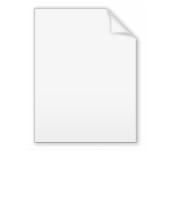
Formability
Encyclopedia
Formability is the ability of a given metal
workpiece to undergo plastic deformation without being damaged. The plastic deformation capacity of metal
lic materials, however, is limited to a certain extent.
Processes affected by the formability of a material include: rolling
, extrusion
, forging
, rollforming, stamping
, and hydroforming
of a material is the fracture
strain which is determined by a uniaxial tensile test (see also fracture toughness
). The strain identified by this test is defined by elongation with respect to a reference length (e. g. 80 mm for the standardized uniaxial test of flat specimens pursuant to EN 10002). It is important to note that deformation is homogeneous up to uniform elongation. Strain subsequently localizes until fracture occurs. Fracture strain is not an engineering strain since distribution of the deformation is inhomogeneous within the reference length. Fracture strain is nevertheless a rough indicator of the formability of a material. Typical values of the fracture strain are 7% for ultra-high-strength material and well over 50% for mild-strength steel.
A neck may appear at a certain forming stage. This is an indication of localized plastic deformation. Whereas more or less homogeneous deformation takes place in and around the subsequent neck location in the early stable deformation stage, almost all deformation is concentrated in the neck zone during the quasistable and instable deformation phase. This leads to material failure manifested by tearing. Forming limit curves depict the extreme but still possible deformation a sheet material may undergo during any stage of the stamping process. These limits depend on the deformation mode and the ratio of the surface strains. The major surface strain has a minimum value when plane strain deformation occurs, which means that the corresponding minor surface strain is zero. Forming limits are a specific material property. Typical plane strain values range from 10% for high-strength grades and 50% and above for mild-strength materials and those with very good formability.
, which is done by drawing a sheet by means of a punch tool pressing on the inner region of the sheet, whereas the side material held by a blankholder can be drawn toward the center. It has been observed that materials with outstanding deep drawability behave anisotropically (anisotropy
). Plastic deformation in the surface is much more pronounced than in the thickness. The lankford coefficient
( r ) is a specific material property indicating the ratio between width deformation and thickness deformation in the uniaxial tensile test. Materials with very good deep drawability have an r value of 2 and above. The positive aspect of formability with respect to the forming limit curve (forming limit diagram
) is seen in the deformation paths of the material that are concentrated in the extreme left of the diagram where the forming limits become very large.
). This may occur as a result of bending or shear deformation (inplane or through the thickness). The failure mechanism may be due to void nucleation and expansion on a microscopic level. Microcracks and subsequent macrocracks may appear when deformation of the material between the voids has exceeded the limit. Extensive research has focused in recent years on understanding and modeling ductile fracture. The approach has been to identify ductile forming limits using various small-scale tests that show different strain ratios or stress triaxialities. An effective measure of this type of forming limit is the minimum radius in roll-forming applications (half the sheet thickness for materials with good and three times the sheet thickness for materials with low formability).
) enhance and, in some cases, are indispensable to certain tool design processes (see also sheet metal forming analysis
).
Metal
A metal , is an element, compound, or alloy that is a good conductor of both electricity and heat. Metals are usually malleable and shiny, that is they reflect most of incident light...
workpiece to undergo plastic deformation without being damaged. The plastic deformation capacity of metal
Metal
A metal , is an element, compound, or alloy that is a good conductor of both electricity and heat. Metals are usually malleable and shiny, that is they reflect most of incident light...
lic materials, however, is limited to a certain extent.
Processes affected by the formability of a material include: rolling
Rolling
Rolling is a combination of rotation and translation of that object with respect to a surface , such that the two are in contact with each other without sliding. This is achieved by a rotational speed at the cylinder or circle of contact which is equal to the translational speed...
, extrusion
Extrusion
Extrusion is a process used to create objects of a fixed cross-sectional profile. A material is pushed or drawn through a die of the desired cross-section...
, forging
Forging
Forging is a manufacturing process involving the shaping of metal using localized compressive forces. Forging is often classified according to the temperature at which it is performed: '"cold," "warm," or "hot" forging. Forged parts can range in weight from less than a kilogram to 580 metric tons...
, rollforming, stamping
Stamping (metalworking)
Stamping includes a variety of sheet-metal forming manufacturing processes, such as punching using a machine press or stamping press, blanking, embossing, bending, flanging, and coining. This could be a single stage operation where every stroke of the press produce the desired form on the sheet...
, and hydroforming
Hydroforming
Hydroforming is a cost-effective way of shaping malleable metals such as aluminum or brass into lightweight, structurally stiff and strong pieces. One of the largest applications of hydroforming is the automotive industry, which makes use of the complex shapes possible by hydroforming to produce...
Fracture strain
A general parameter that indicates the formability and ductilityDuctility
In materials science, ductility is a solid material's ability to deform under tensile stress; this is often characterized by the material's ability to be stretched into a wire. Malleability, a similar property, is a material's ability to deform under compressive stress; this is often characterized...
of a material is the fracture
Fracture
A fracture is the separation of an object or material into two, or more, pieces under the action of stress.The word fracture is often applied to bones of living creatures , or to crystals or crystalline materials, such as gemstones or metal...
strain which is determined by a uniaxial tensile test (see also fracture toughness
Fracture toughness
In materials science, fracture toughness is a property which describes the ability of a material containing a crack to resist fracture, and is one of the most important properties of any material for virtually all design applications. The fracture toughness of a material is determined from the...
). The strain identified by this test is defined by elongation with respect to a reference length (e. g. 80 mm for the standardized uniaxial test of flat specimens pursuant to EN 10002). It is important to note that deformation is homogeneous up to uniform elongation. Strain subsequently localizes until fracture occurs. Fracture strain is not an engineering strain since distribution of the deformation is inhomogeneous within the reference length. Fracture strain is nevertheless a rough indicator of the formability of a material. Typical values of the fracture strain are 7% for ultra-high-strength material and well over 50% for mild-strength steel.
Forming limits for sheet forming
One main failure mode is caused by tearing of the material. This is typical for sheet forming applications.A neck may appear at a certain forming stage. This is an indication of localized plastic deformation. Whereas more or less homogeneous deformation takes place in and around the subsequent neck location in the early stable deformation stage, almost all deformation is concentrated in the neck zone during the quasistable and instable deformation phase. This leads to material failure manifested by tearing. Forming limit curves depict the extreme but still possible deformation a sheet material may undergo during any stage of the stamping process. These limits depend on the deformation mode and the ratio of the surface strains. The major surface strain has a minimum value when plane strain deformation occurs, which means that the corresponding minor surface strain is zero. Forming limits are a specific material property. Typical plane strain values range from 10% for high-strength grades and 50% and above for mild-strength materials and those with very good formability.
Deep drawability
A classic form of sheetforming is deep drawingDeep drawing
Deep drawing is a sheet metal forming process in which a sheet metal blank is radially drawn into a forming die by the mechanical action of a punch. It is thus a shape transformation process with material retention. The process is considered "deep" drawing when the depth of the drawn part exceeds...
, which is done by drawing a sheet by means of a punch tool pressing on the inner region of the sheet, whereas the side material held by a blankholder can be drawn toward the center. It has been observed that materials with outstanding deep drawability behave anisotropically (anisotropy
Anisotropy
Anisotropy is the property of being directionally dependent, as opposed to isotropy, which implies identical properties in all directions. It can be defined as a difference, when measured along different axes, in a material's physical or mechanical properties An example of anisotropy is the light...
). Plastic deformation in the surface is much more pronounced than in the thickness. The lankford coefficient
Lankford coefficient
The Lankford coefficient is a measure of the plastic anisotropy of a rolled sheet metal. This scalar quantity is used extensively as an indicator of the formability of recrystallized low-carbon steel sheets....
( r ) is a specific material property indicating the ratio between width deformation and thickness deformation in the uniaxial tensile test. Materials with very good deep drawability have an r value of 2 and above. The positive aspect of formability with respect to the forming limit curve (forming limit diagram
Forming limit diagram
A forming limit diagram, also known as a forming limit curve, is used in sheet metal forming for predicting forming behaviour of sheet metal. The diagram attempts to provide a graphical description of material failure tests, such as a punched dome test....
) is seen in the deformation paths of the material that are concentrated in the extreme left of the diagram where the forming limits become very large.
Ductility
Another failure mode that may occur without any tearing is ductile fracture after plastic deformation (ductilityDuctility
In materials science, ductility is a solid material's ability to deform under tensile stress; this is often characterized by the material's ability to be stretched into a wire. Malleability, a similar property, is a material's ability to deform under compressive stress; this is often characterized...
). This may occur as a result of bending or shear deformation (inplane or through the thickness). The failure mechanism may be due to void nucleation and expansion on a microscopic level. Microcracks and subsequent macrocracks may appear when deformation of the material between the voids has exceeded the limit. Extensive research has focused in recent years on understanding and modeling ductile fracture. The approach has been to identify ductile forming limits using various small-scale tests that show different strain ratios or stress triaxialities. An effective measure of this type of forming limit is the minimum radius in roll-forming applications (half the sheet thickness for materials with good and three times the sheet thickness for materials with low formability).
Use of formability parameters
Knowledge of the material formability is very important to the layout and design of any industrial forming process. Simulations using the finite-element method and use of formability criteria such as the forming limit curve (forming limit diagramForming limit diagram
A forming limit diagram, also known as a forming limit curve, is used in sheet metal forming for predicting forming behaviour of sheet metal. The diagram attempts to provide a graphical description of material failure tests, such as a punched dome test....
) enhance and, in some cases, are indispensable to certain tool design processes (see also sheet metal forming analysis
Sheet metal forming analysis
The technique of sheet metal forming analysis requires a non-contact optical 3D deformation measuring system. The system analyzes, calculates and documents deformations of sheet metal parts, for example. It provides the 3D coordinates of the component's surface as well as the distribution of...
).