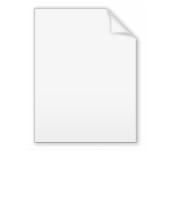
Articulated robot
Encyclopedia
An articulated robot is a robot with rotary joints (e.g. a legged robot
or an industrial robot
). Articulated robots can range from simple two-jointed structures to systems with 10 or more interacting joints.
They are powered by a variety of means, including electric motor
s.
Some types of robots, such as robotic arm
s, can be articulated or non-articulated.
See Figure. An articulated robot is one which uses rotary joints to access its work space.
Usually the joints are arranged in a “chain”, so that one joint supports another further in the chain.
Continuous Path:
A control scheme whereby the inputs or commands specify every point along a desired path of motion. The path is controlled by the coordinated motion of the manipulator joints.
Degrees Of Freedom (DOF):
The number of independent motions in which the end effector can move, defined by the number of axes of motion of the manipulator.
Gripper:
A device for grasping or holding, attached to the free end of the last manipulator link; also called the robot’s hand or end-effector.
Payload:
The maximum payload is the amount of weight carried by the robot manipulator at reduced speed while maintaining rated precision. Nominal payload is measured at maximum speed while maintaining rated precision. These ratings are highly dependent on the size and shape of the payload.
Pick And Place Cycle:
See Figure. Pick and place Cycle is the time, in seconds, to execute the following motion sequence: Move down one inch, grasp a rated payload; move up one inch; move across twelve inches; move down one inch; ungrasp; move up one inch; and return to start location.
Reach:
The maximum horizontal distance from the center of the robot base to the end of its wrist.
Accuracy:
See Figure. The difference between the point that a robot is trying to achieve and the actual resultant position. Absolute accuracy is the difference between a point instructed by the robot control system and the point actually achieved by the manipulator arm, while repeatability is the cycle-to-cycle variation of the manipulator arm when aimed at the same point.
Repeatability:
See Figure. The ability of a system or mechanism to repeat the same motion or achieve the same points when presented with the same control signals. The cycle-to-cycle error of a system when trying to perform a specific task
Resolution:
See Figure. The smallest increment of motion or distance that can be detected or controlled by the control system of a mechanism.
The resolution of any joint is a function of encoder pulses per revolution and drive ratio, and dependent on the distance between the tool center point and the joint axis.
Robot Program:
A robot communication program for IBM and compatible personal computers. Provides terminal emulation and utility functions. This program can record all of the user memory, and some of the system memory to disk files.
Maximum Speed:
The compounded maximum
speed of the tip of a robot moving at full extension with all joints moving simultaneously in complimentary directions. This speed is the theoretical maximum and should under no circumstances be used to estimate cycle time for a particular application. A better measure of real world speed is the standard twelve inch pick and place cycle time. For critical applications, the best indicator of achievable cycle time is a physical simulation.
Servo Controlled:
Controlled by a driving signal
which is determined by the error between the mechanism's present position and the desired output position.
Via Point:
A point through which the robot's tool should pass without stopping; via points are programmed in order to move beyond obstacles or to bring the arm into a lower inertia posture for part of the motion.
Work Envelope:
A three-dimensional
shape that defines the boundaries that the robot manipulator can reach; also known as reach envelope.
Legged robot
thumb|A [[Hexapod |hexapod robot]].Legged robots are a type of mobile robot. They are somewhat a recent innovation in robotics. However, many or all bipedal models are not practical seeing as they are cumbersome and slow. Most successful legged robots have 4 or 6 legs for further stability...
or an industrial robot
Industrial robot
An industrial robot is defined by ISO as an automatically controlled, reprogrammable, multipurpose manipulator programmable in three or more axes...
). Articulated robots can range from simple two-jointed structures to systems with 10 or more interacting joints.
They are powered by a variety of means, including electric motor
Electric motor
An electric motor converts electrical energy into mechanical energy.Most electric motors operate through the interaction of magnetic fields and current-carrying conductors to generate force...
s.
Some types of robots, such as robotic arm
Robotic arm
A mechanical arm is a robotic, usually programmable, with similar functions to a human arm. The links of such a manipulator are connected by joints allowing either rotational motion or translational displacement. The links of the manipulator can be considered to form a kinematic chain...
s, can be articulated or non-articulated.
Definitions
Articulated Robot:See Figure. An articulated robot is one which uses rotary joints to access its work space.
Usually the joints are arranged in a “chain”, so that one joint supports another further in the chain.
Continuous Path:
A control scheme whereby the inputs or commands specify every point along a desired path of motion. The path is controlled by the coordinated motion of the manipulator joints.
Degrees Of Freedom (DOF):
The number of independent motions in which the end effector can move, defined by the number of axes of motion of the manipulator.
Gripper:
A device for grasping or holding, attached to the free end of the last manipulator link; also called the robot’s hand or end-effector.
Payload:
The maximum payload is the amount of weight carried by the robot manipulator at reduced speed while maintaining rated precision. Nominal payload is measured at maximum speed while maintaining rated precision. These ratings are highly dependent on the size and shape of the payload.
Pick And Place Cycle:
See Figure. Pick and place Cycle is the time, in seconds, to execute the following motion sequence: Move down one inch, grasp a rated payload; move up one inch; move across twelve inches; move down one inch; ungrasp; move up one inch; and return to start location.
Reach:
The maximum horizontal distance from the center of the robot base to the end of its wrist.
Accuracy:
See Figure. The difference between the point that a robot is trying to achieve and the actual resultant position. Absolute accuracy is the difference between a point instructed by the robot control system and the point actually achieved by the manipulator arm, while repeatability is the cycle-to-cycle variation of the manipulator arm when aimed at the same point.
Repeatability:
See Figure. The ability of a system or mechanism to repeat the same motion or achieve the same points when presented with the same control signals. The cycle-to-cycle error of a system when trying to perform a specific task
Resolution:
See Figure. The smallest increment of motion or distance that can be detected or controlled by the control system of a mechanism.
The resolution of any joint is a function of encoder pulses per revolution and drive ratio, and dependent on the distance between the tool center point and the joint axis.
Robot Program:
A robot communication program for IBM and compatible personal computers. Provides terminal emulation and utility functions. This program can record all of the user memory, and some of the system memory to disk files.
Maximum Speed:
The compounded maximum
speed of the tip of a robot moving at full extension with all joints moving simultaneously in complimentary directions. This speed is the theoretical maximum and should under no circumstances be used to estimate cycle time for a particular application. A better measure of real world speed is the standard twelve inch pick and place cycle time. For critical applications, the best indicator of achievable cycle time is a physical simulation.
Servo Controlled:
Controlled by a driving signal
which is determined by the error between the mechanism's present position and the desired output position.
Via Point:
A point through which the robot's tool should pass without stopping; via points are programmed in order to move beyond obstacles or to bring the arm into a lower inertia posture for part of the motion.
Work Envelope:
A three-dimensional
shape that defines the boundaries that the robot manipulator can reach; also known as reach envelope.
See also
- ClampClamp (tool)A clamp is a fastening device to hold or secure objects tightly together to prevent movement or separation through the application of inward pressure...
- Degrees of freedom (engineering)Degrees of freedom (engineering)In mechanics, degrees of freedom are the set of independent displacements and/or rotations that specify completely the displaced or deformed position and orientation of the body or system...
- Electric motorElectric motorAn electric motor converts electrical energy into mechanical energy.Most electric motors operate through the interaction of magnetic fields and current-carrying conductors to generate force...
- European Robotic ArmEuropean Robotic ArmThe European Robotic Arm is a robotic arm to be attached to the Russian Segment of the International Space Station. It will be the first robot arm able to work on the Russian space station segments, and will supplement the two Russian Strela cargo cranes that are already installed on the Pirs...
- Robotics suiteRobotics suiteA robotics suite is a visual environment for robot control and simulation. They are typically an end-to-end platform for robotics development and include tools for visual programming and creating and debugging robot applications...
- Industrial robotIndustrial robotAn industrial robot is defined by ISO as an automatically controlled, reprogrammable, multipurpose manipulator programmable in three or more axes...