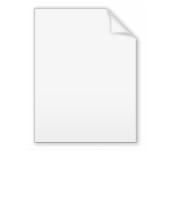
Lean services
Encyclopedia
Lean services is the application of the lean manufacturing
concept to service operations. It is distinct in that Lean services are not concerned with the making of ‘hard’ products.
To date, Lean principles of Continuous Improvement
and Respect for People have been applied to call center services, health care, higher education, software development, and public and professional services. Conceptually, these implementations follow very similar routes to those in manufacturing settings, and very often make use of the same tools and techniques. There are, however, many significant distinctions.
It is important not to confuse 'service operations' with the economic definition of service sectors (as distinct from manufacturing sectors), since many ‘service sector’ organisations have manufacturing-like operations in that they produce regular outputs along value streams.
Instead, ‘service’ refers to the ‘service concept’ or ‘product service bundle’, which are all the activities that provide value to the customer along a value stream.
(see Lean manufacturing
). Lean in the Service sector is subject itself to continuous improvement, and as such there are an increasing number of concepts that may or may not be included as part of Lean Service.
, the father of the Toyota Production System
. These wastes have been often been redefined to better fit new organisations, industries, or external pressures.
One redefinition of these wastes for service operations by Bicheno and Holweg (2009) is as follows:
Rule 1: All work shall be highly specified as to content, sequence, timing, and outcome.
Rule 2: Every customer-supplier connection must be direct, and there must be an unambiguous yes or no way to send requests and receive responses.
Rule 3: The pathway for every product and service must be simple and direct.
Rule 4: Any improvement must be made in accordance with the scientific method, under the guidance of a teacher, at the lowest possible level in the organization.
Value Demand is the demand for service from customers, while Failure Demand is the demand caused by a failure to do something right for the customer. Failure demand is thus demand that only exists because initial demand was not satisfied properly. For example, a large proportion of calls that call centers receive are either chasing down enquiries made earlier, or to correct earlier work that was not done properly. As one of the key aims of "Lean" is to eliminate waste, Failure Demand represents an obvious type of waste in service organizations.
Failure demand
can also be defined as "the delivery or production of products and services downstream as a result of defects in the system upstream."(Shillingburg, 2011) This would include administrative rework, audits, inspections and enquires. This non value-added work can account for the majority of administrative work performed.
By treating failure and value demand alike in statistical analysis, failure demand can give the quite false impression of greater productivity. This merely reinforces the need to look at what is really going on, and ask why the service is being rendered.
. One of the earliest and most successful adopters of this is Honeywell
, which calls its program Six Sigma Plus. Like some other major practitioners, GE has developed a very rigorous Lean Six Sigma training program in which certain employees are chosen to become certified in this area.
(visiting professor Sheffield University) has been especially vocal and critical of lean in his paper 'Rethinking Lean Service' http://www.thesystemsthinkingreview.co.uk/images/ARTICLE/john_rethinking_lean_service.pdf
The application of Lean Tools and techniques has led to serious problems in many service organisations, including Her Majesty's Revenue and Customs (HMRC) and even Starbucks.
Proponents of Lean Service, however, suggest that these criticisms are a response to Lean implementations that have failed to properly understand Lean as a holistic, action based management and implementation system to provide enhanced customer value, a "Tools" mentality instead of an outcomes orientation and an inadequate knowledge of how to utilize and adapt Lean Manufacturing methods to the service environment.
Lean manufacturing
Lean manufacturing, lean enterprise, or lean production, often simply, "Lean," is a production practice that considers the expenditure of resources for any goal other than the creation of value for the end customer to be wasteful, and thus a target for elimination...
concept to service operations. It is distinct in that Lean services are not concerned with the making of ‘hard’ products.
To date, Lean principles of Continuous Improvement
Continuous Improvement Process
A continuous improvement process is an ongoing effort to improve products, services, or processes. These efforts can seek "incremental" improvement over time or "breakthrough" improvement all at once...
and Respect for People have been applied to call center services, health care, higher education, software development, and public and professional services. Conceptually, these implementations follow very similar routes to those in manufacturing settings, and very often make use of the same tools and techniques. There are, however, many significant distinctions.
Understanding of service
'Service’ in this context is not limited to ‘the office’ or ‘administration’ that have been the focus of several publications, but also wider service situations that are not necessarily repetitive, where ‘takt’ time is not applicable, and where task times may be both long and variable. Service in this context could mean anything from a hospital to a university, from an office process to a consultancy, and from a warehouse to field service maintenance.It is important not to confuse 'service operations' with the economic definition of service sectors (as distinct from manufacturing sectors), since many ‘service sector’ organisations have manufacturing-like operations in that they produce regular outputs along value streams.
Instead, ‘service’ refers to the ‘service concept’ or ‘product service bundle’, which are all the activities that provide value to the customer along a value stream.
Aspects of Lean service
Lean Service has its origin in the Toyota Production SystemToyota Production System
The Toyota Production System is an integrated socio-technical system, developed by Toyota, that comprises its management philosophy and practices. The TPS organizes manufacturing and logistics for the automobile manufacturer, including interaction with suppliers and customers...
(see Lean manufacturing
Lean manufacturing
Lean manufacturing, lean enterprise, or lean production, often simply, "Lean," is a production practice that considers the expenditure of resources for any goal other than the creation of value for the end customer to be wasteful, and thus a target for elimination...
). Lean in the Service sector is subject itself to continuous improvement, and as such there are an increasing number of concepts that may or may not be included as part of Lean Service.
The service wastes
The original seven wastes (Muda (Japanese term)) were defined by Taiichi OhnoTaiichi Ohno
was a prominent Japanese businessman. He is considered to be the father of the Toyota Production System, which became Lean Manufacturing in the U.S. He devised the seven wastes as part of this system. He wrote several books about the system, including Toyota Production System: Beyond Large-Scale...
, the father of the Toyota Production System
Toyota Production System
The Toyota Production System is an integrated socio-technical system, developed by Toyota, that comprises its management philosophy and practices. The TPS organizes manufacturing and logistics for the automobile manufacturer, including interaction with suppliers and customers...
. These wastes have been often been redefined to better fit new organisations, industries, or external pressures.
One redefinition of these wastes for service operations by Bicheno and Holweg (2009) is as follows:
- 1. Delay on the part of customers waiting for service, for delivery, in queues, for response, not arriving as promised. The customer’s time may seem free to the provider, but when she takes custom elsewhere the pain begins.
- 2. Duplication. Having to re-enter data, repeat details on forms, copy information across, answer queries from several sources within the same organisation.
- 3. Unnecessary Movement. Queuing several times, lack of one-stop, poor ergonomics in the service encounter.
- 4. Unclear communication, and the wastes of seeking clarification, confusion over product or service use, wasting time finding a location that may result in misuse or duplication.
- 5. Incorrect inventory. Being out-of-stock, unable to get exactly what was required, substitute products or services.
- 6. An opportunity lost to retain or win customers, a failure to establish rapport, ignoring customers, unfriendliness, and rudeness.
- 7. Errors in the service transaction, product defects in the product-service bundle, lost or damaged goods.
Bowen & Spear's 4 principles
For Lean to be successful, HBS professor Kent Bowen and Steven Spear (HBS DBA '99) have defined a framework of 4 principles, based on the Toyota Production System :Rule 1: All work shall be highly specified as to content, sequence, timing, and outcome.
Rule 2: Every customer-supplier connection must be direct, and there must be an unambiguous yes or no way to send requests and receive responses.
Rule 3: The pathway for every product and service must be simple and direct.
Rule 4: Any improvement must be made in accordance with the scientific method, under the guidance of a teacher, at the lowest possible level in the organization.
Value Demand and Failure Demand
One of the central concepts that distinguishes lean services from lean manufacturing is the distinction between Value Demand and Failure Demand (Seddon, 2003).Value Demand is the demand for service from customers, while Failure Demand is the demand caused by a failure to do something right for the customer. Failure demand is thus demand that only exists because initial demand was not satisfied properly. For example, a large proportion of calls that call centers receive are either chasing down enquiries made earlier, or to correct earlier work that was not done properly. As one of the key aims of "Lean" is to eliminate waste, Failure Demand represents an obvious type of waste in service organizations.
Failure demand
Failure demand
Failure demand is a systems concept used in service organisations first discovered and articulated by Professor John Seddon as 'demand caused by a failure to do something or do something right for the customer'...
can also be defined as "the delivery or production of products and services downstream as a result of defects in the system upstream."(Shillingburg, 2011) This would include administrative rework, audits, inspections and enquires. This non value-added work can account for the majority of administrative work performed.
By treating failure and value demand alike in statistical analysis, failure demand can give the quite false impression of greater productivity. This merely reinforces the need to look at what is really going on, and ask why the service is being rendered.
Lean Six Sigma
In recent years, some major practitioners have combined Lean and Six Sigma principles to yield a methodology commonly known as Lean Six SigmaLean Six Sigma
In recent years, some practitioners have combined Six Sigma ideas with lean manufacturing to yield a methodology named Lean Six Sigma. Lean manufacturing – addressing process flow and waste issues – and Six Sigma, with its focus on variation and design, are viewed as complementary disciplines in...
. One of the earliest and most successful adopters of this is Honeywell
Honeywell
Honeywell International, Inc. is a major conglomerate company that produces a variety of consumer products, engineering services, and aerospace systems for a wide variety of customers, from private consumers to major corporations and governments....
, which calls its program Six Sigma Plus. Like some other major practitioners, GE has developed a very rigorous Lean Six Sigma training program in which certain employees are chosen to become certified in this area.
Criticisms of Lean service
More recently it is being argued that the application of lean manufacturing tools and techniques have seriously damaged the service organisations that Lean has been applied to. John SeddonJohn Seddon
John Seddon is a British occupational psychologist, author and "management guru", specialising in the service industry. He is lead consultant of Vanguard, a consultancy company he formed in 1985 and the inventor of 'The Vanguard Method'....
(visiting professor Sheffield University) has been especially vocal and critical of lean in his paper 'Rethinking Lean Service' http://www.thesystemsthinkingreview.co.uk/images/ARTICLE/john_rethinking_lean_service.pdf
The application of Lean Tools and techniques has led to serious problems in many service organisations, including Her Majesty's Revenue and Customs (HMRC) and even Starbucks.
5S in the office
5S has been widely and successfully applied in office environments, however this has received some criticism for resulting in workplaces that are too clinical or impersonal. Service Lean leader Debashis Sarkar has done pioneering work in the space of application of 5S to improve performance of a large financial conglomerate which can be read in his book referenced later.Application of Lean in creative environments
Critics of Lean Service have suggested that problems arise when companies try to apply "Lean principles" to areas where creativity, ability to react to rapid external changes, need to spend an extensive amount of time to convince external parties (typically lobbying) or ability to successfully negotiate are needed; and that the downsides of Lean are reduced / eliminated creativity and ability to cope with the unexpected.Proponents of Lean Service, however, suggest that these criticisms are a response to Lean implementations that have failed to properly understand Lean as a holistic, action based management and implementation system to provide enhanced customer value, a "Tools" mentality instead of an outcomes orientation and an inadequate knowledge of how to utilize and adapt Lean Manufacturing methods to the service environment.
See also
- Lean manufacturingLean manufacturingLean manufacturing, lean enterprise, or lean production, often simply, "Lean," is a production practice that considers the expenditure of resources for any goal other than the creation of value for the end customer to be wasteful, and thus a target for elimination...
- Lean constructionLean constructionLean Construction is a combination of original research and development in design and construction with an adaption of lean manufacturing principles and practices to the end-to-end design and construction process. Unlike manufacturing, construction is a project based-production process...
- Lean ITLean ITLean IT is the extension of lean manufacturing and lean services principles to the development and management of information technology products and services...
- Lean accountingLean accountingThe purpose of Lean Accounting is to support the lean enterprise as a business strategy. It seeks to move from traditional accounting methods to a system that measures and motivates excellent business practices in the lean enterprise.- Introduction :...
- Lean GovernmentLean GovernmentLean Government refers to the application of Lean production principles and methods to identify and implement the most efficient and value added way to provide government services. Government agencies have found that Lean methods enable them to better understand how their processes work, to...
- Lean Higher EducationLean Higher EducationLean Higher Education is the application of the Lean management to Higher Education both in administration and academic activities . Today, the application of Lean management in higher education is most prevalent in administrative activities...