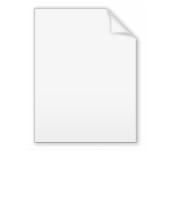
Snowmelt system
Encyclopedia
A snowmelt system is used to remove snow and ice via embedded electric cables or hydronic tubing. Common areas for snowmelt systems are: driveways, walkways, parking areas, stairways, loading docks, and around car washes. A snowmelt system is usually installed during the original construction in concrete, asphalt, or under pavers. Retrofit electric systems can also applied to existing concrete or asphalt using saw cutting technology.
has standards intended to achieve satisfactory results and to minimize energy consumption from over sizing or over designing a system. Systems are typically designed to produce 70-170 BTU/sqft using ASHRAE guidelines by region. The time to melt snow from a surface varies by storm and how many BTUs the system is designed to produce.
The heating cable is built to withstand harsh conditions to make it suitable for outdoor usage. The cable should be listed to UL standards by a Nationally Recognized Testing Laboratory
and many consist of a single or dual conductor with a protective coating and/or insulation. Many cables are rated at 220 °F (104.4 °C) and produce 6-50 watts per lineal foot. Watts per square foot produced is determined by heating element spacing.
The control units are typically wall-mounted control panels and can be mounted in a NEMA enclosure. Control units vary by technology by using line and load terminal blocks, relays, activation terminals, transformers, as well as monitoring electronics.
(antifreeze). The fluid is warmed to temperatures of 140 to 180 °F (82.2 °C) to warm surrounding concrete/asphalt/concrete pavers and melt snow and ice. Technology for hydronic snowmelt systems is based on the same technology as underfloor heating
systems.
There should be a minimum of 3” and max 4” of substrate covering the heating cables for new pour applications. Concrete mixture must not contain sharp stones as these may damage the cable. The concrete should be allowed to set for 30 days before the heating cables are turned on. For this reason, the best installation time is during summer months.
Insulation is recommended, but not required. One-inch rigid insulation can be installed underneath the base surface, or it can be laid on the base surface and the heating cable can be secured on top of the insulation.
Some installations involve two layers of asphalt. For this installation, a base layer of asphalt (1" thick) is placed down first. Heating cables are then installed and secured to the surface of the base layer. Once the heating cables are installed, a second layer of asphalt is poured over the heating cables and the first layer, embedding the heating cables within the slab.
or sealant is applied 1/4" thick at the surface of the groove. For concrete, a special polyurethane based sealant is recommended. For asphalt, a special silicon based sealant is recommended. The Silicon sealant is currently not available.
Like electric snowmelt systems, hydronic snowmelt systems must be installed in the base surface material (sand or compacted crush stone). Ensure the subgrade is well compacted before beginning tube installation. Tubing can be fastened with cable ties to either the re-mesh, re-bar or below slab insulation.
Hydronic tubes should not be placed directly on top of solid bedrock; this will cause the heating tubes to conduct heat into the earth.
Maintenance
Arguably, an electric snowmelt system requires less maintenance than a hydronic snowmelt system because there are no moving parts or corroding agents like water used to operate the system. A snowmelt system may extend the life of the concrete, asphalt or under pavers by eliminating the use of harsh salts and chemicals, and damage from snow removal devices.Aesthetics
A snowmelt system is not visible when installed and does not add extra height or require additional materials than a standard concrete, asphalt or under paver pour.Efficiency
Most new snowmelt systems operate in conjunction with an automatic activation device that will trigger the system on when it senses precipitation and freezing temperatures. These types of devices ensure the system is only on during useful periods and reduces wasteful energy consumption.Environmentally friendly
Snowmelt systems are environmentally friendly compared to the use of salt and chemicals to melt the snow, which causes calcium chloride to run into rivers and watersheds. Current systems are more cost effective in the long run than continual salt dumping and removal, and reduce waste by extending the life of the cement.Low operation costs
Operating costs vary by region, energy source (electric, gas, propane, etc.) used and costs associated. The ASHRAE(American Society of Heating, Refrigeration and Air Conditioning Engineers)American Society of Heating, Refrigerating and Air-Conditioning Engineers
The American Society of Heating, Refrigerating and Air Conditioning Engineers is an international technical society for all individuals and organizations interested in heating, ventilation, air-conditioning, and refrigeration...
has standards intended to achieve satisfactory results and to minimize energy consumption from over sizing or over designing a system. Systems are typically designed to produce 70-170 BTU/sqft using ASHRAE guidelines by region. The time to melt snow from a surface varies by storm and how many BTUs the system is designed to produce.
Electric snowmelt systems
Electric snowmelt systems are composed of three basic components: heating cable, control unit and an activation device.The heating cable is built to withstand harsh conditions to make it suitable for outdoor usage. The cable should be listed to UL standards by a Nationally Recognized Testing Laboratory
Nationally Recognized Testing Laboratories
A Nationally Recognized Testing Laboratory is a testing facility recognized by OSHA as primarily private sector organizations that provide product safety testing and certification services to manufacturers. The testing and certification are done, for purposes of the Program, to U.S. consensus-based...
and many consist of a single or dual conductor with a protective coating and/or insulation. Many cables are rated at 220 °F (104.4 °C) and produce 6-50 watts per lineal foot. Watts per square foot produced is determined by heating element spacing.
The control units are typically wall-mounted control panels and can be mounted in a NEMA enclosure. Control units vary by technology by using line and load terminal blocks, relays, activation terminals, transformers, as well as monitoring electronics.
Hydronic snowmelt systems
The heating element in a hydronic system is a closed-loop tubing made of a flexible polymer or synthetic rubber that circulates a mixture of hot water and propylene glycolPropylene glycol
Propylene glycol, also called 1,2-propanediol or propane-1,2-diol, is an organic compound with formula C3H8O2 or HO-CH2-CHOH-CH3...
(antifreeze). The fluid is warmed to temperatures of 140 to 180 °F (82.2 °C) to warm surrounding concrete/asphalt/concrete pavers and melt snow and ice. Technology for hydronic snowmelt systems is based on the same technology as underfloor heating
Underfloor heating
Underfloor heating and cooling is a form of central heating and cooling which achieves indoor climate control for thermal comfort using conduction, radiation and convection...
systems.
Activation Devices
There are a number of activation devices used for snow melting applications. Some activators are a simple manual timer that activate the system to stay on for a specified time period while others sense temperature and moisture or just temperature conditions to automatically activate the snow melt system. Automatic devices can be aerial-mounted, pavement mounted or gutter mounted. High-end activation devices feature: adjustable temperature trigger points, adjustable delay off cycle, and upgradeable remote activation. The activation device enables the snowmelt system to run 100% automated.Installation
Installation for both hydronic and electric snowmelt systems should begin as close as possible to the electrical. Use care to ensure the tubing and cables are spaced evenly over the entire area to be heated. It is not required to install the heating cables or tubes beneath the entire surface of the area. More economical installations heat only a pair of 2 foot (0.6096 m)-wide tire tracks on a driveway or a 3 foot (0.9144 m) center portion of a sidewalk, etc.Concrete – new pour
Proceed with standard method of pouring concrete. The heating cable is secured to the re-mesh with wire ties at intervals of 3-9”, concrete is then poured on top of the heating cables. Spacing of cables will vary by the watts per lineal foot that the cable produces.There should be a minimum of 3” and max 4” of substrate covering the heating cables for new pour applications. Concrete mixture must not contain sharp stones as these may damage the cable. The concrete should be allowed to set for 30 days before the heating cables are turned on. For this reason, the best installation time is during summer months.
Asphalt - new
Not all snowmelt systems can withstand the heat and compression of newly poured asphalt. Check manufacturer recommendations before proceeding with an asphalt installation. The cable can be laid out on the base surface (usually a sand bed), and covered with 1/2" sand. The asphalt is then hand shoveled onto the heating cable and base surface.Insulation is recommended, but not required. One-inch rigid insulation can be installed underneath the base surface, or it can be laid on the base surface and the heating cable can be secured on top of the insulation.
Some installations involve two layers of asphalt. For this installation, a base layer of asphalt (1" thick) is placed down first. Heating cables are then installed and secured to the surface of the base layer. Once the heating cables are installed, a second layer of asphalt is poured over the heating cables and the first layer, embedding the heating cables within the slab.
Brick paver – new
Installing a snowmelt system under brick pavers is achieved by placing the heating cables on the base surface over 1/2" of sand. The heating cables are then covered with 1/2" of sand and the pavers are installed as normal over the sand bed.Retrofit(Saw Cut) into existing surfaces
Retrofit is an option to install an electric snow melt systems on existing surfaces. The system can be designed to cover any specified area. Chalk lines are used to mark the runs of heating element onto the surface and covered with a clear lacquer or acrylic spray to waterproof the chalk marks. Waterproofing is important so the lines can be visually seen and unaffected by the water used during the cutting process. Depending on the cable used, saw cuts can be 1" to 1" deep and between 1/4" and 3/8" wide. Once the saw cutting is finished, a power washer is used to clean the surface and grooves in preparation for the heating cables. Heating cables are placed into the groove and covered with a foam (backer rod) insulation and a caulkingCaulking
Caulking is one of several different processes to seal joints or seams in various structures and certain types of piping. The oldest form of caulking is used to make the seams in wooden boats or ships watertight, by driving fibrous materials into the wedge-shaped seams between planks...
or sealant is applied 1/4" thick at the surface of the groove. For concrete, a special polyurethane based sealant is recommended. For asphalt, a special silicon based sealant is recommended. The Silicon sealant is currently not available.
Activation Devices
There are many activators to choose from. Automatic activation devices are the eyes and ears of the snow melting system. Careful placement of the sensors is important to have and effective result when using these activators. Activation moisture sensors should be placed in a location where they will effectively collect any moisture from a snow storm and in a relatively close proximity to the area to be free of snow and ice. Temperature sensors are installed outside to sense the same temperature conditions that the surface that the snow melting system will experience. Other activators, such as manual timers or switches can be installed in a convenient location.Hydronic snowmelt systems
The most crucial part of a successful hydronic heating system depends on proper tube spacing and layout. It is recommended to lay the tubes in a spiral or serpentine pattern to help distribute the heat evenly. Specification for spacing will vary between manufacturers. A faster rate of snowmelting will require closer spacing of tubing, typical spacing is 6”. Another heat factor is the amount of insulation used under the slab.Like electric snowmelt systems, hydronic snowmelt systems must be installed in the base surface material (sand or compacted crush stone). Ensure the subgrade is well compacted before beginning tube installation. Tubing can be fastened with cable ties to either the re-mesh, re-bar or below slab insulation.
Hydronic tubes should not be placed directly on top of solid bedrock; this will cause the heating tubes to conduct heat into the earth.