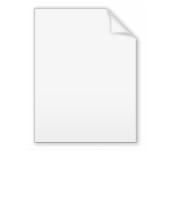
Direct metal laser sintering
Encyclopedia
Direct metal laser sintering (DMLS) is an additive metal fabrication technology developed by EOS
out of Munich, Germany, sometimes also referred to by the terms selective laser sintering
(SLS) or selective laser melting
(SLM). The process involves use of a 3D CAD model whereby a .stl
file is created and sent to the machine’s software. A technician works with this 3D model to properly orient the geometry for part building and adds supports structure as appropriate. Once this "build file" has been completed, it is "sliced" into the layer thickness the machine will build in and downloaded to the DMLS machine allowing the build to begin. The DMLS machine uses a high-powered 200 watt Yb-fiber optic laser
. Inside the build chamber area, there is a material dispensing platform and a build platform along with a recoater blade used to move new powder over the build platform. The technology fuses metal
powder into a solid part by melting it locally using the focused laser beam. Parts are built up additively layer by layer, typically using layers 20 micrometres thick. This process allows for highly complex geometries to be created directly from the 3D CAD data, fully automatically, in hours and without any tooling. DMLS is a net-shape process, producing parts with high accuracy and detail resolution, good surface quality and excellent mechanical properties.
s, prototypes can now be functional hardware made out of the same material as production components.
DMLS is also one of the few additive manufacturing technologies being used in production. Since the components are built layer by layer, it is possible to design internal features and passages that could not be cast or otherwise machined. Complex geometries and assemblies with multiple components can be simplified to fewer parts with a more cost effective assembly. DMLS does not require special tooling like casting
s, so it is convenient for short production runs.
For production tooling, material density of a finished part or insert should be addressed prior to use. For example, in injection molding inserts, any surface imperfections will cause imperfections in the plastic part, and the inserts will have to mate with the base of the mold with temperature and surfaces to prevent problems.
In this process metallic support structure removal and post processing of the part generated is a time consuming process and requires use of EDM and/or grinding machines having the same level of accuracy provided by the RP machine.
When using rapid prototyping machines, .stl files, which do not include anything but raw mesh data in binary (generated from Solid Works / Catia, and other major CAD programs) need further conversion to .cli & .sli files (the format required for non stereolithography machines). Software converts .stl file to .sli files, as with the rest of the process, there can be costs associated with this step.
, maraging steel
, cobalt
chromium
, inconel
625 and 718, and titanium
Ti6Alv4. Theoretically, almost any alloy metal can be used in this process once fully developed and validated.
EOS (company)
EOS GmbH, or EOS, Electro Optical Systems, is a major manufacturer of SLS and DMLS laser sintering systems, based in Krailling, Germany. Its revenues exceed 60 million Euros, and employs 300 people worldwide...
out of Munich, Germany, sometimes also referred to by the terms selective laser sintering
Selective laser sintering
Selective laser sintering is an additive manufacturing technique that uses a high power laser to fuse small particles of plastic, metal , ceramic, or glass powders into a mass that has a desired 3-dimensional shape...
(SLS) or selective laser melting
Selective Laser melting
Selective laser melting is an additive manufacturing process that uses 3D CAD data as a digital information source and energy in the form of a high powered laser beam to create three-dimensional metal parts by fusing fine metallic powders together...
(SLM). The process involves use of a 3D CAD model whereby a .stl
STL (file format)
STL is a file format native to the stereolithography CAD software created by 3D Systems. This file format is supported by many other software packages; it is widely used for rapid prototyping and computer-aided manufacturing. STL files describe only the surface geometry of a three dimensional...
file is created and sent to the machine’s software. A technician works with this 3D model to properly orient the geometry for part building and adds supports structure as appropriate. Once this "build file" has been completed, it is "sliced" into the layer thickness the machine will build in and downloaded to the DMLS machine allowing the build to begin. The DMLS machine uses a high-powered 200 watt Yb-fiber optic laser
Laser
A laser is a device that emits light through a process of optical amplification based on the stimulated emission of photons. The term "laser" originated as an acronym for Light Amplification by Stimulated Emission of Radiation...
. Inside the build chamber area, there is a material dispensing platform and a build platform along with a recoater blade used to move new powder over the build platform. The technology fuses metal
Metal
A metal , is an element, compound, or alloy that is a good conductor of both electricity and heat. Metals are usually malleable and shiny, that is they reflect most of incident light...
powder into a solid part by melting it locally using the focused laser beam. Parts are built up additively layer by layer, typically using layers 20 micrometres thick. This process allows for highly complex geometries to be created directly from the 3D CAD data, fully automatically, in hours and without any tooling. DMLS is a net-shape process, producing parts with high accuracy and detail resolution, good surface quality and excellent mechanical properties.
Benefits
DMLS has many benefits over traditional manufacturing techniques. Speed is the most obvious because no special tooling is required and parts can be built in a matter of hours. Additionally, DMLS allows for more rigorous testing of prototypes. Since DMLS can use most alloyAlloy
An alloy is a mixture or metallic solid solution composed of two or more elements. Complete solid solution alloys give single solid phase microstructure, while partial solutions give two or more phases that may or may not be homogeneous in distribution, depending on thermal history...
s, prototypes can now be functional hardware made out of the same material as production components.
DMLS is also one of the few additive manufacturing technologies being used in production. Since the components are built layer by layer, it is possible to design internal features and passages that could not be cast or otherwise machined. Complex geometries and assemblies with multiple components can be simplified to fewer parts with a more cost effective assembly. DMLS does not require special tooling like casting
Casting
In metalworking, casting involves pouring liquid metal into a mold, which contains a hollow cavity of the desired shape, and then allowing it to cool and solidify. The solidified part is also known as a casting, which is ejected or broken out of the mold to complete the process...
s, so it is convenient for short production runs.
Applications
This technology is used to manufacture direct parts for a variety of industries including aerospace, dental, medical and other industries that have small to medium size, highly complex parts and the tooling industry to make direct tooling inserts. With a build envelop of 250 x 250 x 185 mm, and the ability to ‘grow’ multiple parts at one time, DMLS is a very cost and time effective technology. The technology is used both for rapid prototyping, as it decreases development time for new products, and production manufacturing as a cost saving method to simplify assemblies and complex geometries.Constraints
The aspects of size, feature details and surface finish, as well as print through error in the Z axis may be factors that should be considered prior to the use of the technology. However, by planning the build in the machine where most features are built in the x and y axis as the material is laid down, the feature tolerances can be managed well. Surfaces usually have to be polished to achieve mirror or extremely smooth finishes.For production tooling, material density of a finished part or insert should be addressed prior to use. For example, in injection molding inserts, any surface imperfections will cause imperfections in the plastic part, and the inserts will have to mate with the base of the mold with temperature and surfaces to prevent problems.
In this process metallic support structure removal and post processing of the part generated is a time consuming process and requires use of EDM and/or grinding machines having the same level of accuracy provided by the RP machine.
When using rapid prototyping machines, .stl files, which do not include anything but raw mesh data in binary (generated from Solid Works / Catia, and other major CAD programs) need further conversion to .cli & .sli files (the format required for non stereolithography machines). Software converts .stl file to .sli files, as with the rest of the process, there can be costs associated with this step.
Materials
Currently available alloys used in the process include 17-4 and 15-5 stainless steelStainless steel
In metallurgy, stainless steel, also known as inox steel or inox from French "inoxydable", is defined as a steel alloy with a minimum of 10.5 or 11% chromium content by mass....
, maraging steel
Maraging steel
Maraging steels are steels which are known for possessing superior strength and toughness without losing malleability, although they cannot hold a good cutting edge. Aging refers to the extended heat-treatment process...
, cobalt
Cobalt
Cobalt is a chemical element with symbol Co and atomic number 27. It is found naturally only in chemically combined form. The free element, produced by reductive smelting, is a hard, lustrous, silver-gray metal....
chromium
Chromium
Chromium is a chemical element which has the symbol Cr and atomic number 24. It is the first element in Group 6. It is a steely-gray, lustrous, hard metal that takes a high polish and has a high melting point. It is also odorless, tasteless, and malleable...
, inconel
Inconel
Inconel is a registered trademark of Special Metals Corporation that refers to a family of austenitic nickel-chromium-based superalloys. Inconel alloys are typically used in high temperature applications. It is often referred to in English as "Inco"...
625 and 718, and titanium
Titanium
Titanium is a chemical element with the symbol Ti and atomic number 22. It has a low density and is a strong, lustrous, corrosion-resistant transition metal with a silver color....
Ti6Alv4. Theoretically, almost any alloy metal can be used in this process once fully developed and validated.
See also
- 3D printing3D printing3D printing is a form of additive manufacturing technology where a three dimensional object is created by laying down successive layers of material. 3D printers are generally faster, more affordable, and easier to use than other additive manufacturing technologies. However, the term 3D printing is...
- Additive manufacturingAdditive manufacturingAdditive manufacturing is defined by ASTM as the "process of joining materials to make objects from 3D model data, usually layer upon layer, as opposed to subtractive manufacturing methodologies, such as traditional machining...
- Desktop manufacturing
- Digital fabricator
- Direct digital manufacturing
- Fab labFab labA fab lab is a small-scale workshop offering digital fabrication.A fab lab is generally equipped with an array of flexible computer controlled tools that cover several different length scales and various materials, with the aim to make "almost anything"...
- Fused deposition modelingFused deposition modelingFused deposition modeling is an additive manufacturing technology commonly used for modeling, prototyping, and production applications. The technology was developed by S...
- Instant manufacturing, also known as "direct manufacturing" or "on-demand manufacturing"
- Rapid manufacturing
- Rapid prototypingRapid prototypingRapid prototyping is the automatic construction of physical objects using additive manufacturing technology. The first techniques for rapid prototyping became available in the late 1980s and were used to produce models and prototype parts. Today, they are used for a much wider range of applications...
- RepRap ProjectRepRap ProjectThe RepRap project is an initiative to develop a 3D printer that can print most of its own components...
- Solid freeform fabrication
- StereolithographyStereolithographyStereolithography is an additive manufacturing technology for producing models, prototypes, patterns, and in some cases, production parts.-Technology description:...
External links
- Rapid Manufacturing's Role in the Factory of the Future
- Laser sintering - versatile production of tooling inserts, prototype parts and end products from metal powder Feature article available for free on ipmd.net