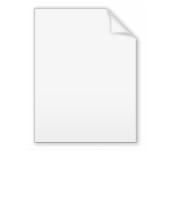
History of spray forming
Encyclopedia
Spray Forming – The Pioneering Years
Spray forming has now become very attractive to the metal industry because of its versatility and its capability of producing products with properties not easily obtainable by other means. This makes it especially suitable for items ranging from flat, extruded and forged products with fine grain size and correspondingly high mechanical properties to composite materials, large diameter billets in various alloys and ring shaped products in super alloys made by centrifugal spray forming. Progress began slowly as it was an entirely new technology. Even so, it soon increased rapidly and has now become so overwhelming that the early pioneering work is often forgotten. Many research fellows and research students at Swansea University and in industry were involved in the first 20 years and together laid the foundations for spray forming technology. In justice to them it is necessary to recognize their contribution.
Spray forming began as an offshoot of research on powder metallurgy that was proceeding at that time at Swansea University and a new process that was being developed at the Sketty Hall plant of the British Iron and Steel Research Association (BISRA) laboratories, under the direction of W N Jenkins. This latter process was designed to produce high quality thin strip from a range of steels. It used steel powder made into a slurry with a cellulose binder. This was spread on a flat substrate in a layer of uniform thickness, dried, cold rolled to consolidate, and then sintered. The product was thin strip of excellent appearance and properties, but the route contained too many steps and was too expensive. It was eventually abandoned.
It seemed to Prof Singer that a much shorter route was possible by gas atomizing molten metal and directing the spray on to a cool substrate from which it could be released and then consolidated by rolling or other means. Preliminary work showed that this was possible and the new route was termed spray rolling because of its mode of manufacture and to distinguish it from other forms of spray forming that were being considered at that time. Although it has now taken many forms, all of them can be traced back to 1966 when Prof Singer began research at Swansea University, funded by the Science Research Council (SRC) and aided by P. Jones who was in charge of the Departmental machine shop, constructed the first spray rolling equipment producing metal strip by depositing on a cool substrate, removing and then hot rolling in a separate operation.
The spray rolling equipment and the product were detailed in a paper in Metals and Materials June 1970. The equipment illustrated in this paper was a Mark I using a flat substrate, together with a Mark IV with twin continuously operating rolls capable of producing a strip either by depositing on one roll, or alternatively, in the nip of the rolls. Two types of atomizer were also illustrated together with the structure of the product. Aluminium alloy strip was produced up to 5m in length and 125mm in width. The new spray forming route devised by Singer seemed much more likely to be viable and was discussed with J. Brigenshaw of the National Research Development Corporation (NRDC) on 3rd April1968. NRDC had recently been set up by the Government as a means of encouraging innovation, and financially supporting University research in science directly related to industry. It also had a strong patent team to protect any promising process or product. Use was made of this patent facility when patents describing the basic features of spray forming and several ways of producing metal strip, both homogeneous and laminated, were filed by NRDC in 1968.
The early work was disclosed, in confidence, to Sir Charles Goodeve, the then director of BISRA on 11 June 1968, in view of its relationship to some of the current work of BISRA at its Swansea laboratories.
Between 1969 and 1974 several other PhD students began working with Singer on various aspects of spray forming at Swansea. Amongst them were S. Ozbek, S.E, Kisakurec, I. Davies, A. D. Roche, J. H. Tundermann, W N Jenkins, A. M. H. Alibhai and K. G. Watkins. The last, supported by the MOD, made some remarkable high strength aluminium alloy composites containing silicon carbide whiskers. Regrettably, this work had to be terminated even though it was a promising development, because of the high level of toxicity of the extremely fine whiskers and the absence of glove box facilities. This research was fully reported in his PhD thesis of 1975.
Another student, S. Ozbek, using an aluminium alloy as a basis and a spray co-deposition technique, produced strip incorporating silica, silicon carbide, alumina, chilled iron and graphite in various quantities and particle sizes. The friction and wear properties were examined and compared with conventional friction materials.
Kisakurek was concerned with centrifugal spray deposition (CSD) benefiting from the work at Harwell in 1976 in which super alloy powders were produced by centrifugal means. The new CSD process was further developed by Aurora Steels as set out below.
Roche investigated an entirely new process termed Simultaneous Spray Peening (SSP) that was shown to be particularly effective in producing high density, stress free coatings. A further use was the manufacture of tools and dies by making a hard electrodeposited shell on a plastic or ceramic pattern and then spray depositing on the shell which, when released made either a tool or a die. This concept was taken up by the Ford Motor Co for making large press tools and dies.
Idris Davies produced steel strip spray coated with aluminium from a liquid source using a scanning spray technique. The latter showed no intermetalics at the interface, had excellent bending properties and good adhesion, when the atmosphere during deposition was carefully controlled to retain reducing conditions. The work was supported by the Ford Motor Co and fully described in Davies’s thesis for an MSc degree in 1984 and in a paper in Metal Society World.
Another industrial company exploring spray forming was Davy-Ashmore. Sponsored by NRDC they erected a pilot plant at their R&D establishment at Bedford to produce aluminium alloy strip using inert gas atomization and three overlapping spray nozzles. The strip measured 6m x 0.5m x 10mm, was made in one pass at 6 m/min. Three materials were used, commercially pure aluminium, Al 5%Mg and Al 6% Cu. After rolling and heat treatment they showed fine grain size and good mechanical properties although thickness variations across the width were high at 5%. Subsequently it was realized that scanning of the spray would have been better.
Osprey Metals, founded in 1974 by Brooks, Leatham and Coombs began slowly with the manufacture of spray forgings and metal powders, but a rapid expansion followed and then it went on to become the most significant company in terms of the industrial development of spray forming. A particularly important innovation in conjunction with Alcan International was an ingenious way of making large billets by the vertical billet process. In this case an atomized spray was directed at an angle to the billet axis as it was rotated and withdrawn axially. By adjusting the angle it enabled billets of a wide range of diameters to be produced. For the first time industry was now able to produce large billets and ingots of both ferrous and non-ferrous metals having all the benefits of spray forming.
British Steel Electricals carried out pioneering work with the spray rolling of 6.5% silicon low carbon steels at their Orb Works. This is the optimum silicon content for electrical steel but it is virtually impossible to roll into strip form using a conventional ingot route when the maximum silicon content is 3.5%. G. Eadie found that by using a spray rolling technique, the very fine dispersion of silicon allowed the 6.5% product to be hot rolled to produce continuous strip up to 200mm width having excellent electrical properties.
Aurora Steels in Sheffield very courageously developed the CSD process to produce large rings over 1m in diameter weighing up to 2 tons. This was announced in 1980 when they reported superior properties compared with the ingot route. Their work was published in 1981 when they disclosed that they were about to scale up their work to produce even larger rings. Unfortunately the recession in the special steels industry at that time forced them to close, and they went into administration. In fact they were the last full-range tool steel manufacturer in this country to close. Practically all the existing rings were claimed by the liquidator as valuable scrap and sold for re-melting.
Fortunately some small pieces were salvaged and they confirmed the excellent structure and properties. This was a most unfortunate closure of Aurora as Singer always had in mind that the CSD process could be used for the manufacture of large diameter rings for jet engines. This has now occurred – twenty years later – and is widely in use. An important feature of CSD is that atomisation can be carried out in vacuum with the special benefit of reducing the hydrogen level in steel.
The new company was designed to operate with innovation and R&D only. It was financed by government bodies specifically interested in its work and by industries that wished to have certain of the concepts developed still further, before taking them into their own hands. It was joined by W N Jenkins from British Steel and by D. R. G. Davies from Aurora Steel. Because the new Company was intended to work on R&D only, it did not produce any material product for sale, although it had already collected and maintained a valuable patent portfolio. The Company was sold, together with its patent portfolio, to Alcan International in 1991. This ended research on spray forming at Swansea University.
In general terms, and from the author’s point of view, spray forming has been a well rewarded venture, in the sense that, from small beginnings, further development and important applications have proceeded in many parts of the world, making a major contribution to the metal, engineering and aeronautical industries.
Spray forming has now become very attractive to the metal industry because of its versatility and its capability of producing products with properties not easily obtainable by other means. This makes it especially suitable for items ranging from flat, extruded and forged products with fine grain size and correspondingly high mechanical properties to composite materials, large diameter billets in various alloys and ring shaped products in super alloys made by centrifugal spray forming. Progress began slowly as it was an entirely new technology. Even so, it soon increased rapidly and has now become so overwhelming that the early pioneering work is often forgotten. Many research fellows and research students at Swansea University and in industry were involved in the first 20 years and together laid the foundations for spray forming technology. In justice to them it is necessary to recognize their contribution.
Spray forming began as an offshoot of research on powder metallurgy that was proceeding at that time at Swansea University and a new process that was being developed at the Sketty Hall plant of the British Iron and Steel Research Association (BISRA) laboratories, under the direction of W N Jenkins. This latter process was designed to produce high quality thin strip from a range of steels. It used steel powder made into a slurry with a cellulose binder. This was spread on a flat substrate in a layer of uniform thickness, dried, cold rolled to consolidate, and then sintered. The product was thin strip of excellent appearance and properties, but the route contained too many steps and was too expensive. It was eventually abandoned.
It seemed to Prof Singer that a much shorter route was possible by gas atomizing molten metal and directing the spray on to a cool substrate from which it could be released and then consolidated by rolling or other means. Preliminary work showed that this was possible and the new route was termed spray rolling because of its mode of manufacture and to distinguish it from other forms of spray forming that were being considered at that time. Although it has now taken many forms, all of them can be traced back to 1966 when Prof Singer began research at Swansea University, funded by the Science Research Council (SRC) and aided by P. Jones who was in charge of the Departmental machine shop, constructed the first spray rolling equipment producing metal strip by depositing on a cool substrate, removing and then hot rolling in a separate operation.
Early Experimental Work
The early work was concerned with aluminum alloy strip that was produced continuously and was shown to have full density and good mechanical properties.The spray rolling equipment and the product were detailed in a paper in Metals and Materials June 1970. The equipment illustrated in this paper was a Mark I using a flat substrate, together with a Mark IV with twin continuously operating rolls capable of producing a strip either by depositing on one roll, or alternatively, in the nip of the rolls. Two types of atomizer were also illustrated together with the structure of the product. Aluminium alloy strip was produced up to 5m in length and 125mm in width. The new spray forming route devised by Singer seemed much more likely to be viable and was discussed with J. Brigenshaw of the National Research Development Corporation (NRDC) on 3rd April1968. NRDC had recently been set up by the Government as a means of encouraging innovation, and financially supporting University research in science directly related to industry. It also had a strong patent team to protect any promising process or product. Use was made of this patent facility when patents describing the basic features of spray forming and several ways of producing metal strip, both homogeneous and laminated, were filed by NRDC in 1968.
The early work was disclosed, in confidence, to Sir Charles Goodeve, the then director of BISRA on 11 June 1968, in view of its relationship to some of the current work of BISRA at its Swansea laboratories.
Subsequent Experimental Work
Several students now began working for PhD degrees on spray forming programmes under the direction of Prof Singer. All of them were financed either by SRC or by NRDC. Amongst them, notably, was Alan Leatham who began work in1969.and Gwyn Brooks who joined in1970. A PhD thesis by Leatham was presented in 1972 describing the structure and properties of some of the spray formed materials that had been produced in Swansea. These two research workers subsequently joined forces, and with J. Coombs who was a graduate of engineering at Swansea University, formed Osprey Metals at Neath, near Swansea, in 1974.Between 1969 and 1974 several other PhD students began working with Singer on various aspects of spray forming at Swansea. Amongst them were S. Ozbek, S.E, Kisakurec, I. Davies, A. D. Roche, J. H. Tundermann, W N Jenkins, A. M. H. Alibhai and K. G. Watkins. The last, supported by the MOD, made some remarkable high strength aluminium alloy composites containing silicon carbide whiskers. Regrettably, this work had to be terminated even though it was a promising development, because of the high level of toxicity of the extremely fine whiskers and the absence of glove box facilities. This research was fully reported in his PhD thesis of 1975.
Another student, S. Ozbek, using an aluminium alloy as a basis and a spray co-deposition technique, produced strip incorporating silica, silicon carbide, alumina, chilled iron and graphite in various quantities and particle sizes. The friction and wear properties were examined and compared with conventional friction materials.
Kisakurek was concerned with centrifugal spray deposition (CSD) benefiting from the work at Harwell in 1976 in which super alloy powders were produced by centrifugal means. The new CSD process was further developed by Aurora Steels as set out below.
Roche investigated an entirely new process termed Simultaneous Spray Peening (SSP) that was shown to be particularly effective in producing high density, stress free coatings. A further use was the manufacture of tools and dies by making a hard electrodeposited shell on a plastic or ceramic pattern and then spray depositing on the shell which, when released made either a tool or a die. This concept was taken up by the Ford Motor Co for making large press tools and dies.
Idris Davies produced steel strip spray coated with aluminium from a liquid source using a scanning spray technique. The latter showed no intermetalics at the interface, had excellent bending properties and good adhesion, when the atmosphere during deposition was carefully controlled to retain reducing conditions. The work was supported by the Ford Motor Co and fully described in Davies’s thesis for an MSc degree in 1984 and in a paper in Metal Society World.
Developments in Industry
During this time several industrial companies had taken up the concept of spray forming. These included GKN Vandervell who released information about their steel backed aluminium-lead plain bearings for cars at the Motor Show in 1982. These were produced by direct spray deposition of the two metals on to a specially prepared, heated and roughened steel strip. Adhesion was good and the bearing strip was produced continuously.Another industrial company exploring spray forming was Davy-Ashmore. Sponsored by NRDC they erected a pilot plant at their R&D establishment at Bedford to produce aluminium alloy strip using inert gas atomization and three overlapping spray nozzles. The strip measured 6m x 0.5m x 10mm, was made in one pass at 6 m/min. Three materials were used, commercially pure aluminium, Al 5%Mg and Al 6% Cu. After rolling and heat treatment they showed fine grain size and good mechanical properties although thickness variations across the width were high at 5%. Subsequently it was realized that scanning of the spray would have been better.
Osprey Metals, founded in 1974 by Brooks, Leatham and Coombs began slowly with the manufacture of spray forgings and metal powders, but a rapid expansion followed and then it went on to become the most significant company in terms of the industrial development of spray forming. A particularly important innovation in conjunction with Alcan International was an ingenious way of making large billets by the vertical billet process. In this case an atomized spray was directed at an angle to the billet axis as it was rotated and withdrawn axially. By adjusting the angle it enabled billets of a wide range of diameters to be produced. For the first time industry was now able to produce large billets and ingots of both ferrous and non-ferrous metals having all the benefits of spray forming.
British Steel Electricals carried out pioneering work with the spray rolling of 6.5% silicon low carbon steels at their Orb Works. This is the optimum silicon content for electrical steel but it is virtually impossible to roll into strip form using a conventional ingot route when the maximum silicon content is 3.5%. G. Eadie found that by using a spray rolling technique, the very fine dispersion of silicon allowed the 6.5% product to be hot rolled to produce continuous strip up to 200mm width having excellent electrical properties.
Aurora Steels in Sheffield very courageously developed the CSD process to produce large rings over 1m in diameter weighing up to 2 tons. This was announced in 1980 when they reported superior properties compared with the ingot route. Their work was published in 1981 when they disclosed that they were about to scale up their work to produce even larger rings. Unfortunately the recession in the special steels industry at that time forced them to close, and they went into administration. In fact they were the last full-range tool steel manufacturer in this country to close. Practically all the existing rings were claimed by the liquidator as valuable scrap and sold for re-melting.
Fortunately some small pieces were salvaged and they confirmed the excellent structure and properties. This was a most unfortunate closure of Aurora as Singer always had in mind that the CSD process could be used for the manufacture of large diameter rings for jet engines. This has now occurred – twenty years later – and is widely in use. An important feature of CSD is that atomisation can be carried out in vacuum with the special benefit of reducing the hydrogen level in steel.
Sprayforming Developments Ltd
In 1984, when Singer was about to retire from the headship of the Dept at Swansea University, he formed an R&D Company—Sprayforming Developments Ltd. Fortunately, up until that time all the specialised equipment used in the experimental work had been bought either by government bodies specifically for spray forming, or by industry. This equipment was therefore transferred to the newly built Innovation Centre at the University where work on spray forming was able to continue. This was particularly important for those post graduate students who had already embarked on this research for higher degrees.The new company was designed to operate with innovation and R&D only. It was financed by government bodies specifically interested in its work and by industries that wished to have certain of the concepts developed still further, before taking them into their own hands. It was joined by W N Jenkins from British Steel and by D. R. G. Davies from Aurora Steel. Because the new Company was intended to work on R&D only, it did not produce any material product for sale, although it had already collected and maintained a valuable patent portfolio. The Company was sold, together with its patent portfolio, to Alcan International in 1991. This ended research on spray forming at Swansea University.
In general terms, and from the author’s point of view, spray forming has been a well rewarded venture, in the sense that, from small beginnings, further development and important applications have proceeded in many parts of the world, making a major contribution to the metal, engineering and aeronautical industries.