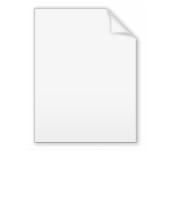
Eutectic bonding
Encyclopedia
Eutectic bonding, also referred to as eutectic soldering, describes a wafer bonding
Wafer bonding
Wafer bonding is a packaging technology on wafer-level for the fabrication of microelectromechanical systems , nanoelectromechanical systems , microelectronics and optoelectronics, ensuring a mechanically stable and hermetically sealed encapsulation...
technique with an intermediate metal layer. Those eutectic metals are alloys that transform directly from solid to liquid state at a specific composition and temperature without passing a two phase equilibrium, i.e. liquid and solid state.
Eutectic alloys are deposited by sputtering, dual source evaporation or electroplating. It also can be formed by diffusion reactions of pure materials and subsequently melting of the eutectic composition.
Eutectic bonding is able to produce hermetically sealed packages and electrical interconnection within a single process (compare ultrasonic images). In addition this procedure is conducting at low processing temperatures, low resultant stress induced in final assembly, high bonding strength, large fabrication yield and a good reliability. Those attributes are dependent on the coefficient of thermal expansion between the substrates.
The most important parameters for eutectic bonding are:
- bonding temperature
- bonding duration
- tool pressure
Overview =
Eutectic bonding is based on the ability of silicon (Si) to alloy with numerous metals and form an eutectic system. The most established eutectic formations are Si with gold (Au) or with aluminium (Al). This bonding procedure is most commonly used for Si or glass wafers that are coated with an Au/Al film and partly with adhesive layer (compare with following image).
The Si-Au compound has the advantages of a low eutectic temperature, a already widespread use in die bonding and the compatibility with Al interconnects. Additionally, often used eutectic alloys for wafer bonding in semiconductor fabrication are shown in the table. Choosing the correct alloy is determined by the processing temperature and compatibility of the materials used.
Eutectic alloy | Eutectic composition | Eutectic temperature |
---|---|---|
Au-In | 0.6 / 99.4 wt-% | 156 °C |
Cn-Sn | 5 / 95 wt-% | 231 °C |
Au-Sn | 80 / 20 wt-% | 280 °C |
Au-Ge | 28 / 72 wt-% | 361 °C |
Au-Si | 97.15 / 2.85 wt-% | 370 °C |
Al-Ge | 49 / 51 wt-% | 419 °C |
Al-Si | 87.5 / 12.5 wt-% | 580 °C |
Further, the bonding has less restrictions, concerning substrate roughness and planarity than direct bonding. Compared to anodic bonding, no high voltages are required that can be detrimental to electrostatic MEMS. Additionally, the eutectic bonding procedure promotes a better out-gassing and hermeticity than bonding with organic intermediate layers. Compared to glass frit bonding, the advantage sticks out that the reduction of seal ring geometries, an increase of the hermeticity levels and a shrinking of device size is possible. The geometry of eutectic seals is characterized by a thickness of 1 - 5 µm and a wideness of > 50 µm. The use of eutectic alloy brings the advantage of providing electrical conduction and interfacing with redistribution layers.
The temperature of the eutectic bonding procedure is dependent on the used material. The bonding happens at a specific weight-% and temperature, e.g. 370 °C at 2.85 wt-% Si for Au intermediate layer (compare to phase diagram).
The procedure of eutectic bonding is divided into following steps:
- Substrate processing
- Conditioning prior to bonding (e.g. oxide removal)
- Bonding process (Temperature, Mechanical Pressure for a few minutes)
- Cooling process
Pre-treatment
The surface preparation is the most important step to accomplish a successful eutectic bonding. This bonding procedure is due to oxide presence on the silicon substrates very limited based on the poor wettability of Au on the oxide layer. This leads to a poor adhesion of the eutectic bond. The oxide on the silicon surface acts as a diffusion barrier. The surface preparation's main task is to facilitate the deposition of the eutectic metal by oxide removal or adhesion layer deposition.To remove existing native oxide layers wet chemical etching (HF clean), dry chemical etching or chemical vapor deposition (CVD) with different types of crystals can be used. Also some applications require a surface pre-treatment using dry oxide removal processes, e.g. H2 plasma and CF4 plasma.
An additional method for the removal of unwanted surface films, i.e. oxide, is applying ultrasound during attachment process. As soon the tool is lowered a relative vibration between the wafer and the substrate is applied. Commonly, industrial bonders use ultrasonic with 60 Hz vibration frequencies and 100 µm vibration amplitude. A successful oxide removal results in a solid, hermetically tight connection.
A Second method to ensure the eutectic metal adheres on the Si wafer is by using an adhesion layer. This thin intermediate metal layer adheres well to the oxide and the eutectic metal. Well suitable metals for a Au-Si compound are titanium (Ti) and chromium (Cr) resulting in, e.g. Si-SiO2-Ti-Au or Si-SiO2-Cr-Au. The adhesion layer is used to break up the oxide by diffusion of silicon into the used material. A typical wafer is composed of a silicon wafer with oxide, 30 - 200 nm Ti or Cr layer and Au layer of > 500 nm thickness.
In the wafer fabrication a nickel (Ni) or a platinum (Pt) layer is added between the gold and the substrate wafer as diffusion barrier. The diffusion barrier avoids interaction between Au and Ti/Cr and requires higher temperatures to form a reliable and uniform bond. Further, the very limited solubility of silicon in titanium and chromium can prevent the developing of Au-Si eutectic composition based on the diffusion of silicon through titanium into gold.
The eutectic materials and optional adhesion layers are usually approached by deposition as alloy in one layer by dual component electroplating, dual-source evaporation (physical vapor deposition
Physical vapor deposition
Physical vapor deposition is a variety of vacuum deposition and is a general term used to describe any of a variety of methods to deposit thin films by the condensation of a vaporized form of the desired film material onto various workpiece surfaces...
) or composite alloy sputtering.
The removal of contamination, on the for silicon most established Au layer, is usually realized with water flushing and wafer heating.
Bonding process
The contacting of the substrates is applied directly after the pre-treatment of the surfaces to avoid oxide regeneration. The bonding procedure for oxidizing metals (not Au) generally takes place in a reduced atmosphere of 4 % hydrogen and an inert carrier gas flow, e.g. nitrogen. The requirements for the bonding equipment lies in the thermal and pressure uniformity across the wafer. This enables uniformly compressed seal lines.The substrate is aligned and fixed on a heated stage and the silicon wafer in a heated tool. The substrates inserted in the bonding chamber are contacted maintaining the alignment. As soon the layers are in atomic contact the reaction between those starts. To support the reaction mechanical pressure is applied and heating above the eutectic temperature is carried out.
The diffusivity and solubility of gold into silicon substrate increases with rising bonding temperatures. A higher temperature than the eutectic temperature is usually preferred for the bonding procedure. This may result in the formation of a thicker Au-Si alloy layer and further a stronger eutectic bond.
The diffusion starts as soon as the layers are in atomic contact at elevated temperatures. The contacted surface layer containing the eutectic composites melts, forming a liquid phase alloy, accelerating further mixing processes and diffusion until the saturation composition is reached.
The chosen bonding temperature usually is some degrees higher than the eutectic temperature so the melt becomes less viscous and readily flows due to higher roughness to surface areas that are not in atomic contact. To prevent the melt pressed outside the bonding interface the optimization of the bonding parameter control is necessary, e.g. low force on the wafers. Otherwise, it may lead to short circuits or device malfunctions of the used components (electrical and mechanical). The heating of the wafers leads to a change in the surface texture due to formation of fine silicon micro structures on top of the gold surface.
Cooling process
The material mix is solidified when the temperature decreases below eutectic point or the concentration ratio changes (for Si-Au: ). The solidification leads to epitaxial growth of silicon and gold on top of the silicon substrate resulting in numerous small silicon islands protruding from a polycrystalline gold alloy (compare to cross-section image of the bonding interface). This can result in bonding strengths around 70 MPa.The importance lies in the appropriate process parameters, i.e. sufficient bonding temperature control. Otherwise the bond cracks due to stress caused by a mismatch of the thermal expansion coefficient. This stress is able to relax over time.
Examples =
Based on the high bonding strength this procedure is special applicable for pressure sensors or fluidics. Also smart micro mechanical sensors and actuators with electronic and/or micro mechanical functions over multiple wafers can be fabricated.
Technical specifications =
Materials | Substrate:
Intermediate layer:
|
Temperature |
|
Advantages |
|
Drawbacks |
|
Researches |
|
See also =
- Wafer bondingWafer bondingWafer bonding is a packaging technology on wafer-level for the fabrication of microelectromechanical systems , nanoelectromechanical systems , microelectronics and optoelectronics, ensuring a mechanically stable and hermetically sealed encapsulation...
- Direct bondingDirect bondingDirect bonding describes a wafer bonding process without any additional intermediate layers. The bonding process is based on chemical bonds between two surfaces of any material possible meeting numerous requirements....
- Plasma activated bondingPlasma activated bondingPlasma activated bonding is a derivative, directed to lower processing temperatures for direct bonding with hydrophilic surfaces. The main requirements for lowering temperatures of direct bonding are the use of materials melting at low temperatures and with different coefficients of thermal...
- Anodic bondingAnodic bondingAnodic bonding is a wafer bonding procedure without any intermediate layer. This bonding technique, also known as field assisted bonding or electrostatic sealing, is mostly used for connecting silicon/glass and metal/glass through electric fields...
- Adhesive bondingAdhesive bondingAdhesive bonding describes a wafer bonding technique with applying an intermediate layer to connect substrates of different materials. These produced connections can be soluble or insoluble. The commercially available adhesive can be organic or inorganic and is deposited on one or both substrate...
- Glass frit bondingGlass frit bondingGlass frit bonding, also referred to as glass soldering or seal glass bonding, describes a wafer bonding technique with an intermediate glass layer. It is a widely used encapsulation technology for surface micro-machined structures, i.e. accelerometers or gyroscopes. This technique utilizes low...
- Thermocompression bondingThermocompression bondingThermocompression bonding describes a wafer bonding technique and is also referred to as diffusion bonding, pressure joining, thermocompression welding or solid-state welding. Two metals, e.g. gold -gold , are brought into atomic contact applying force and heat simultaneously. The diffusion...
- Reactive bondingReactive bondingReactive bonding describes a wafer bonding procedure using highly reactive nanoscale multilayer systems as an intermediate layer between the bonding substrates. The multilayer system consists of two alternating different thin metallic films. The self-propagating exothermic reaction within the...
- Measurement and characterization for wafer level packaging technologiesBond characterizationThe wafer bond characterization is based on different methods and tests. Considered a high importance of the wafer are the successful bonded wafers without flaws. Those flaws can be caused by void formation in the interface due to unevenness or impurities...
External links =