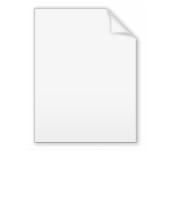
Modular home
Encyclopedia
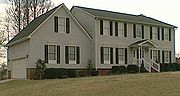
House
A house is a building or structure that has the ability to be occupied for dwelling by human beings or other creatures. The term house includes many kinds of different dwellings ranging from rudimentary huts of nomadic tribes to free standing individual structures...
s that consist of multiple modules or sections which are built in a remote facility and then delivered to their intended site of use. The modules are assembled into a single residential building using either a crane or trucks.
Modular buildings are considerably different from mobile home
Mobile home
Mobile homes or static caravans are prefabricated homes built in factories, rather than on site, and then taken to the place where they will be occupied...
s or manufactured homes. Off-frame modular dwellings differ from mobile homes largely in their absence of axles or a frame, meaning that they are typically transported to their site by means of flat-bed truck
Truck
A truck or lorry is a motor vehicle designed to transport cargo. Trucks vary greatly in size, power, and configuration, with the smallest being mechanically similar to an automobile...
s; however, some modular dwellings are built on a steel frame (on-frame modular) that can be used for transportation to the site. Many modular homes have multiple levels. Homes are often set in place using a crane
Crane (machine)
A crane is a type of machine, generally equipped with a hoist, wire ropes or chains, and sheaves, that can be used both to lift and lower materials and to move them horizontally. It uses one or more simple machines to create mechanical advantage and thus move loads beyond the normal capability of...
.
Uses
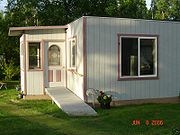
Construction process
Modular components are typically constructed indoors on assembly lines. An assembly line track moves the modules from one workstation to the next. Independent building inspectors are on site to supervise the construction and ensure that all building codes are adhered to during assembly. While modules can take one to three months to be constructed, they can take as little as 10 days. They are transported to the building site and assembled by a crane. The placement of the modules may take from several hours to several days. Once assembled, modular buildings are essentially indistinguishable from typical site-built structures. While mobile manufactured buildings often decrease in value over time, a well-built modular building should have the same longevity as its site-built counterpart, increasing in value over time.Advantages
Modular buildings are very affordable because of the factory construction of these buildings. They are very cost effective compared to conventional construction. These units are typically constructed in an enclosed facility, therefore weather is not a factor in the construction timeline. Material delivery fees are also out of the equation because an ample amount of material will always be available at the facility, as opposed to being delivered in limited quantities to the job site, nearly eliminating construction delays, and theft of building materials from the site.Such dwellings are often priced lower than their site-built counterparts and are typically more cost-effective to builders and consumers. Homes can be constructed in less time than it takes to build a home "on-site."
Manufacturers cite the following reasons for the typically lower cost/price of these dwellings:
- Speed of construction/faster return on investment. Modular construction allows for the building and the site work to be completed simultaneously, reducing the overall completion schedule by as much as 50%.
- Indoor construction. Assembly is independent of weather, which increases work efficiency and avoids damaged building material.
- Favorable pricing from suppliers. Large-scale manufacturers can effectively bargain with suppliers for discounts on materials.
- Ability to service remote locations. Particularly in countries such as Australia there can be much higher costs to build a site-built house in a remote area or an area experiencing a construction boom such as mining towns. Modular homes can be built in major towns and sold to regional areas.
- Low waste. With the same plans being constantly built, the manufacturer has records of exactly what quantity of materials are needed for a given job. While waste from a site-built dwelling may typically fill several large dumpsters, construction of a modular dwelling generates much less waste.
- Environmentally friendly construction process. Modular construction reduces waste and site disturbance compared to site-built structures.
- Flexibility. Conventional buildings can be difficult to extend, however with a modular building you can simply add sections, or even entire floors
Market acceptance
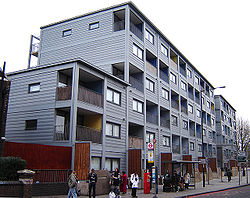
Modular homes vs. mobile homes
Differences include the building codes that govern the construction, types of material used and how they are appraised by banks for lending purposes. The codes that govern the construction of modular homes are exactly the same codes that govern the construction of site-constructed homes. In the United States, all modular homes are constructed according to the International Building CodeInternational Building Code
The International Building Code is a model building code developed by the International Code Council . It has been adopted throughout most of the United States.-History:...
(IBC), IRC, BOCA or the code that has been adopted by the local jurisdiction.
Mobile homes (manufactured homes) are constructed according to the HUD Code and are generally considered lesser quality. The materials are the same as site constructed homes. Wood-frame floors, walls and roof are the most typical. Some modular homes include brick or stone exteriors, granite counters and steeply pitched roofs. All modulars are designed to sit on a perimeter foundation or basement. Mobile homes are constructed with a steel chassis that is integral to the integrity of the floor system. Mobile homes often require special lenders. Most companies have standard plans. However, all modular buildings can be custom built to a clients specifications. Today's designs include multi-story units, multi-family units and entire apartment complexes. The negative stereotype commonly associated with mobile homes and has prompted some manufacturers to start using the term "off-site construction."
Standards and zoning considerations
Typically, modular dwellings are built to local, state or council code: dwellings built in a given manufacturing facility will have differing construction standards depending on the final destination of the modules. Steel and/or wood framing are common options for building a modular home. Modular home designs can be customized for local zoning codes. For example, homes built for final assembly in a hurricane-prone area may include additional bracing to meet local building codes.Some US courts have ruled that zoning
Zoning
Zoning is a device of land use planning used by local governments in most developed countries. The word is derived from the practice of designating permitted uses of land based on mapped zones which separate one set of land uses from another...
restrictions applicable to mobile homes do not apply to modular homes since modular homes are often assembled with a permanent foundation. Additionally, in the US, valuation differences between modular homes and site-built homes are often negligible in real estate appraisal
Real estate appraisal
Real estate appraisal, property valuation or land valuation is the process of valuing real property. The value usually sought is the property's Market Value. Appraisals are needed because compared to, say, corporate stock, real estate transactions occur very infrequently...
practice; thus, modular homes can in some market areas (depending on local appraisal practices per Uniform Standards of Professional Appraisal Practice
Uniform Standards of Professional Appraisal Practice
Uniform Standards of Professional Appraisal Practice, commonly referred to by the acronym USPAP, can be considered the quality control standards applicable for real property, personal property, intangibles, and business valuation appraisal analysis and reports in the United States and its territories...
) be evaluated the same way as traditionally built dwellings of similar quality. In Australia manufactured home parks are governed by additional legislation that does not apply to permanent modular homes. Possible developments in equivalence between modular and site-built housing types for the purposes of real estate appraisal
Real estate appraisal
Real estate appraisal, property valuation or land valuation is the process of valuing real property. The value usually sought is the property's Market Value. Appraisals are needed because compared to, say, corporate stock, real estate transactions occur very infrequently...
s, financing and zoning may increase the sales of modular homes over time.
Building strength
According to manufacturers, modular homes are generally designed to be initially stronger than traditional homes by, for example, replacing nails with screws and adding glue to joints. This is supposed to help the modules maintain their structural integrity as they are transported on trucks to the construction site. Despite manufacturer claims that the modular home is initially built to be stronger than a traditional home, it is difficult to predict the final building strength since it needs to endure transportation stresses that traditional homes never experience.When FEMA studied the destruction wrought by Hurricane Andrew in Dade County Florida, they concluded that modular and masonry homes fared best compared to other construction.
Typically, a modular home contains about 10 to 20 percent more lumber compared to traditional stick-built homes. This is because modules need to be transported to the job site and the additional lumber helps keep them stable.
CE marking
The CE markCE mark
CE marking is a mandatory conformity mark for products placed on the market in the European Economic Area . With the CE marking on a product the manufacturer ensures that the product conforms with the essential requirements of the applicable EC directives...
is a construction norm that guaranties the user of mechanical resistance and strength of the structure. It is a label given by European community empowered authorities for end-to-end process mastering and traceability.
All manufacturing operations are being monitored and recorded:
- Suppliers have to be known and certified,
- Raw materials and goods being sourced are to be recorded by batch used,
- Elementary products are recorded and their quality is monitored,
- Assembly quality is managed and assessed on a step by step basis,
- When a modular unit is finished, a whole set of tests are performed and if quality standards are met, a unique number and EC stamp is attached to and on the unit.
- This ID and all the details are recorded in a database
Database
A database is an organized collection of data for one or more purposes, usually in digital form. The data are typically organized to model relevant aspects of reality , in a way that supports processes requiring this information...
dedicated to quality,
- At any time, the producer has to be able to answer and provide all the information from each step of the production of a single unit,
- The EC certification guaranties standards in terms of durability, resistance against wind and earthquakes.
Surfaces and finishes
Modular buildings can be assembled on top of multiple foundation surfaces, such as a crawl space, stilts (for areas that are prone to flooding), full basementBasement
__FORCETOC__A basement is one or more floors of a building that are either completely or partially below the ground floor. Basements are typically used as a utility space for a building where such items as the furnace, water heater, breaker panel or fuse box, car park, and air-conditioning system...
s or standard slab at grade. They can also be built to multi-story heights. Motels and other multi-family structures have been built using modular construction techniques.
The height that a modular structure can be built to depends on jurisdiction but a number of countries, especially in Asia, allow them to be built to 24 floors and possibly even more.
Exterior wall surfaces can be finalized in the plant production process or in the case of brick/stone veneers field applications may be the builders choice. Roof systems also can be apart of – separate from – applied in the field after the basic installation is completed.
See also
- Kit houseKit houseKit houses, also known as pre-cut houses, ready-cut houses, mail order homes, or catalog homes, were a type of prefabricated housing that was popular in the United States in the first half of the 20th century...
- Manufactured housingManufactured housingManufactured housing is a type of prefabricated housing that is largely assembled in factories and then transported to sites of use...
- NTA IncNTA IncNTA Inc is a nationally recognized testing laboratory and third party certification agency headquartered in Nappanee, Indiana, USA.- About NTA :NTA evaluates and certifies products for the residential and commercial building industry....
- Prefabricated homePrefabricated homePrefabricated homes, often referred to as prefab homes, are dwellings manufactured off-site in advance, usually in standard sections that can be easily shipped and assembled....
- Stick-built home
- ToterToterA Toter, or Mobile Home Toter is a tractor specifically designed for the modular and manufactured housing industries. Some toters are highly adapted for purposes of delivering or removing mobile homes on smaller home sites...
External links
- Modular Building Systems Association – National trade association representing the legislative and regulatory interests of the modular housing industry
- National Association of Home Builders (United States)
- National Modular Housing Council National Trade Association for the Modular Housing Industry
- Modular Building Institute – International trade association representing non residential modular construction professionals