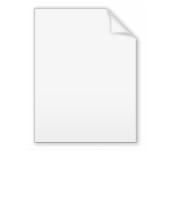
SolidCAM
Encyclopedia
SolidCAM provides CNC manufacturing customers with a full suite of CAM software modules for 2.5D Milling, High Speed Surface milling, 3D Milling/High-Speed Machining, Multi-sided Indexial 4/5 axes Milling, Simultaneous 5 axes Milling, Turning, Turn-Mill and WireEDM.
SolidCAM's latest iMachining technology can save up to 70% in machining time and increase tool life dramatically.
SolidCAM provides complete CAD integration, with seamless, single-window integration and full associativity to SolidWorks and Autodesk Inventor (InventorCAM). The integration ensures the automatic update of tool paths for CAD revisions.
Today SolidCAM has more than 15,500 seats installed and is sold by a reseller network in 50 countries worldwide.
The integration strategy of SolidCAM, in the major 3D mainstream CAD systems, SolidWorks and Inventor, has created major growth for SolidCAM and established SolidCAM as the leaders in Integrated CAM.
SolidCAM has the Certified Gold-product status from SolidWorks since 2003 and provides seamless, single-window integration and full associativity to the SolidWorks design model.
InventorCAM has the Autodesk certified product status and provides seamless, single-window integration and full associativity to the Inventor design model.
With the single-window integration of SolidCAM in SolidWorks and Inventor, all machining operations can be defined, calculated and verified without leaving the host CAD environment. All geometries used for machining are fully associative to the SolidWorks and Inventor design model.
A breakthrough in CNC Milling tool path technology that allows cutting 2 to 3 times faster and deeper, by optimizing tool cutting angles and feeds through the entire tool path. Using existing CNC milling machines, iMachining enables the user to cut faster and deeper, with even the smallest cutting tools, in the hardest materials.
iMachining uses a patent-pending "Technology Wizard" that guides users through all steps to optimize the production job. With the Wizard, iMachining uses the tool data, together with geometry, material and CNC machine properties, to generate smooth morphing spiral toolpaths, that ensure constant cutting force on the tool. The calculated CNC-programs avoids continuous repositioning and time-consuming air cutting movements like insertion, retraction and withdrawing.
The results are significantly higher metal removal rates and also reduced load and wear on the tools and CNC machines. Users enjoy shorter cutting-times for increased CNC machine productivity, longer cutting tool life, better machining process, reduced CNC machine wear and the best surface machining quality.
SolidCAM provides both interactive and automated 2.5D milling operations on the solid model. SolidCAM supports profile and pocket rest material machining, thread milling, undercut
slots with T-Slot tools and all other 2.5D milling needs. SolidCAM's automatic hole and pocket feature-recognition and machining module automates the manufacturing of parts with multiple pockets, multiple drills and complex holes.
The HSS Module is a High Speed Surface Machining Module, for smooth machining of localized surface areas in the part, including undercuts. It provides easy selection of the surfaces to be machined, with no need to define the boundaries. It supports both standard and shaped tools.The linking moves between the Toolpaths can be controlled by the user to avoid holes and slots, without the need to modify the Model Surface.Complete Gouge Control is available for holder, arbor and tool. Adjoining check surfaces that are to be avoided can be selected. Several Retract Strategies are available, under user control.The HSS Module is essential for each manufacturing facility as a complementary module for the machining of all types of parts.
SolidCAM HSM module is an advanced 3D Mill and high-speed-machining module for 3D parts, aerospace parts and molds, tools and dies. The HSM module offers unique machining
and linking strategies for generating advanced 3D Mill and high-speed toolpaths. SolidCAM’s HSM module smooths the paths of both cutting moves and retracts wherever possible to maintain a continuous machine tool motion – an essential requirement for maintaining higher feedrates and eliminating dwelling. With SolidCAM HSM module retracts to high Z levels are kept to a minimum. Angled where possible, smoothed by arcs, retracts do not go any higher than necessary – thus minimizing aircutting and reducing machining time. The result of the HSM module is an efficient, smooth, and optimal toolpath. This translates to increased surface quality, less wear on cutters, and a longer life for your machine tools.
With SolidCAM, programming and machining of multi-sided parts on 4- and 5-Axis machining centers is easy and efficient. SolidCAM rotates the design model to the user-defined machining planes and automatically calculates all necessary shifts and tilts for the 3D machining coordinate systems.
SolidCAM enables flexible set-ups and reduces the need for special clamping jigs. All 2.5D and 3D machining operations on any face can be defined and checked using SolidCAM’s tool path verification. The output is ready-to-run programs for the 4/5-axis CNC-machine.
SolidCAM provides various 5-axis machining strategies, including swarfing and trimming, for machining of complex geometry parts including mold cores and cavities, aerospace parts, cutting tools, cylinder heads, turbine blades and impellers. SolidCAM provides a realistic simulation of the complete machine tool, enabling collision checking between the tool and the machine components.
SolidCAM supports all the latest multi-function CNC machines for combined milling and turning, including multi-turret and multi-spindle programming with full machine simulation.
The integrated Mill-Turn capability enables the turning and milling operations to be programmed in the same environment. Access to the complete 2.5D to 5 axis milling is available.
SolidCAM Wire EDM handles profiles and tapers with constant and variable angles, as well as 4-axis contours. SolidCAM provides full user control of stop-points and of wire cutting conditions at any point of the profile or taper.
SolidCAM's latest iMachining technology can save up to 70% in machining time and increase tool life dramatically.
SolidCAM provides complete CAD integration, with seamless, single-window integration and full associativity to SolidWorks and Autodesk Inventor (InventorCAM). The integration ensures the automatic update of tool paths for CAD revisions.
Founder and History
SolidCAM was founded in 1984 by its current Managing Director, Dr. Emil Somekh, a veteran of 41 years in CAD/CAM development and applications. SolidCAM's current products are SolidCAM 2011 and InventorCAM 2012. SolidCAM and InventorCAM are noted for their ease of use, combined with complete CAM functionality and customized postprocessors that generate ready-to-go CNC-code.Market
SolidCAM's CAM products supports the complete range of manufacturing applications used in mechanical manufacturing, electronics, medical, consumer products, machine design, automotive and aerospace industries, in mold, tool and die and rapid prototyping shops.Today SolidCAM has more than 15,500 seats installed and is sold by a reseller network in 50 countries worldwide.
CAD Integration strategy
SolidCAM's CAM software provides seamless single-window integration and full associativity in the following CAD systems:- SolidWorksSolidWorksSolidWorks is a 3D mechanical CAD program that runs on Microsoft Windows and is being developed by Dassault Systèmes SolidWorks Corp., a subsidiary of Dassault Systèmes, S. A. . SolidWorks is currently used by over 1.3 million engineers and designers at more than 130,000 companies worldwide...
- SolidCAM - Autodesk InventorAutodesk InventorAutodesk Inventor, developed by U.S.-based software company Autodesk, is 3D mechanical solid modeling design software for creating 3D digital prototypes used in the design, visualization and simulation of products...
- InventorCAM
The integration strategy of SolidCAM, in the major 3D mainstream CAD systems, SolidWorks and Inventor, has created major growth for SolidCAM and established SolidCAM as the leaders in Integrated CAM.
SolidCAM has the Certified Gold-product status from SolidWorks since 2003 and provides seamless, single-window integration and full associativity to the SolidWorks design model.
InventorCAM has the Autodesk certified product status and provides seamless, single-window integration and full associativity to the Inventor design model.
With the single-window integration of SolidCAM in SolidWorks and Inventor, all machining operations can be defined, calculated and verified without leaving the host CAD environment. All geometries used for machining are fully associative to the SolidWorks and Inventor design model.
Available CAM modules
- iMachining
A breakthrough in CNC Milling tool path technology that allows cutting 2 to 3 times faster and deeper, by optimizing tool cutting angles and feeds through the entire tool path. Using existing CNC milling machines, iMachining enables the user to cut faster and deeper, with even the smallest cutting tools, in the hardest materials.
iMachining uses a patent-pending "Technology Wizard" that guides users through all steps to optimize the production job. With the Wizard, iMachining uses the tool data, together with geometry, material and CNC machine properties, to generate smooth morphing spiral toolpaths, that ensure constant cutting force on the tool. The calculated CNC-programs avoids continuous repositioning and time-consuming air cutting movements like insertion, retraction and withdrawing.
The results are significantly higher metal removal rates and also reduced load and wear on the tools and CNC machines. Users enjoy shorter cutting-times for increased CNC machine productivity, longer cutting tool life, better machining process, reduced CNC machine wear and the best surface machining quality.
- 2.5D Milling
SolidCAM provides both interactive and automated 2.5D milling operations on the solid model. SolidCAM supports profile and pocket rest material machining, thread milling, undercut
Undercut (manufacturing)
In manufacturing, an undercut is a special type of recessed surface. In turning it refers to a recess in a diameter. In machining it refers to a recess in a corner. In molding it refers to a feature that cannot be molded using only a single pull mold...
slots with T-Slot tools and all other 2.5D milling needs. SolidCAM's automatic hole and pocket feature-recognition and machining module automates the manufacturing of parts with multiple pockets, multiple drills and complex holes.
- High Speed Surface Machining (HSS)
The HSS Module is a High Speed Surface Machining Module, for smooth machining of localized surface areas in the part, including undercuts. It provides easy selection of the surfaces to be machined, with no need to define the boundaries. It supports both standard and shaped tools.The linking moves between the Toolpaths can be controlled by the user to avoid holes and slots, without the need to modify the Model Surface.Complete Gouge Control is available for holder, arbor and tool. Adjoining check surfaces that are to be avoided can be selected. Several Retract Strategies are available, under user control.The HSS Module is essential for each manufacturing facility as a complementary module for the machining of all types of parts.
- 3D Mill/High-Speed Machining (HSM)
SolidCAM HSM module is an advanced 3D Mill and high-speed-machining module for 3D parts, aerospace parts and molds, tools and dies. The HSM module offers unique machining
and linking strategies for generating advanced 3D Mill and high-speed toolpaths. SolidCAM’s HSM module smooths the paths of both cutting moves and retracts wherever possible to maintain a continuous machine tool motion – an essential requirement for maintaining higher feedrates and eliminating dwelling. With SolidCAM HSM module retracts to high Z levels are kept to a minimum. Angled where possible, smoothed by arcs, retracts do not go any higher than necessary – thus minimizing aircutting and reducing machining time. The result of the HSM module is an efficient, smooth, and optimal toolpath. This translates to increased surface quality, less wear on cutters, and a longer life for your machine tools.
- Multi-sided Indexial 4/5 axes Milling
With SolidCAM, programming and machining of multi-sided parts on 4- and 5-Axis machining centers is easy and efficient. SolidCAM rotates the design model to the user-defined machining planes and automatically calculates all necessary shifts and tilts for the 3D machining coordinate systems.
SolidCAM enables flexible set-ups and reduces the need for special clamping jigs. All 2.5D and 3D machining operations on any face can be defined and checked using SolidCAM’s tool path verification. The output is ready-to-run programs for the 4/5-axis CNC-machine.
- Simultaneous 5 axes Milling
SolidCAM provides various 5-axis machining strategies, including swarfing and trimming, for machining of complex geometry parts including mold cores and cavities, aerospace parts, cutting tools, cylinder heads, turbine blades and impellers. SolidCAM provides a realistic simulation of the complete machine tool, enabling collision checking between the tool and the machine components.
- Turning and Mill-Turn
SolidCAM supports all the latest multi-function CNC machines for combined milling and turning, including multi-turret and multi-spindle programming with full machine simulation.
The integrated Mill-Turn capability enables the turning and milling operations to be programmed in the same environment. Access to the complete 2.5D to 5 axis milling is available.
- WireEDM
SolidCAM Wire EDM handles profiles and tapers with constant and variable angles, as well as 4-axis contours. SolidCAM provides full user control of stop-points and of wire cutting conditions at any point of the profile or taper.