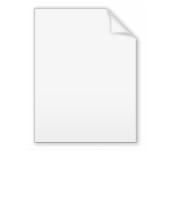
Kamov V-80
Encyclopedia
The Kamov V-80 was a design study designation for an attack helicopter that eventually evolved into the single seat Kamov Ka-50
family of aircraft.
Design of the V-80 (later Ka-50), began at the Kamov Helicopter Plant in January 1977. The program was run by the head of the design bureau, Chief Designer Sergei Mikheyev, who was later to become Designer General.
Kamov designers believed that combining the duties of flying, navigation, target detection, and tracking could be automated to a degree that a single crew member could perform all functions. Further, it was not expected that this would cause an excessive psychological and physical strain on the pilot. By the late seventies, the sophistication level of the Soviet helicopter industry ensured the building of such automatic systems was possible; even the Ka-25 and Ka-27 featured an automatic submarine search capability, automatic navigation and flight modes, automatic data exchange among the helicopters operating in the same flight, etc. A single-person crew would provide the benefits of weight reduction, better flight performance, reduce training costs and reduce the number of possible combat casualties.
One of the program priorities was to enhance the helicopter's survivability. With this goal in mind, the configuration and systems' arrangement were chosen, assemblies designed, and structural materials tested. The helicopter lacked a very vulnerable tail rotor as well as an intermediate and tail reduction gearbox and control rods. The following measures to enhance pilot survivability were taken:
• The engines were placed on both sides of the airframe to prevent a single hit from destroying both engines
• The helicopter could fly on a single engine in various modes
• The cockpit was armored and screened with combined steel/aluminum armor and armored Plexiglas
• The hydraulic steering system compartment was armored and screened
• Vital units were screened by less important ones
• Self-sealing fuel tanks were filled with polyurethane
• Composites were used to preserve the helicopter's efficiency when its load-carrying elements are damaged
• A two-contour rotor-blade spar was developed
• Control rod diameter was increased by positioning most of them inside the armored cockpit
• The powerplant and compartments adjacent to the fuel tanks were fire-protected
• The transmission is capable of operating for 30 minutes if the oil system is damaged
• The power supply systems, control circuits, etc. were made redundant and placed on opposite sides of the airframe
• Individual protection is provided to the pilot
The armor consisted of spaced-aluminum plates with a total weight of more than 300 kg. The armor is fitted into the fuselage load-bearing structure, which reduces the total weight of the helicopter. GosNIIAS tests confirmed the pilot's protection up to 20mm caliber cannon rounds and shell fragments.
A unique feature of this helicopter is the use of a rocket-parachute ejection system in case of an emergency. The helicopter emergency-escape system uses the K-37-800 ejection seat that was developed by the Zvezda Scientific Production Association (Chief Designer Guy Severin). The pilot's safety was also ensured by the undercarriage design. The undercarriage is capable of absorbing large loads in an emergency landing, and the cockpit has a crunch zone of up to 10-15% upon impact. Additionally, the fuel system is designed to remove the possibility of fire after a rough landing.
A model of an earlier design from around 1975 shows a two seat aircraft with an airframe similar to that of the V-60, a pair of widely spaced downward facing vertical stabilisers, a fixed GSh-23L forward firing gun in the fuselage and two stub wings incorporating one hardpoint each and a pod containing the retractable undercarriage. Further studies include novel features such as a variable azimuth stub wing, a biplane stub wing/canard configuration, additional fuselage hardpoints, ejecting exhaust on either side of the tail to reduce the heat signature, making the forward firing gun depressible and single seat as well as two seat configurations. Specification weight was 4000 kg empty and 6500 kg takeoff.
The first V-80 prototype (Bort 010) left the Kamov Helicopter Plant in June 1982. On 17 June, for the first time, test pilot Nikolay Bezdetnov performed a hover in the V-80 and on 23 July the V-80 made its maiden forward flight.
The V-80Sh-1 prototype version was the configuration used for the Ka-50 production version. Production of the attack helicopter was ordered by the Soviet Council of Ministers on 14 December 1987. Following initial flight testing and system tests the Council ordered the first batch of the helicopter in 1990. The attack helicopter was first described publicly as the "Ka-50" in March 1992 at a symposium in the United Kingdom.
Kamov Ka-50
The Kamov Ka-50 "Black Shark" is a single-seat Russian attack helicopter with the distinctive coaxial rotor system of the Kamov design bureau. It was designed in the 1980s and adopted for service in the Russian army in 1995...
family of aircraft.
Design and development
By the mid-1970s, the Soviet Defense Ministry determined that the Mi-24 “Hind” attack helicopter (then the backbone of the Soviet Army Aviation) was not going to meet future Army requirements. Acting on the advice of the Ministry, the Central Committee of the Communist Party and the Council of Ministers of the Soviet Union passed a resolution on the development of a new-generation combat helicopter that could be fielded with the Soviet Army Aviation in the 1980s. The prospective helicopter's primary purpose was to destroy the armored forces close to the forward edge of battle area (FEBA). This resolution pitted competing programs run by N.I. Kamov and Ml. Mil's design bureaus against each other. At that time, both developers had already gained valuable experience in designing and producing rotary-wing aircraft.Design of the V-80 (later Ka-50), began at the Kamov Helicopter Plant in January 1977. The program was run by the head of the design bureau, Chief Designer Sergei Mikheyev, who was later to become Designer General.
Kamov designers believed that combining the duties of flying, navigation, target detection, and tracking could be automated to a degree that a single crew member could perform all functions. Further, it was not expected that this would cause an excessive psychological and physical strain on the pilot. By the late seventies, the sophistication level of the Soviet helicopter industry ensured the building of such automatic systems was possible; even the Ka-25 and Ka-27 featured an automatic submarine search capability, automatic navigation and flight modes, automatic data exchange among the helicopters operating in the same flight, etc. A single-person crew would provide the benefits of weight reduction, better flight performance, reduce training costs and reduce the number of possible combat casualties.
One of the program priorities was to enhance the helicopter's survivability. With this goal in mind, the configuration and systems' arrangement were chosen, assemblies designed, and structural materials tested. The helicopter lacked a very vulnerable tail rotor as well as an intermediate and tail reduction gearbox and control rods. The following measures to enhance pilot survivability were taken:
• The engines were placed on both sides of the airframe to prevent a single hit from destroying both engines
• The helicopter could fly on a single engine in various modes
• The cockpit was armored and screened with combined steel/aluminum armor and armored Plexiglas
• The hydraulic steering system compartment was armored and screened
• Vital units were screened by less important ones
• Self-sealing fuel tanks were filled with polyurethane
• Composites were used to preserve the helicopter's efficiency when its load-carrying elements are damaged
• A two-contour rotor-blade spar was developed
• Control rod diameter was increased by positioning most of them inside the armored cockpit
• The powerplant and compartments adjacent to the fuel tanks were fire-protected
• The transmission is capable of operating for 30 minutes if the oil system is damaged
• The power supply systems, control circuits, etc. were made redundant and placed on opposite sides of the airframe
• Individual protection is provided to the pilot
The armor consisted of spaced-aluminum plates with a total weight of more than 300 kg. The armor is fitted into the fuselage load-bearing structure, which reduces the total weight of the helicopter. GosNIIAS tests confirmed the pilot's protection up to 20mm caliber cannon rounds and shell fragments.
A unique feature of this helicopter is the use of a rocket-parachute ejection system in case of an emergency. The helicopter emergency-escape system uses the K-37-800 ejection seat that was developed by the Zvezda Scientific Production Association (Chief Designer Guy Severin). The pilot's safety was also ensured by the undercarriage design. The undercarriage is capable of absorbing large loads in an emergency landing, and the cockpit has a crunch zone of up to 10-15% upon impact. Additionally, the fuel system is designed to remove the possibility of fire after a rough landing.
A model of an earlier design from around 1975 shows a two seat aircraft with an airframe similar to that of the V-60, a pair of widely spaced downward facing vertical stabilisers, a fixed GSh-23L forward firing gun in the fuselage and two stub wings incorporating one hardpoint each and a pod containing the retractable undercarriage. Further studies include novel features such as a variable azimuth stub wing, a biplane stub wing/canard configuration, additional fuselage hardpoints, ejecting exhaust on either side of the tail to reduce the heat signature, making the forward firing gun depressible and single seat as well as two seat configurations. Specification weight was 4000 kg empty and 6500 kg takeoff.
The first V-80 prototype (Bort 010) left the Kamov Helicopter Plant in June 1982. On 17 June, for the first time, test pilot Nikolay Bezdetnov performed a hover in the V-80 and on 23 July the V-80 made its maiden forward flight.
The V-80Sh-1 prototype version was the configuration used for the Ka-50 production version. Production of the attack helicopter was ordered by the Soviet Council of Ministers on 14 December 1987. Following initial flight testing and system tests the Council ordered the first batch of the helicopter in 1990. The attack helicopter was first described publicly as the "Ka-50" in March 1992 at a symposium in the United Kingdom.