is designed to make the software problem easier. Self-reconfiguring systems have more tightly coupled hardware and software than any other existing system.
Planning and control challenges
Though algorithms have been developed for handling thousands of units in ideal conditions, challenges to scalability remain both in low-level control and high-level planning to overcome realistic constraints:- Algorithms for parallel-motion for large scale manipulation and locomotion
- Algorithms for robustly handling a variety of failure modes, from misalignments, dead-units (not responding, not releasing) to units that behave erratically.
- Algorithms that determine the optimal configuration for a given task
- Algorithms for optimal (time, energy) reconfiguration plan
- Efficient and scalable (asynchronous) communication among multiple units
Application challenges
Though the advantages of Modular self-reconfiguring robotic systems is largely recognized, it has been difficult to identify specific application domains where benefits can be demonstrated in the short term. Some suggested applications are- Space explorationSpace explorationSpace exploration is the use of space technology to explore outer space. Physical exploration of space is conducted both by human spaceflights and by robotic spacecraft....
and Space colonizationSpace colonizationSpace colonization is the concept of permanent human habitation outside of Earth. Although hypothetical at the present time, there are many proposals and speculations about the first space colony...
applications, e.g. Lunar colonization - Construction of large architectural systems
- Deep sea exploration/mining
- Search and rescue in unstructured environments
- Rapid construction of arbitrary tools under space/weight constraints
- Disaster relief shelters for displaced peoples
- Shelters for impoverished areas which require little on-the-ground expertise to assemble
Grand Challenges
Several robotic fields have identified ‘’Grand Challenges’’ that act as a catalyst for development and serve as a short-term goal in absence of immediate ‘’killer apps’’. The Grand Challenge is not in itself a research agenda or milestone, but a means to stimulate and evaluate coordinated progress across multiple technical frontiers. Several Grand Challenges have been proposed for the modular self-reconfiguring robotics field:- Demonstration of a system with >1000 units. Physical demonstration of such a system will inevitably require rethinking key hardware and algorithmic issues, as well as handling noise and error.
- Robosphere. A self-sustaining robotic ecology, isolated for a long period of time (1 year) that needs to sustain operation and accomplish unforeseen tasks without any human presence.
- Self replication A system with many units capable of self replication by collecting scattered building blocks will require solving many of the hardware and algorithmic challenges.
- Ultimate Construction A system capable of making objects out of the components of, say, a wall.
- Biofilter analogy If the system is ever made small enough to be injected into a mammal, one task may be to monitor molecules in the blood stream and allow some to pass and others not to, somewhat like the Blood-brain barrierBlood-brain barrierThe blood–brain barrier is a separation of circulating blood and the brain extracellular fluid in the central nervous system . It occurs along all capillaries and consists of tight junctions around the capillaries that do not exist in normal circulation. Endothelial cells restrict the diffusion...
. As a challenge, an analogy may be made where system must be able to:- be inserted into a hole one module’s diameter.
- travel some specified distance in a channel that is say roughly 40 x 40 module diameters in area.
- form a barrier fully conforming to the channel (whose shape is non-regular, and unknown beforehand).
- allow some objects to pass and others not to (not based on size).
- Since sensing is not the emphasis of this work, the actual detection of the passable objects should be made trivial.
Inductive Transducers
A unique potential solution that can be exploited is the use of inductors as transducers. This could be useful for dealing with docking and bonding problems. At the same time it could also be beneficial for its capabilities of docking detection (alignment and finding distance), power transmission, and (data signal) communication. A proof-of-concept video can be seenhere. The rather limited exploration down this avenue is probably a consequence of the historical lack of need in any applications for such an approach.
Modular Robotics Google Group
Modular Robotics Google Group is an open public forum dedicated to announcements of events in the field of Modular Robotics. This medium is used to disseminate calls to workshops, special issues and other academic activities of interest to modular robotics researchers. The founders of this Google group intend it to facilitate the exchange of information and ideas within the community of modular robotics researchers around the world and thus promote acceleration of advancements in modular robotics. Anybody who is interested in objectives and progress of Modular Robotics can join this Google group and learn about the new developments in this field.External links
Modular self-reconfiguring robotRobot
A robot is a mechanical or virtual intelligent agent that can perform tasks automatically or with guidance, typically by remote control. In practice a robot is usually an electro-mechanical machine that is guided by computer and electronic programming. Robots can be autonomous, semi-autonomous or...
ic systems or self-reconfigurable modular robots are autonomous kinematic machines with variable morphology
Morphology
Morphology may mean:*Morphology , the study of the structure and content of word forms*Morphology , the study of the form or shape of an organism or part thereof...
. Beyond conventional actuation, sensing and control typically found in fixed-morphology robots, self-reconfiguring robots are also able to deliberately change their own shape by rearranging the connectivity of their parts, in order to adapt to new circumstances, perform new tasks, or recover from damage.
For example, a robot made of such components could assume a worm
Worm
The term worm refers to an obsolete taxon used by Carolus Linnaeus and Jean-Baptiste Lamarck for all non-arthropod invertebrate animals, and stems from the Old English word wyrm. Currently it is used to describe many different distantly-related animals that typically have a long cylindrical...
-like shape to move through a narrow pipe, reassemble into something with spider
Spider
Spiders are air-breathing arthropods that have eight legs, and chelicerae with fangs that inject venom. They are the largest order of arachnids and rank seventh in total species diversity among all other groups of organisms...
-like legs to cross uneven terrain, then form a third arbitrary object (like a ball or wheel that can spin itself) to move quickly over a fairly flat terrain; it can also be used for making "fixed" objects, such as walls, shelters, or buildings.
In some cases this involves each module having 2 or more connectors for connecting several together. They can contain electronics
Electronics
Electronics is the branch of science, engineering and technology that deals with electrical circuits involving active electrical components such as vacuum tubes, transistors, diodes and integrated circuits, and associated passive interconnection technologies...
, sensor
Sensor
A sensor is a device that measures a physical quantity and converts it into a signal which can be read by an observer or by an instrument. For example, a mercury-in-glass thermometer converts the measured temperature into expansion and contraction of a liquid which can be read on a calibrated...
s, computer processors, memory
Memory
In psychology, memory is an organism's ability to store, retain, and recall information and experiences. Traditional studies of memory began in the fields of philosophy, including techniques of artificially enhancing memory....
, and power supplies; they can also contain actuator
Actuator
An actuator is a type of motor for moving or controlling a mechanism or system. It is operated by a source of energy, usually in the form of an electric current, hydraulic fluid pressure or pneumatic pressure, and converts that energy into some kind of motion. An actuator is the mechanism by which...
s that are used for manipulating their location in the environment and in relation with each other. A feature found in some cases is the ability of the modules to automatically connect and disconnect themselves to and from each other, and to form into many objects or perform many tasks moving or manipulating the environment.
By saying "self-reconfiguring" or "self-reconfigurable" it means that the mechanism or device is capable of utilizing its own system of control such as with actuators or stochastic means to change its overall structural shape. Having the quality of being "modular" in "self-reconfiguring modular robotics" is to say that the same module or set of modules can be added to or removed from the system, as opposed to being generically "modularized" in the broader sense. The underlying intent is to have an indefinite number of identical modules, or a finite and relatively small set of identical modules, in a mesh or matrix structure of self-reconfigurable modules.
Self-reconfiguration is also different from the concept of self-replication
Self-replication
Self-replication is any behavior of a dynamical system that yields construction of an identical copy of that dynamical system. Biological cells, given suitable environments, reproduce by cell division. During cell division, DNA is replicated and can be transmitted to offspring during reproduction...
, and self-replication is not necessarily a quality that a self-reconfigurable module or collection of such modules can or must possess. A matrix of N-number of modules does not need to be able to increase the quantity of modules to greater than N to be considered self-reconfigurable. It is sufficient for self-reconfigurable modules to be a device that is produced at a conventional factory, where dedicated machines stamp or mold components, and factory workers on an assembly line assemble the components to build each module.
There are two basic types of methods of segment articulation that self-reconfigurable mechanisms can utilize to reshape their structures, chain reconfiguration and lattice reconfiguration.
Structure and control
Modular robots are usually composed of multiple building blocks of a relatively small repertoire, with uniform docking interfaces that allow transfer of mechanical forces and moments, electrical power and communication throughout the robot.The modular building blocks usually consist of some primary structural actuated unit, and potentially additional specialized units such as grippers, feet, wheels, cameras, payload and energy storage and generation.
A taxonomy of architectures
Modular self-reconfiguring robotic systems can be generally classified into several architectural groups by the geometric arrangement of their unit (lattice vs. chain). Several systems exhibit hybrid properties.- Lattice architectures have units that are arranged and connected in some regular, space-filling three-dimensional pattern, such as a cubical or hexagonal grid. Control and motion are executed in parallel. Lattice architectures usually offer simpler computational representation that can be more easily scaled to complex systems.
- Chain/tree architectures have units that are connected together in a string or tree topology. This chain or tree can fold up to become space filling, but underlying architecture is serial. Chain architectures can reach any point in space, and are therefore more versatile but more computationally difficult to represent and analyze. Tree architectures may resemble a bush robotBush robotBush robots, as envisioned by Hans Moravec, are the ultimate in dexterity and reconfigurability. They earn their nickname from their appearance: bush robots repeatedly branch in a fractal way into trillions of nanoscale fingers...
Modular robotic systems can also be classified according to the way by which units are reconfigured (moved) into place.
- Deterministic reconfiguration relies on units moving or being directly manipulated into their target location during reconfiguration. The exact location of each unit is known at all times. Reconfiguration times can be guaranteed, but sophisticated feedback control is necessary to assure precise manipulation. Macro-scale systems are usually deterministic.
- Stochastic reconfiguration relies on units moving around using statistical processes (like Brownian motion). The exact location of each unit only known when it is connected to the main structure, but it may take unknown paths to move between locations. Reconfiguration times can be guaranteed only statistically. Stochastic architectures are more favorable at micro scales.
Modular robotic system are also generally classified depending on the design of the modules.
- Homogeneous modular robot system has many same modules coming together to form a structure suitable to perform the required task. Its advantage over other systems is that there are easy to replicate, as there a is only a singular design. their disadvantage being their functionality get leimited depending on the modules design.
- Heterogeneous modular robot system has different modules which do specialized function coming together to form a structure suitable to perform the task. Its advantage beings depending on the requirement of task the modular robot could get new modules to enhance its capabilities.The disadvantage being it becomes a more complex design.
- Hybrid modular robot system has multiple modules of same functions and also of different functions coming together to form a structure suitable to perform the task. Its advantage is it combines the features of its predecessors.
Other modular robotic systems exist which are not self-reconfigurable, and thus do not formally belong to this family of robots though they may have similar appearance. For example, self-assembling systems may be composed of multiple modules but cannot dynamically control their target shape. Similarly, tensegrity robotics may be composed of multiple interchangeable modules but cannot self-reconfigure.
Motivation and inspiration
There are two key motivations for designing modular self-reconfiguring robotic systems.- Functional advantage: Self reconfiguring robotic systems are potentially more robust and more adaptive than conventional systems. The reconfiguration ability allows a robot or a group of robots to disassemble and reassemble machines to form new morphologies that are better suitable for new tasks, such as changing from a legged robot to a snake robot and then to a rolling robot. Since robot parts are interchangeable (within a robot and between different robots), machines can also replace faulty parts autonomously, leading to self-repair.
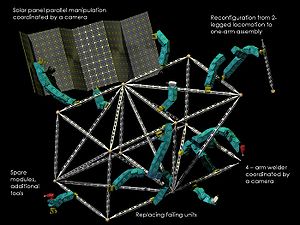
- Economic advantage: Self reconfiguring robotic systems can potentially lower overall robot cost by making a range of complex machines out of a single (or relatively few) types of mass-produced modules.
Both these advantages have not yet been fully realized. A modular robot is likely to be inferior in performance to any single custom robot tailored for a specific task. However, the advantage of modular robotics is only apparent when considering multiple tasks that would normally require a set of different robots.
The added degrees of freedom make modular robots more versatile in their potential capabilities, but also incur a performance tradeoff and increased mechanical and computational complexities.
The quest for self-reconfiguring robotic structures is to some extent inspired by envisioned applications such as long-term space missions, that require long-term self-sustaining robotic ecology that can handle unforeseen situations and may require self repair. A second source of inspiration are biological systems that are self-constructed out of a relatively small repertoire of lower-level building blocks (cells or amino acids, depending on scale of interest). This architecture underlies biological systems’ ability to physically adapt, grow, heal, and even self replicate – capabilities that would be desirable in many engineered systems.
Application areas
Given these advantages, where would a modular self-reconfigurable system be used? While the system has the promise of being capable of doing a wide variety of things, finding the “killer applicationKiller application
A killer application , in the jargon of marketing teams, has been used to refer to any computer program that is so necessary or desirable that it proves the core value of some larger technology, such as computer hardware, gaming console, software, or an operating system...
” has been somewhat elusive. Here are several examples:
Space exploration
One application that highlights the advantages of self-reconfigurable systems is long-term space missions. These require long-term self-sustaining robotic ecology that can handle unforeseen situations and may require self repair. Self-reconfigurable systems have the ability to handle tasks that are not known a priori especially compared to fixed configuration systems. In addition, space missions are highly volume and mass constrained. Sending a robot system that can reconfigure to achieve many tasks is better than sending many robots that each can do one task.Telepario
Another example of an application has been coined “telepario” by CMU professors Todd Mowry and Seth Goldstein. What the researchers propose to make are moving, physical,three-dimensional replicas of people or objects, so lifelike that human senses would accept them as real. This would eliminate the need for cumbersome virtual reality gear and overcome the viewing angle limitations of modern 3D approaches. The replicas would mimic the shape and appearance of a person or object being imaged in real time, and as the originals moved, so would their replicas. One aspect of this application is that the main development thrust is geometric representation rather than applying forces to the environment as in a typical robotic manipulation task.
This project is widely known as claytronics or programmable matter.
Bucket of stuff
A third long term vision for these systems has been called “bucket of stuff”. In this vision, consumers of the future have a container of self-reconfigurable modules say in their garage, basement, or attic. When the need arises, the consumer calls forth the robots to achieve a task such as “clean the gutters” or “change the oil in the car” and the robot assumes the shape needed and does the task.One source of inspiration for the development of these systems comes from the application. A second source is biological systems that are self-constructed out of a relatively small repertoire of lower-level building blocks (cells or amino acids, depending on scale of interest). This architecture underlies biological systems’ ability to physically adapt, grow, heal, and even self replicate – capabilities that would be desirable in many engineered systems.
History and state of the art
The roots of the concept of modular self-reconfigurable robots can be traced back to the “quick change” end effector and automatic tool changers in computer numerical controlled machining centers in the 1970s. Here, special modules each with a common connection mechanism could be automatically swapped out on the end of a robotic arm. However, taking the basic concept of the common connection mechanism and applying it to the whole robot was introduced by Toshio Fukuda with the CEBOT (short for cellular robot) in the late 1980s.The early 1990s saw further development from Greg Chirikjian, Mark Yim, Joseph Michael, and Satoshi Murata. Chirikjian, Michael, and Murata developed lattice reconfiguration systems and Yim developed a chain based system. While these researchers started with from a mechanical engineering emphasis, designing and building modules then developing code to program them, the work of Daniela Rus and Wei-min Shen developed hardware but had a greater impact on the programming aspects. They started a trend towards provable or verifiable distributed algorithms for the control of large numbers of modules.
One of the more interesting hardware platforms recently has been the MTRAN II and III systems developed by Satoshi Murata et al. This system is a hybrid chain and lattice system. It has the advantage of being able to achieve tasks more easily like chain systems, yet reconfigure like a lattice system.
More recently new efforts in stochastic self-assembly have been pursued by Hod Lipson and Eric Klavins. A large effort at CMU headed by Seth Goldstein and Todd Mowry has started looking at issues in developing millions of modules.
Many tasks have been shown to be achievable, especially with chain reconfiguration modules. This demonstrates the versatility of these systems however, the other two advantages, robustness and low cost have not been demonstrated. In general the prototype systems developed in the labs have been fragile and expensive as would be expected during any initial development.
There is a growing number of research groups actively involved in modular robotics research. To date, about 30 systems have been designed and constructed, some of which are shown below.
System | Class, DOF | Author | Year |
---|---|---|---|
CEBOT | Mobile | Fukuda et al. (Tsukuba) | 1988 |
Polypod | chain, 2, 3D | Yim (Stanford) | 1993 |
Metamorphic | lattice, 6, 2D | Chirikjian (Caltech) | 1993 |
Fracta | lattice, 3 2D | Murata (MEL) | 1994 |
Fractal Robots | lattice, 3D | Michael(UK) | 1995 |
Tetrobot | chain, 1 3D | Hamline et al. (RPI) | 1996 |
ANAT Robot | Chain/tree, 8D | Charles Khairallah (CA) | 1997 |
3D Fracta | lattice, 6 3D | Murata et al. (MEL) | 1998 |
Molecule | lattice, 4 3D | Kotay & Rus (Dartmouth) | 1998 |
CONRO | chain, 2 3D | Will & Shen (USC/ISI) | 1998 |
PolyBot | chain, 1 3D | Yim et al. (PARC) | 1998 |
TeleCube | lattice, 6 3D | Suh et al., (PARC) | 1998 |
Vertical | lattice, 2D | Hosakawa et al., (Riken) | 1998 |
Crystalline | lattice, 4 2D | Vona & Rus, (Dartmouth) | 1999 |
I-Cube | lattice, 3D | Unsal, (CMU) | 1999 |
M-TRAN I | hybrid, 2 3D | Murata et al.(AIST) | 1999 |
Pneumatic | lattice, 2D | Inou et al., (TiTech) | 2002 |
Uni Rover | mobile, 2 2D | Hirose et al., (TiTech) | 2002 |
M-TRAN II | hybrid, 2 3D | Murata et al., (AIST) | 2002 |
Atron | lattice, 1 3D | Stoy et al., (U.S Denmark) | 2003 |
S-bot S-bot mobile robot The s-bot is a small differential wheeled mobile robot developed at the LIS at the EPFL in Lausanne, Switzerland between 2001 and 2004. Targeted to swarm robotics, a field of artificial intelligence, it was developed within the Swarm-bots project, a Future and Emerging Technologies project... |
mobile, 3 2D | Mondada Francesco Mondada Francesco Mondada is a Swiss researcher in artificial intelligence and robotics. He is one of the creators of the Khepera, the S-bot and the e-puck mobile robots. He got a Master's degree in Microengineering at the EPFL in 1991 and a Ph.D. degree in 1997.He was the director of from its creation... et al., (EPFL) |
2003 |
Stochastic | lattice, 0 3D | White, Kopanski, Lipson (Cornell) | 2004 |
Superbot | hybrid, 3 3D | Shen et al., (USC/ISI) | 2004 |
Y1 Modules | Chain, 1 3D | Gonzalez-Gomez et al., (UAM) | 2004 |
M-TRAN III | hybrid, 2 3D | Kurokawa et al., (AIST) | 2005 |
AMOEBA-I | Mobile, 7 3D | Liu JG et al., (SIA) | 2005 |
Catom | lattice, 0 2D | Goldstein et al., (CMU) | 2005 |
Stochastic-3D | lattice, 0 3D | White, Zykov, Lipson (Cornell) | 2005 |
Molecubes | chain, 1 3D | Zykov, Mytilinaios, Lipson (Cornell) | 2005 |
Prog. parts | lattice, 0 2D | Klavins, (U. Washington) | 2005 |
Miche | lattice, 0 3D | Rus et al., (MIT) | 2006 |
GZ-I Modules | Chain, 1 3D | Zhang & Gonzalez-Gomez (U. Hamburg, UAM) | 2006 |
Evolve | Chain, 2 3D | Chang Fanxi, Francis (NUS) | 2008 |
Odin | Hybrid, 3 3D | Lyder et al., Modular Robotics Research Lab, (USD) | 2008 |
Roombots | Hybrid, 3 3D | Sproewitz, Moeckel, Ijspeert, Biorobotics Laboratory, (EPFL) | 2009 |
Some current systems
ANAT Robot (1997)A chain/tree hyper-redundant
Redundancy (engineering)
In engineering, redundancy is the duplication of critical components or functions of a system with the intention of increasing reliability of the system, usually in the case of a backup or fail-safe....
modular robotic system invented by Charles Khairallah from Robotics Design Inc in Montreal
Montreal
Montreal is a city in Canada. It is the largest city in the province of Quebec, the second-largest city in Canada and the seventh largest in North America...
, Quebec
Quebec
Quebec or is a province in east-central Canada. It is the only Canadian province with a predominantly French-speaking population and the only one whose sole official language is French at the provincial level....
, Canada
Canada
Canada is a North American country consisting of ten provinces and three territories. Located in the northern part of the continent, it extends from the Atlantic Ocean in the east to the Pacific Ocean in the west, and northward into the Arctic Ocean...
. This robot is designed with ANAT Technology (Articulated Nimble Adaptable Trunk) and is currently used for industrial manipulating under the name ANAT AMI-100. Robotics Design's patented U and H shaped modules, of which this robot is composed, form the other robots in the ANAT robotics family. This robot can re-configure and/or self-reconfigure to form different shapes, due to its LEGO
Lego
Lego is a line of construction toys manufactured by the Lego Group, a privately held company based in Billund, Denmark. The company's flagship product, Lego, consists of colorful interlocking plastic bricks and an accompanying array of gears, minifigures and various other parts...
-like sets of modules with one degree of freedom each. This allows robots to be designed using ANAT modules with n° of freedom. Configurations range from mobile robots (ANATROLLER), manipulators (ANAT AMI-100), to walking robots (ANAT Walker).
PolyBot G3 (2002)
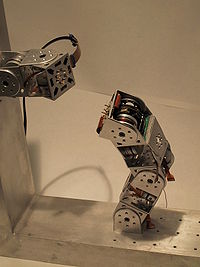
M-TRAN III (2005)
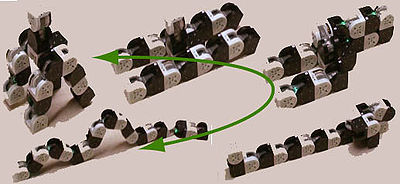
AMOEBA-I (2005)
AMOEBA-I, a three-module reconfigurable mobile robot was developed in Shenyang Institute of Automation (SIA), Chinese Academy of Sciences (CAS) by Liu J G et al.http://ieeexplore.ieee.org/xpls/abs_all.jsp?arnumber=1708645http://www.springerlink.com/content/m81820061n48jh32/.AMOEBA-I has nine kinds of non-isomorphic configurations and high mobility under unstructured environments.Four generations of its platform have been developed and a series of researches have been carried out on their reconfiguration mechanism, non-isomorphic configurations, tipover stability, and reconfiguration planning. Experiments have demonstrated that such kind structure permits good mobility and high flexibility to uneven terrain. Being hyper-redundant, modularized and reconfigurable, AMOEBA-I has many possible applications such as Urban Search and Rescue (USAR) and space exploration.
Ref_1: see http://ieeexplore.ieee.org/xpls/abs_all.jsp?arnumber=1708645;
Ref_2: see http://www.springerlink.com/content/m81820061n48jh32/
Stochastic-3D (2005)
High spatial resolution for arbitrary three-dimensional shape formation with modular robots can be accomplished using lattice system with large quantities of very small, prospectively microscopic modules. At small scales, and with large quantities of modules, deterministic control over reconfiguration of individual modules will become unfeasible, while stochastic mechanisms will naturally prevail. Microscopic size of modules will make the use of electromagnetic actuation and interconnection prohibitive, as well, as the use of on-board power storage.
Three large scale prototypes were built in attempt to demonstrate dynamically programmable three-dimensional stochastic reconfiguration in a neutral-buoyancy environment. The first prototype used electromagnets for module reconfiguration and interconnection. The modules were 100 mm cubes and weighed 0.81 kg. The second prototype used stochastic fluidic reconfiguration and interconnection mechanism. Its 130 mm cubic modules weighed 1.78 kg each and made reconfiguration experiments excessively slow. The current third implementation inherits the fluidic reconfiguration principle. The lattice grid size is 80 mm, and the reconfiguration experiments are under way. More information can be found at the CCSL Stochastic Modular Robotics webpage.
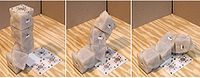
This chain self-reconfiguring system was built by the Cornell Computational Synthesis Lab to physically demonstrate artificial kinematic self-reproduction. Each module is a 0.65 kg cube with 100 mm long edges and one rotational degree of freedom. The axis of rotation is aligned with the cube's longest diagonal. Physical self-reproduction of a three- and a four-module robots was demonstrated. It was also shown that, disregarding the gravity constraints, an infinite number of self-reproducing chain meta-structures can be built from Molecubes. More information can be found at the CCSL Self-Replication webpage.
The Programmable Parts (2005)
The programmable parts are stirred randomly on an air-hockey table by randomly actuated air jets. When they collide and stick, they can communicate and decide whether to stay stuck, or if and when to detach. Local interaction rules can be devised and optimized to guide the robots to make any desired global shape. More information can be found at the programmable parts web page.
SuperBot (2006)
The SuperBot modules fall into the chain/tree architecture. The modules have three degrees of freedom each. The design is based on two previous systems: Conro (by the same research group) and MTRAN (by Murata et al.). Each module can connect to another module through one of its six dock connectors. They can communicate and share power through their dock connectors. Several locomotion gaits have been developed for different arrangements of modules. For high-level communication the modules use hormone-based control, a distributed, scalable protocol that does not require the modules to have unique ID's.
Miche (2006)
The Miche system is a modular lattice system capable of arbitrary shape formation. Each module is an autonomous robot module capable of connecting to and communicating with its immediate neighbors. When assembled into a structure, the modules form a system that can be virtually sculpted using a computer interface and a distributed process. The group of modules collectively decide who is on the final shape and who is not using algorithms that minimize the information transmission and storage. Finally, the modules not in the structure let go and fall off under the control of an external force, in this case gravity.
More details at Miche (Rus et al.).
Roombots (2009)
Roombots have a hybrid chain/tree architecture. Each module has three degree of freedom, two of them using the diametrical axis within a regular cube, and a third (center) axis of rotation connecting the two spherical parts. All three axes are continuously rotatory. The outer Roombots DOF is using the same axis-orientation as Molecubes, the third, central Roombots axis enables the module to rotate its two outer DOF against each other. This novel feature enables a single Roombots module to locomote on flat terrain, but also to climb a wall, or to cross a concave, perpendicular edge. Convex edges require the assembly of at least two modules into a Roombots "Metamodule". Each module has ten available connector slots, currently two of them are equipped with an active connection mechanism based on mechanical latches.
Roombots are designed for two tasks: to eventually shape objects of daily life, e.g. furniture, and to locomote, e.g. as a quadruped or a tripod robot made from multiple modules.
More information can be found at Biorobotics Laboratory Roombots webpage.
Quantitative accomplishment
- The robot with most active modules has 56 units
- The smallest actuated modular unit has a size of
mm - The largest actuated modular unit (by volume) has the size of 8 m^3 <(GHFC)giant helium filled catoms, CMU>
- The strongest actuation modules are able to lift 5 identical horizontally cantilevered units.
- The fastest modular robot can move at 23 unit-sizes/second.
- The largest simulated system contained many 100,000's of units.
Challenges, solutions, and opportunities
Since the early demonstrations of early modular self-reconfiguring systems, the size, robustness and performance has been continuously improving. In parallel, planning and control algorithms have been progressing to handle thousands of units. There are, however, several key steps that are necessary for these systems to realize their promise of adaptability, robustness and low cost. These steps can be broken down into challenges in the hardware design, in planning and control algorithms and in application. These challenges are often intertwined.Hardware design challenges
The extent to which the promise of self-reconfiguring robotic systems can be realized depends critically on the numbers of modules in the system. To date, only systems with up to about 50 units have been demonstrated, with this number stagnating over almost a decade. There are a number of fundamental limiting factors that govern this number:- Limits on strength, precision, and field robustness (both mechanical and electrical) of bonding/docking interfaces between modules
- Limits on motor power, motion precision and energetic efficiency of units, (i.e. specific power, specific torque)
- Hardware/software design. Hardware that is designed to make the software problem easier. Self-reconfiguring systems have more tightly coupled hardware and software than any other existing system.
Planning and control challenges
Though algorithms have been developed for handling thousands of units in ideal conditions, challenges to scalability remain both in low-level control and high-level planning to overcome realistic constraints:- Algorithms for parallel-motion for large scale manipulation and locomotion
- Algorithms for robustly handling a variety of failure modes, from misalignments, dead-units (not responding, not releasing) to units that behave erratically.
- Algorithms that determine the optimal configuration for a given task
- Algorithms for optimal (time, energy) reconfiguration plan
- Efficient and scalable (asynchronous) communication among multiple units
Application challenges
Though the advantages of Modular self-reconfiguring robotic systems is largely recognized, it has been difficult to identify specific application domains where benefits can be demonstrated in the short term. Some suggested applications are- Space explorationSpace explorationSpace exploration is the use of space technology to explore outer space. Physical exploration of space is conducted both by human spaceflights and by robotic spacecraft....
and Space colonizationSpace colonizationSpace colonization is the concept of permanent human habitation outside of Earth. Although hypothetical at the present time, there are many proposals and speculations about the first space colony...
applications, e.g. Lunar colonization - Construction of large architectural systems
- Deep sea exploration/mining
- Search and rescue in unstructured environments
- Rapid construction of arbitrary tools under space/weight constraints
- Disaster relief shelters for displaced peoples
- Shelters for impoverished areas which require little on-the-ground expertise to assemble
Grand Challenges
Several robotic fields have identified ‘’Grand Challenges’’ that act as a catalyst for development and serve as a short-term goal in absence of immediate ‘’killer apps’’. The Grand Challenge is not in itself a research agenda or milestone, but a means to stimulate and evaluate coordinated progress across multiple technical frontiers. Several Grand Challenges have been proposed for the modular self-reconfiguring robotics field:- Demonstration of a system with >1000 units. Physical demonstration of such a system will inevitably require rethinking key hardware and algorithmic issues, as well as handling noise and error.
- Robosphere. A self-sustaining robotic ecology, isolated for a long period of time (1 year) that needs to sustain operation and accomplish unforeseen tasks without any human presence.
- Self replication A system with many units capable of self replication by collecting scattered building blocks will require solving many of the hardware and algorithmic challenges.
- Ultimate Construction A system capable of making objects out of the components of, say, a wall.
- Biofilter analogy If the system is ever made small enough to be injected into a mammal, one task may be to monitor molecules in the blood stream and allow some to pass and others not to, somewhat like the Blood-brain barrierBlood-brain barrierThe blood–brain barrier is a separation of circulating blood and the brain extracellular fluid in the central nervous system . It occurs along all capillaries and consists of tight junctions around the capillaries that do not exist in normal circulation. Endothelial cells restrict the diffusion...
. As a challenge, an analogy may be made where system must be able to:- be inserted into a hole one module’s diameter.
- travel some specified distance in a channel that is say roughly 40 x 40 module diameters in area.
- form a barrier fully conforming to the channel (whose shape is non-regular, and unknown beforehand).
- allow some objects to pass and others not to (not based on size).
- Since sensing is not the emphasis of this work, the actual detection of the passable objects should be made trivial.
Inductive Transducers
A unique potential solution that can be exploited is the use of inductors as transducers. This could be useful for dealing with docking and bonding problems. At the same time it could also be beneficial for its capabilities of docking detection (alignment and finding distance), power transmission, and (data signal) communication. A proof-of-concept video can be seenhere. The rather limited exploration down this avenue is probably a consequence of the historical lack of need in any applications for such an approach.
Modular Robotics Google Group
Modular Robotics Google Group is an open public forum dedicated to announcements of events in the field of Modular Robotics. This medium is used to disseminate calls to workshops, special issues and other academic activities of interest to modular robotics researchers. The founders of this Google group intend it to facilitate the exchange of information and ideas within the community of modular robotics researchers around the world and thus promote acceleration of advancements in modular robotics. Anybody who is interested in objectives and progress of Modular Robotics can join this Google group and learn about the new developments in this field.External links
Modular self-reconfiguring robotRobot
A robot is a mechanical or virtual intelligent agent that can perform tasks automatically or with guidance, typically by remote control. In practice a robot is usually an electro-mechanical machine that is guided by computer and electronic programming. Robots can be autonomous, semi-autonomous or...
ic systems or self-reconfigurable modular robots are autonomous kinematic machines with variable morphology
Morphology
Morphology may mean:*Morphology , the study of the structure and content of word forms*Morphology , the study of the form or shape of an organism or part thereof...
. Beyond conventional actuation, sensing and control typically found in fixed-morphology robots, self-reconfiguring robots are also able to deliberately change their own shape by rearranging the connectivity of their parts, in order to adapt to new circumstances, perform new tasks, or recover from damage.
For example, a robot made of such components could assume a worm
Worm
The term worm refers to an obsolete taxon used by Carolus Linnaeus and Jean-Baptiste Lamarck for all non-arthropod invertebrate animals, and stems from the Old English word wyrm. Currently it is used to describe many different distantly-related animals that typically have a long cylindrical...
-like shape to move through a narrow pipe, reassemble into something with spider
Spider
Spiders are air-breathing arthropods that have eight legs, and chelicerae with fangs that inject venom. They are the largest order of arachnids and rank seventh in total species diversity among all other groups of organisms...
-like legs to cross uneven terrain, then form a third arbitrary object (like a ball or wheel that can spin itself) to move quickly over a fairly flat terrain; it can also be used for making "fixed" objects, such as walls, shelters, or buildings.
In some cases this involves each module having 2 or more connectors for connecting several together. They can contain electronics
Electronics
Electronics is the branch of science, engineering and technology that deals with electrical circuits involving active electrical components such as vacuum tubes, transistors, diodes and integrated circuits, and associated passive interconnection technologies...
, sensor
Sensor
A sensor is a device that measures a physical quantity and converts it into a signal which can be read by an observer or by an instrument. For example, a mercury-in-glass thermometer converts the measured temperature into expansion and contraction of a liquid which can be read on a calibrated...
s, computer processors, memory
Memory
In psychology, memory is an organism's ability to store, retain, and recall information and experiences. Traditional studies of memory began in the fields of philosophy, including techniques of artificially enhancing memory....
, and power supplies; they can also contain actuator
Actuator
An actuator is a type of motor for moving or controlling a mechanism or system. It is operated by a source of energy, usually in the form of an electric current, hydraulic fluid pressure or pneumatic pressure, and converts that energy into some kind of motion. An actuator is the mechanism by which...
s that are used for manipulating their location in the environment and in relation with each other. A feature found in some cases is the ability of the modules to automatically connect and disconnect themselves to and from each other, and to form into many objects or perform many tasks moving or manipulating the environment.
By saying "self-reconfiguring" or "self-reconfigurable" it means that the mechanism or device is capable of utilizing its own system of control such as with actuators or stochastic means to change its overall structural shape. Having the quality of being "modular" in "self-reconfiguring modular robotics" is to say that the same module or set of modules can be added to or removed from the system, as opposed to being generically "modularized" in the broader sense. The underlying intent is to have an indefinite number of identical modules, or a finite and relatively small set of identical modules, in a mesh or matrix structure of self-reconfigurable modules.
Self-reconfiguration is also different from the concept of self-replication
Self-replication
Self-replication is any behavior of a dynamical system that yields construction of an identical copy of that dynamical system. Biological cells, given suitable environments, reproduce by cell division. During cell division, DNA is replicated and can be transmitted to offspring during reproduction...
, and self-replication is not necessarily a quality that a self-reconfigurable module or collection of such modules can or must possess. A matrix of N-number of modules does not need to be able to increase the quantity of modules to greater than N to be considered self-reconfigurable. It is sufficient for self-reconfigurable modules to be a device that is produced at a conventional factory, where dedicated machines stamp or mold components, and factory workers on an assembly line assemble the components to build each module.
There are two basic types of methods of segment articulation that self-reconfigurable mechanisms can utilize to reshape their structures, chain reconfiguration and lattice reconfiguration.
Structure and control
Modular robots are usually composed of multiple building blocks of a relatively small repertoire, with uniform docking interfaces that allow transfer of mechanical forces and moments, electrical power and communication throughout the robot.The modular building blocks usually consist of some primary structural actuated unit, and potentially additional specialized units such as grippers, feet, wheels, cameras, payload and energy storage and generation.
A taxonomy of architectures
Modular self-reconfiguring robotic systems can be generally classified into several architectural groups by the geometric arrangement of their unit (lattice vs. chain). Several systems exhibit hybrid properties.- Lattice architectures have units that are arranged and connected in some regular, space-filling three-dimensional pattern, such as a cubical or hexagonal grid. Control and motion are executed in parallel. Lattice architectures usually offer simpler computational representation that can be more easily scaled to complex systems.
- Chain/tree architectures have units that are connected together in a string or tree topology. This chain or tree can fold up to become space filling, but underlying architecture is serial. Chain architectures can reach any point in space, and are therefore more versatile but more computationally difficult to represent and analyze. Tree architectures may resemble a bush robotBush robotBush robots, as envisioned by Hans Moravec, are the ultimate in dexterity and reconfigurability. They earn their nickname from their appearance: bush robots repeatedly branch in a fractal way into trillions of nanoscale fingers...
Modular robotic systems can also be classified according to the way by which units are reconfigured (moved) into place.
- Deterministic reconfiguration relies on units moving or being directly manipulated into their target location during reconfiguration. The exact location of each unit is known at all times. Reconfiguration times can be guaranteed, but sophisticated feedback control is necessary to assure precise manipulation. Macro-scale systems are usually deterministic.
- Stochastic reconfiguration relies on units moving around using statistical processes (like Brownian motion). The exact location of each unit only known when it is connected to the main structure, but it may take unknown paths to move between locations. Reconfiguration times can be guaranteed only statistically. Stochastic architectures are more favorable at micro scales.
Modular robotic system are also generally classified depending on the design of the modules.
- Homogeneous modular robot system has many same modules coming together to form a structure suitable to perform the required task. Its advantage over other systems is that there are easy to replicate, as there a is only a singular design. their disadvantage being their functionality get leimited depending on the modules design.
- Heterogeneous modular robot system has different modules which do specialized function coming together to form a structure suitable to perform the task. Its advantage beings depending on the requirement of task the modular robot could get new modules to enhance its capabilities.The disadvantage being it becomes a more complex design.
- Hybrid modular robot system has multiple modules of same functions and also of different functions coming together to form a structure suitable to perform the task. Its advantage is it combines the features of its predecessors.
Other modular robotic systems exist which are not self-reconfigurable, and thus do not formally belong to this family of robots though they may have similar appearance. For example, self-assembling systems may be composed of multiple modules but cannot dynamically control their target shape. Similarly, tensegrity robotics may be composed of multiple interchangeable modules but cannot self-reconfigure.
Motivation and inspiration
There are two key motivations for designing modular self-reconfiguring robotic systems.- Functional advantage: Self reconfiguring robotic systems are potentially more robust and more adaptive than conventional systems. The reconfiguration ability allows a robot or a group of robots to disassemble and reassemble machines to form new morphologies that are better suitable for new tasks, such as changing from a legged robot to a snake robot and then to a rolling robot. Since robot parts are interchangeable (within a robot and between different robots), machines can also replace faulty parts autonomously, leading to self-repair.
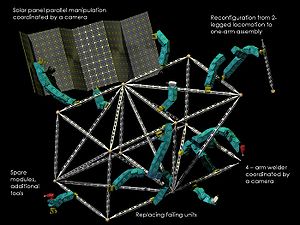
- Economic advantage: Self reconfiguring robotic systems can potentially lower overall robot cost by making a range of complex machines out of a single (or relatively few) types of mass-produced modules.
Both these advantages have not yet been fully realized. A modular robot is likely to be inferior in performance to any single custom robot tailored for a specific task. However, the advantage of modular robotics is only apparent when considering multiple tasks that would normally require a set of different robots.
The added degrees of freedom make modular robots more versatile in their potential capabilities, but also incur a performance tradeoff and increased mechanical and computational complexities.
The quest for self-reconfiguring robotic structures is to some extent inspired by envisioned applications such as long-term space missions, that require long-term self-sustaining robotic ecology that can handle unforeseen situations and may require self repair. A second source of inspiration are biological systems that are self-constructed out of a relatively small repertoire of lower-level building blocks (cells or amino acids, depending on scale of interest). This architecture underlies biological systems’ ability to physically adapt, grow, heal, and even self replicate – capabilities that would be desirable in many engineered systems.
Application areas
Given these advantages, where would a modular self-reconfigurable system be used? While the system has the promise of being capable of doing a wide variety of things, finding the “killer applicationKiller application
A killer application , in the jargon of marketing teams, has been used to refer to any computer program that is so necessary or desirable that it proves the core value of some larger technology, such as computer hardware, gaming console, software, or an operating system...
” has been somewhat elusive. Here are several examples:
Space exploration
One application that highlights the advantages of self-reconfigurable systems is long-term space missions. These require long-term self-sustaining robotic ecology that can handle unforeseen situations and may require self repair. Self-reconfigurable systems have the ability to handle tasks that are not known a priori especially compared to fixed configuration systems. In addition, space missions are highly volume and mass constrained. Sending a robot system that can reconfigure to achieve many tasks is better than sending many robots that each can do one task.Telepario
Another example of an application has been coined “telepario” by CMU professors Todd Mowry and Seth Goldstein. What the researchers propose to make are moving, physical,three-dimensional replicas of people or objects, so lifelike that human senses would accept them as real. This would eliminate the need for cumbersome virtual reality gear and overcome the viewing angle limitations of modern 3D approaches. The replicas would mimic the shape and appearance of a person or object being imaged in real time, and as the originals moved, so would their replicas. One aspect of this application is that the main development thrust is geometric representation rather than applying forces to the environment as in a typical robotic manipulation task.
This project is widely known as claytronics or programmable matter.
Bucket of stuff
A third long term vision for these systems has been called “bucket of stuff”. In this vision, consumers of the future have a container of self-reconfigurable modules say in their garage, basement, or attic. When the need arises, the consumer calls forth the robots to achieve a task such as “clean the gutters” or “change the oil in the car” and the robot assumes the shape needed and does the task.One source of inspiration for the development of these systems comes from the application. A second source is biological systems that are self-constructed out of a relatively small repertoire of lower-level building blocks (cells or amino acids, depending on scale of interest). This architecture underlies biological systems’ ability to physically adapt, grow, heal, and even self replicate – capabilities that would be desirable in many engineered systems.
History and state of the art
The roots of the concept of modular self-reconfigurable robots can be traced back to the “quick change” end effector and automatic tool changers in computer numerical controlled machining centers in the 1970s. Here, special modules each with a common connection mechanism could be automatically swapped out on the end of a robotic arm. However, taking the basic concept of the common connection mechanism and applying it to the whole robot was introduced by Toshio Fukuda with the CEBOT (short for cellular robot) in the late 1980s.The early 1990s saw further development from Greg Chirikjian, Mark Yim, Joseph Michael, and Satoshi Murata. Chirikjian, Michael, and Murata developed lattice reconfiguration systems and Yim developed a chain based system. While these researchers started with from a mechanical engineering emphasis, designing and building modules then developing code to program them, the work of Daniela Rus and Wei-min Shen developed hardware but had a greater impact on the programming aspects. They started a trend towards provable or verifiable distributed algorithms for the control of large numbers of modules.
One of the more interesting hardware platforms recently has been the MTRAN II and III systems developed by Satoshi Murata et al. This system is a hybrid chain and lattice system. It has the advantage of being able to achieve tasks more easily like chain systems, yet reconfigure like a lattice system.
More recently new efforts in stochastic self-assembly have been pursued by Hod Lipson and Eric Klavins. A large effort at CMU headed by Seth Goldstein and Todd Mowry has started looking at issues in developing millions of modules.
Many tasks have been shown to be achievable, especially with chain reconfiguration modules. This demonstrates the versatility of these systems however, the other two advantages, robustness and low cost have not been demonstrated. In general the prototype systems developed in the labs have been fragile and expensive as would be expected during any initial development.
There is a growing number of research groups actively involved in modular robotics research. To date, about 30 systems have been designed and constructed, some of which are shown below.
System | Class, DOF | Author | Year |
---|---|---|---|
CEBOT | Mobile | Fukuda et al. (Tsukuba) | 1988 |
Polypod | chain, 2, 3D | Yim (Stanford) | 1993 |
Metamorphic | lattice, 6, 2D | Chirikjian (Caltech) | 1993 |
Fracta | lattice, 3 2D | Murata (MEL) | 1994 |
Fractal Robots | lattice, 3D | Michael(UK) | 1995 |
Tetrobot | chain, 1 3D | Hamline et al. (RPI) | 1996 |
ANAT Robot | Chain/tree, 8D | Charles Khairallah (CA) | 1997 |
3D Fracta | lattice, 6 3D | Murata et al. (MEL) | 1998 |
Molecule | lattice, 4 3D | Kotay & Rus (Dartmouth) | 1998 |
CONRO | chain, 2 3D | Will & Shen (USC/ISI) | 1998 |
PolyBot | chain, 1 3D | Yim et al. (PARC) | 1998 |
TeleCube | lattice, 6 3D | Suh et al., (PARC) | 1998 |
Vertical | lattice, 2D | Hosakawa et al., (Riken) | 1998 |
Crystalline | lattice, 4 2D | Vona & Rus, (Dartmouth) | 1999 |
I-Cube | lattice, 3D | Unsal, (CMU) | 1999 |
M-TRAN I | hybrid, 2 3D | Murata et al.(AIST) | 1999 |
Pneumatic | lattice, 2D | Inou et al., (TiTech) | 2002 |
Uni Rover | mobile, 2 2D | Hirose et al., (TiTech) | 2002 |
M-TRAN II | hybrid, 2 3D | Murata et al., (AIST) | 2002 |
Atron | lattice, 1 3D | Stoy et al., (U.S Denmark) | 2003 |
S-bot S-bot mobile robot The s-bot is a small differential wheeled mobile robot developed at the LIS at the EPFL in Lausanne, Switzerland between 2001 and 2004. Targeted to swarm robotics, a field of artificial intelligence, it was developed within the Swarm-bots project, a Future and Emerging Technologies project... |
mobile, 3 2D | Mondada Francesco Mondada Francesco Mondada is a Swiss researcher in artificial intelligence and robotics. He is one of the creators of the Khepera, the S-bot and the e-puck mobile robots. He got a Master's degree in Microengineering at the EPFL in 1991 and a Ph.D. degree in 1997.He was the director of from its creation... et al., (EPFL) |
2003 |
Stochastic | lattice, 0 3D | White, Kopanski, Lipson (Cornell) | 2004 |
Superbot | hybrid, 3 3D | Shen et al., (USC/ISI) | 2004 |
Y1 Modules | Chain, 1 3D | Gonzalez-Gomez et al., (UAM) | 2004 |
M-TRAN III | hybrid, 2 3D | Kurokawa et al., (AIST) | 2005 |
AMOEBA-I | Mobile, 7 3D | Liu JG et al., (SIA) | 2005 |
Catom | lattice, 0 2D | Goldstein et al., (CMU) | 2005 |
Stochastic-3D | lattice, 0 3D | White, Zykov, Lipson (Cornell) | 2005 |
Molecubes | chain, 1 3D | Zykov, Mytilinaios, Lipson (Cornell) | 2005 |
Prog. parts | lattice, 0 2D | Klavins, (U. Washington) | 2005 |
Miche | lattice, 0 3D | Rus et al., (MIT) | 2006 |
GZ-I Modules | Chain, 1 3D | Zhang & Gonzalez-Gomez (U. Hamburg, UAM) | 2006 |
Evolve | Chain, 2 3D | Chang Fanxi, Francis (NUS) | 2008 |
Odin | Hybrid, 3 3D | Lyder et al., Modular Robotics Research Lab, (USD) | 2008 |
Roombots | Hybrid, 3 3D | Sproewitz, Moeckel, Ijspeert, Biorobotics Laboratory, (EPFL) | 2009 |
Some current systems
ANAT Robot (1997)A chain/tree hyper-redundant
Redundancy (engineering)
In engineering, redundancy is the duplication of critical components or functions of a system with the intention of increasing reliability of the system, usually in the case of a backup or fail-safe....
modular robotic system invented by Charles Khairallah from Robotics Design Inc in Montreal
Montreal
Montreal is a city in Canada. It is the largest city in the province of Quebec, the second-largest city in Canada and the seventh largest in North America...
, Quebec
Quebec
Quebec or is a province in east-central Canada. It is the only Canadian province with a predominantly French-speaking population and the only one whose sole official language is French at the provincial level....
, Canada
Canada
Canada is a North American country consisting of ten provinces and three territories. Located in the northern part of the continent, it extends from the Atlantic Ocean in the east to the Pacific Ocean in the west, and northward into the Arctic Ocean...
. This robot is designed with ANAT Technology (Articulated Nimble Adaptable Trunk) and is currently used for industrial manipulating under the name ANAT AMI-100. Robotics Design's patented U and H shaped modules, of which this robot is composed, form the other robots in the ANAT robotics family. This robot can re-configure and/or self-reconfigure to form different shapes, due to its LEGO
Lego
Lego is a line of construction toys manufactured by the Lego Group, a privately held company based in Billund, Denmark. The company's flagship product, Lego, consists of colorful interlocking plastic bricks and an accompanying array of gears, minifigures and various other parts...
-like sets of modules with one degree of freedom each. This allows robots to be designed using ANAT modules with n° of freedom. Configurations range from mobile robots (ANATROLLER), manipulators (ANAT AMI-100), to walking robots (ANAT Walker).
PolyBot G3 (2002)
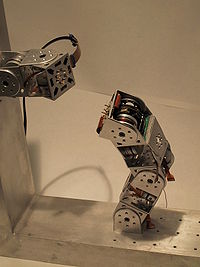
M-TRAN III (2005)
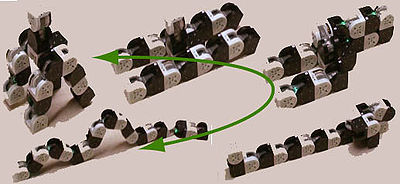
AMOEBA-I (2005)
AMOEBA-I, a three-module reconfigurable mobile robot was developed in Shenyang Institute of Automation (SIA), Chinese Academy of Sciences (CAS) by Liu J G et al.http://ieeexplore.ieee.org/xpls/abs_all.jsp?arnumber=1708645http://www.springerlink.com/content/m81820061n48jh32/.AMOEBA-I has nine kinds of non-isomorphic configurations and high mobility under unstructured environments.Four generations of its platform have been developed and a series of researches have been carried out on their reconfiguration mechanism, non-isomorphic configurations, tipover stability, and reconfiguration planning. Experiments have demonstrated that such kind structure permits good mobility and high flexibility to uneven terrain. Being hyper-redundant, modularized and reconfigurable, AMOEBA-I has many possible applications such as Urban Search and Rescue (USAR) and space exploration.
Ref_1: see http://ieeexplore.ieee.org/xpls/abs_all.jsp?arnumber=1708645;
Ref_2: see http://www.springerlink.com/content/m81820061n48jh32/
Stochastic-3D (2005)
High spatial resolution for arbitrary three-dimensional shape formation with modular robots can be accomplished using lattice system with large quantities of very small, prospectively microscopic modules. At small scales, and with large quantities of modules, deterministic control over reconfiguration of individual modules will become unfeasible, while stochastic mechanisms will naturally prevail. Microscopic size of modules will make the use of electromagnetic actuation and interconnection prohibitive, as well, as the use of on-board power storage.
Three large scale prototypes were built in attempt to demonstrate dynamically programmable three-dimensional stochastic reconfiguration in a neutral-buoyancy environment. The first prototype used electromagnets for module reconfiguration and interconnection. The modules were 100 mm cubes and weighed 0.81 kg. The second prototype used stochastic fluidic reconfiguration and interconnection mechanism. Its 130 mm cubic modules weighed 1.78 kg each and made reconfiguration experiments excessively slow. The current third implementation inherits the fluidic reconfiguration principle. The lattice grid size is 80 mm, and the reconfiguration experiments are under way. More information can be found at the CCSL Stochastic Modular Robotics webpage.
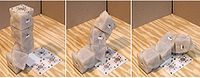
This chain self-reconfiguring system was built by the Cornell Computational Synthesis Lab to physically demonstrate artificial kinematic self-reproduction. Each module is a 0.65 kg cube with 100 mm long edges and one rotational degree of freedom. The axis of rotation is aligned with the cube's longest diagonal. Physical self-reproduction of a three- and a four-module robots was demonstrated. It was also shown that, disregarding the gravity constraints, an infinite number of self-reproducing chain meta-structures can be built from Molecubes. More information can be found at the CCSL Self-Replication webpage.
The Programmable Parts (2005)
The programmable parts are stirred randomly on an air-hockey table by randomly actuated air jets. When they collide and stick, they can communicate and decide whether to stay stuck, or if and when to detach. Local interaction rules can be devised and optimized to guide the robots to make any desired global shape. More information can be found at the programmable parts web page.
SuperBot (2006)
The SuperBot modules fall into the chain/tree architecture. The modules have three degrees of freedom each. The design is based on two previous systems: Conro (by the same research group) and MTRAN (by Murata et al.). Each module can connect to another module through one of its six dock connectors. They can communicate and share power through their dock connectors. Several locomotion gaits have been developed for different arrangements of modules. For high-level communication the modules use hormone-based control, a distributed, scalable protocol that does not require the modules to have unique ID's.
Miche (2006)
The Miche system is a modular lattice system capable of arbitrary shape formation. Each module is an autonomous robot module capable of connecting to and communicating with its immediate neighbors. When assembled into a structure, the modules form a system that can be virtually sculpted using a computer interface and a distributed process. The group of modules collectively decide who is on the final shape and who is not using algorithms that minimize the information transmission and storage. Finally, the modules not in the structure let go and fall off under the control of an external force, in this case gravity.
More details at Miche (Rus et al.).
Roombots (2009)
Roombots have a hybrid chain/tree architecture. Each module has three degree of freedom, two of them using the diametrical axis within a regular cube, and a third (center) axis of rotation connecting the two spherical parts. All three axes are continuously rotatory. The outer Roombots DOF is using the same axis-orientation as Molecubes, the third, central Roombots axis enables the module to rotate its two outer DOF against each other. This novel feature enables a single Roombots module to locomote on flat terrain, but also to climb a wall, or to cross a concave, perpendicular edge. Convex edges require the assembly of at least two modules into a Roombots "Metamodule". Each module has ten available connector slots, currently two of them are equipped with an active connection mechanism based on mechanical latches.
Roombots are designed for two tasks: to eventually shape objects of daily life, e.g. furniture, and to locomote, e.g. as a quadruped or a tripod robot made from multiple modules.
More information can be found at Biorobotics Laboratory Roombots webpage.
Quantitative accomplishment
- The robot with most active modules has 56 units
- The smallest actuated modular unit has a size of
mm - The largest actuated modular unit (by volume) has the size of 8 m^3 <(GHFC)giant helium filled catoms, CMU>
- The strongest actuation modules are able to lift 5 identical horizontally cantilevered units.
- The fastest modular robot can move at 23 unit-sizes/second.
- The largest simulated system contained many 100,000's of units.
Challenges, solutions, and opportunities
Since the early demonstrations of early modular self-reconfiguring systems, the size, robustness and performance has been continuously improving. In parallel, planning and control algorithms have been progressing to handle thousands of units. There are, however, several key steps that are necessary for these systems to realize their promise of adaptability, robustness and low cost. These steps can be broken down into challenges in the hardware design, in planning and control algorithms and in application. These challenges are often intertwined.Hardware design challenges
The extent to which the promise of self-reconfiguring robotic systems can be realized depends critically on the numbers of modules in the system. To date, only systems with up to about 50 units have been demonstrated, with this number stagnating over almost a decade. There are a number of fundamental limiting factors that govern this number:- Limits on strength, precision, and field robustness (both mechanical and electrical) of bonding/docking interfaces between modules
- Limits on motor power, motion precision and energetic efficiency of units, (i.e. specific power, specific torque)
- Hardware/software design. Hardware that is designed to make the software problem easier. Self-reconfiguring systems have more tightly coupled hardware and software than any other existing system.
Planning and control challenges
Though algorithms have been developed for handling thousands of units in ideal conditions, challenges to scalability remain both in low-level control and high-level planning to overcome realistic constraints:- Algorithms for parallel-motion for large scale manipulation and locomotion
- Algorithms for robustly handling a variety of failure modes, from misalignments, dead-units (not responding, not releasing) to units that behave erratically.
- Algorithms that determine the optimal configuration for a given task
- Algorithms for optimal (time, energy) reconfiguration plan
- Efficient and scalable (asynchronous) communication among multiple units
Application challenges
Though the advantages of Modular self-reconfiguring robotic systems is largely recognized, it has been difficult to identify specific application domains where benefits can be demonstrated in the short term. Some suggested applications are- Space explorationSpace explorationSpace exploration is the use of space technology to explore outer space. Physical exploration of space is conducted both by human spaceflights and by robotic spacecraft....
and Space colonizationSpace colonizationSpace colonization is the concept of permanent human habitation outside of Earth. Although hypothetical at the present time, there are many proposals and speculations about the first space colony...
applications, e.g. Lunar colonization - Construction of large architectural systems
- Deep sea exploration/mining
- Search and rescue in unstructured environments
- Rapid construction of arbitrary tools under space/weight constraints
- Disaster relief shelters for displaced peoples
- Shelters for impoverished areas which require little on-the-ground expertise to assemble
Grand Challenges
Several robotic fields have identified ‘’Grand Challenges’’ that act as a catalyst for development and serve as a short-term goal in absence of immediate ‘’killer apps’’. The Grand Challenge is not in itself a research agenda or milestone, but a means to stimulate and evaluate coordinated progress across multiple technical frontiers. Several Grand Challenges have been proposed for the modular self-reconfiguring robotics field:- Demonstration of a system with >1000 units. Physical demonstration of such a system will inevitably require rethinking key hardware and algorithmic issues, as well as handling noise and error.
- Robosphere. A self-sustaining robotic ecology, isolated for a long period of time (1 year) that needs to sustain operation and accomplish unforeseen tasks without any human presence.
- Self replication A system with many units capable of self replication by collecting scattered building blocks will require solving many of the hardware and algorithmic challenges.
- Ultimate Construction A system capable of making objects out of the components of, say, a wall.
- Biofilter analogy If the system is ever made small enough to be injected into a mammal, one task may be to monitor molecules in the blood stream and allow some to pass and others not to, somewhat like the Blood-brain barrierBlood-brain barrierThe blood–brain barrier is a separation of circulating blood and the brain extracellular fluid in the central nervous system . It occurs along all capillaries and consists of tight junctions around the capillaries that do not exist in normal circulation. Endothelial cells restrict the diffusion...
. As a challenge, an analogy may be made where system must be able to:- be inserted into a hole one module’s diameter.
- travel some specified distance in a channel that is say roughly 40 x 40 module diameters in area.
- form a barrier fully conforming to the channel (whose shape is non-regular, and unknown beforehand).
- allow some objects to pass and others not to (not based on size).
- Since sensing is not the emphasis of this work, the actual detection of the passable objects should be made trivial.
Inductive Transducers
A unique potential solution that can be exploited is the use of inductors as transducers. This could be useful for dealing with docking and bonding problems. At the same time it could also be beneficial for its capabilities of docking detection (alignment and finding distance), power transmission, and (data signal) communication. A proof-of-concept video can be seenhere. The rather limited exploration down this avenue is probably a consequence of the historical lack of need in any applications for such an approach.