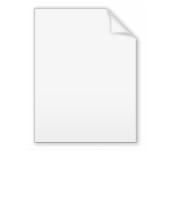
Full-mold casting
Encyclopedia
Full-mold casting is a evaporative-pattern casting
process which is a combination of sand casting
and lost-foam casting
. It uses a expanded polystyrene foam pattern
which is then surrounded by sand, much like sand casting. The metal is then poured directly into the mold, which vaporizes the foam upon contact.
. If the volume is large, then the pattern can be mass-produced by a process similar to injection molding
. Pre-expanded beads of polystyrene are injected into a preheated aluminium mold at low pressure. Steam
is then applied to the polystyrene which causes it to expand more to fill the die. The final pattern is approximately 97.5% air and 2.5% polystyrene. Once the pattern is made pre-made pouring basins, runners, and risers
can be hot glue
d to form the final pattern.
The pattern is then coated with a refractory material. The coated pattern is then placed in a flask and packed carefully with green sand
or a chemically bonded sand. Finally, the molten metal is poured into the mold, which vaporizes the foam allowing the metal to fill the entire mold. The casting is allowed to cool and then dumped out of the flask ready to use. The sand does not need to be reprocessed so it can be directly reused.
. The size range is from 400 gram to several tonnes (tons).
Full-mold casting is often used to produce cylinder head
s, engine blocks, pump
housings, automotive brake
components, and manifold
s. Commonly employed materials include aluminium
, iron
, steel
, nickel alloys, and copper alloys.
, and has no parting lines so no flash is formed. As compared to investment casting, it is cheaper because it is a simpler process and the foam is cheaper than the wax. Risers are not usually required due to the nature of the process; because the molten metal vaporizes the foam the first metal into the mold cools more quickly than the rest, which results in natural directional solidification
.
The two main disadvantages are that pattern costs can be high for low volume applications and the patterns are easily damaged or distorted due to their low strength. If a die is used to create the patterns there is a large initial cost.
Evaporative-pattern casting
Evaporative-pattern casting is a type of casting process that uses a pattern made from a material that will evaporate when the molten metal is poured into the molding cavity...
process which is a combination of sand casting
Sand casting
Sand casting, also known as sand molded casting, is a metal casting process characterized by using sand as the mold material.It is relatively cheap and sufficiently refractory even for steel foundry use. A suitable bonding agent is mixed or occurs with the sand...
and lost-foam casting
Lost-foam casting
Lost-foam casting is a type of evaporative-pattern casting process that is similar to investment casting except foam is used for the pattern instead of wax...
. It uses a expanded polystyrene foam pattern
Pattern (casting)
In casting, a pattern is a replica of the object to be cast, used to prepare the cavity into which molten material will be poured during the casting process.Patterns used in sand casting may be made of wood, metal, plastics or other materials...
which is then surrounded by sand, much like sand casting. The metal is then poured directly into the mold, which vaporizes the foam upon contact.
Process
First, a pattern is made from polystyrene foam, which can be done many different ways. For small volume runs the pattern can be hand cut or machined from a solid block of foam; if the geometry is simple enough it can even be cut using a hot-wire foam cutterHot-wire foam cutter
A hot-wire foam cutter is a tool used to cut polystyrene foam and similar materials. The device consists of a thin, taut metal wire, often made of nichrome or stainless steel, or a thicker wire preformed into a desired shape, which is heated via electrical resistance to approximately 200°C...
. If the volume is large, then the pattern can be mass-produced by a process similar to injection molding
Injection molding
Injection molding is a manufacturing process for producing parts from both thermoplastic and thermosetting plastic materials. Material is fed into a heated barrel, mixed, and forced into a mold cavity where it cools and hardens to the configuration of the cavity...
. Pre-expanded beads of polystyrene are injected into a preheated aluminium mold at low pressure. Steam
Steam
Steam is the technical term for water vapor, the gaseous phase of water, which is formed when water boils. In common language it is often used to refer to the visible mist of water droplets formed as this water vapor condenses in the presence of cooler air...
is then applied to the polystyrene which causes it to expand more to fill the die. The final pattern is approximately 97.5% air and 2.5% polystyrene. Once the pattern is made pre-made pouring basins, runners, and risers
Riser (casting)
A riser, also known as a feeder, is a reservoir built into a metal casting mold to prevent cavities due to shrinkage. Most metals are less dense as a liquid than as a solid so castings shrink upon cooling, which can leave a void at the last point to solidify...
can be hot glue
Hot glue
Hot melt adhesive , also known as hot glue, is a form of thermoplastic adhesive that is commonly supplied in solid cylindrical sticks of various diameters, designed to be melted in an electric hot glue gun...
d to form the final pattern.
The pattern is then coated with a refractory material. The coated pattern is then placed in a flask and packed carefully with green sand
Green sand
Green sand may refer to:*Green sand , slightly damp sand, used in sand casting of metals*Greensand, a mineral containing glauconite*Olivine sand, which can form "green sand beaches"...
or a chemically bonded sand. Finally, the molten metal is poured into the mold, which vaporizes the foam allowing the metal to fill the entire mold. The casting is allowed to cool and then dumped out of the flask ready to use. The sand does not need to be reprocessed so it can be directly reused.
Details
The minimum wall thickness for a full-mold casting is 2.5 mm (0.0984251968503937 in). Typical dimensional tolerances are 0.3% and typical surface finishes are from 2.5 to 25 µm (100 to 1000 µin) RMSRMS
-Science and technology:* Root mean square, a concept encapsulating the "average", in some sense, of a quantity. Frequently encountered in statistics, the physical sciences and electronics...
. The size range is from 400 gram to several tonnes (tons).
Full-mold casting is often used to produce cylinder head
Cylinder head
In an internal combustion engine, the cylinder head sits above the cylinders on top of the cylinder block. It closes in the top of the cylinder, forming the combustion chamber. This joint is sealed by a head gasket...
s, engine blocks, pump
Pump
A pump is a device used to move fluids, such as liquids, gases or slurries.A pump displaces a volume by physical or mechanical action. Pumps fall into three major groups: direct lift, displacement, and gravity pumps...
housings, automotive brake
Brake
A brake is a mechanical device which inhibits motion. Its opposite component is a clutch. The rest of this article is dedicated to various types of vehicular brakes....
components, and manifold
Manifold
In mathematics , a manifold is a topological space that on a small enough scale resembles the Euclidean space of a specific dimension, called the dimension of the manifold....
s. Commonly employed materials include aluminium
Aluminium
Aluminium or aluminum is a silvery white member of the boron group of chemical elements. It has the symbol Al, and its atomic number is 13. It is not soluble in water under normal circumstances....
, iron
Iron
Iron is a chemical element with the symbol Fe and atomic number 26. It is a metal in the first transition series. It is the most common element forming the planet Earth as a whole, forming much of Earth's outer and inner core. It is the fourth most common element in the Earth's crust...
, steel
Steel
Steel is an alloy that consists mostly of iron and has a carbon content between 0.2% and 2.1% by weight, depending on the grade. Carbon is the most common alloying material for iron, but various other alloying elements are used, such as manganese, chromium, vanadium, and tungsten...
, nickel alloys, and copper alloys.
Advantages and disadvantages
This casting process advantageous for very complex castings, that would regularly require cores. It is also dimensionally accurate, requires no draftDraft angle
In engineering, draft is the amount of taper for molded or cast parts perpendicular to the parting line. It can be measured in degrees or mm/mm ....
, and has no parting lines so no flash is formed. As compared to investment casting, it is cheaper because it is a simpler process and the foam is cheaper than the wax. Risers are not usually required due to the nature of the process; because the molten metal vaporizes the foam the first metal into the mold cools more quickly than the rest, which results in natural directional solidification
Directional solidification
Directional solidification and progressive solidification describe types of solidification within castings. Directional solidification describes solidification that occurs from farthest end of the casting and works its way towards the sprue...
.
The two main disadvantages are that pattern costs can be high for low volume applications and the patterns are easily damaged or distorted due to their low strength. If a die is used to create the patterns there is a large initial cost.